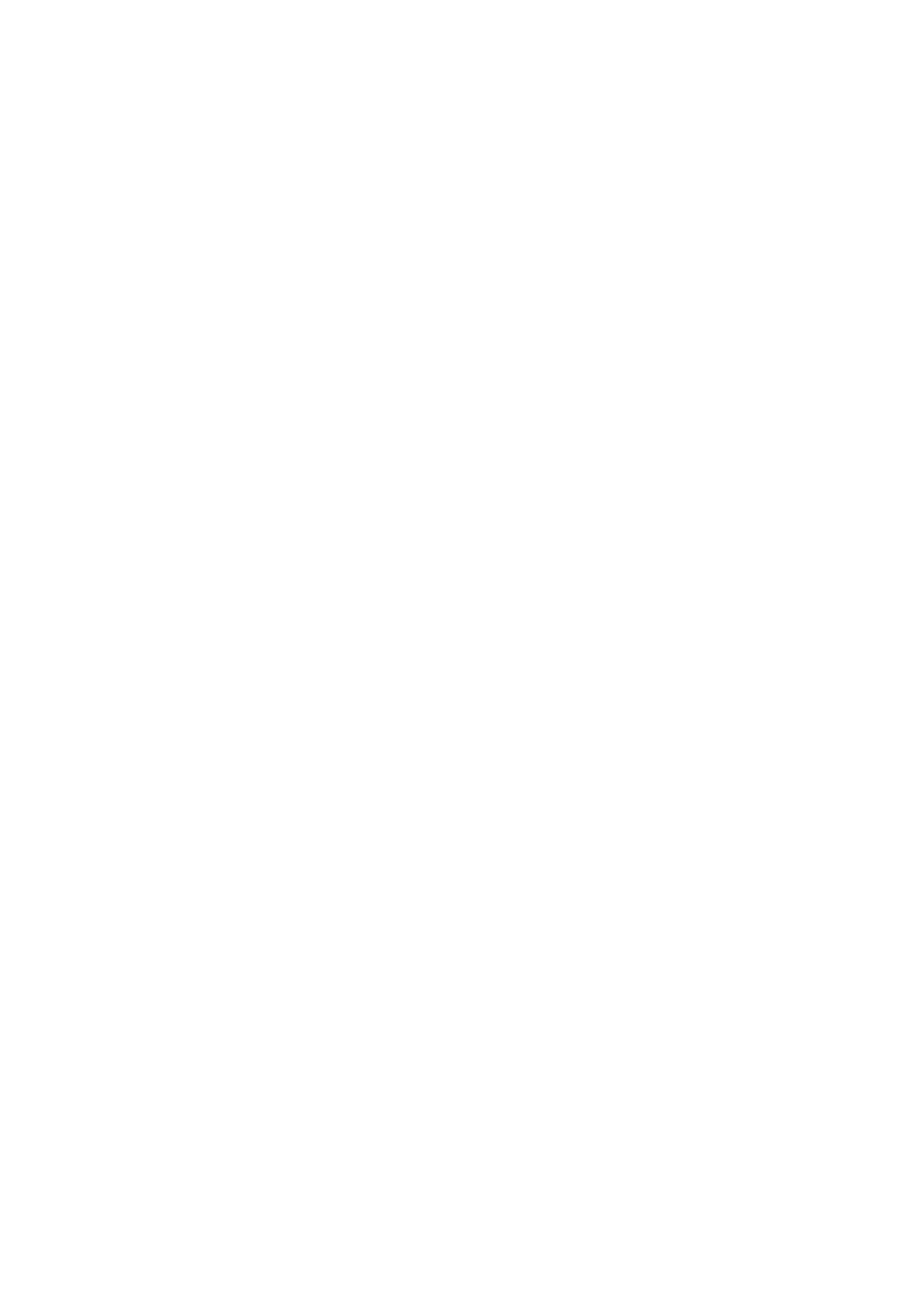
4.7 DETECTING INTERMITTENT ELECTRICAL FAULTS
DIAGNOSTIC PROCEDURE
This procedure can be used to detect intermittent terminal contact or a broken wire with an intermittent connection
inside its insulation.
Some digital multimeters, such as Tool No. 3588, have the ability to monitor current, resistance or voltage while
recording the minimum (MIN) and maximum (MAX) values measured.
When diagnosing circuits that have voltage applied, use the voltage setting to monitor a connector or part of a
circuit which may have an intermittent connection, but at the time is operating normally. Using Tool No. 3588:
1. Set the digital multimeter to read voltage. Since the MIN MAX mode does not use auto ranging, manually select
the voltage range necessary before proceeding.
2. Connect the meter to both sides of a suspect connector (still connected) or from one end of a suspect circuit to
the other. This will continuously monitor the terminal contacts or length of wire being checked.
3. Press the MIN MAX button. The meter should read 100 ms RECORD (100 millisecond record) and emit a 0.25
second beep. The meter is now ready to record and will generate an audible tone for any change in voltage. At
this point, press the PEAK MIN MAX button, which will record any voltage variations that occur for at least 1
millisecond.
4. Simulate the condition that may be causing an intermittent connection, either by wiggling connections or wiring,
test driving or performing other operations. If an open or resistance is created, a voltage drop will occur and the
meter will emit a tone for as long as the open or resistance exists. Any change in voltage will cause the meter to
emit a tone for no less than 0.25 second.
Use the MIN and MAX values when the meter is out of sight or sound range, in noisy areas or for test driving when
it may not be possible to monitor the meter.
To check the MIN and MAX recorded voltages, press MIN MAX button once for MAX and twice for MIN. A variation
between MIN and MAX recorded voltages (unless nearly 0 volts) suggests an intermittent open or resistance exists
and should be repaired as necessary. Refer to 5. WIRING REPAIR PROCEDURES in this Section for repair
procedures.
NOTE:The 100 ms RECORD mode is NOT the amount of time allowed to perform a specific procedure. It is the
amount of time used to record each snapshot of information used for calculating AVG when in the MIN MAX mode.
CHECKING TERMINAL CONTACT
Before replacing a suspect faulty component, it is important to check terminal contact between a connector and the
component, or between in-line mating connectors.
Frequently, a diagnostic chart leads to a step that reads for example ‘Check for poor connection’. Mating terminals
must be inspected to ensure good terminal contact. A poor connection between the male and female terminals at a
connector may be the result of contamination or deformation.
Contamination is caused by the connector bodies being improperly connected, a missing or damaged connector
seal, or damage to the connector itself, exposing the terminals to moisture and dirt. Contamination, usually in the
engine compartment or underbody connectors, leads to terminal corrosion, causing an open circuit or intermittently
open circuit.
Deformation is caused by probing the mating side of a connector terminal without the proper adaptor, improperly
joining the connector bodies or repeatedly separating and reconnecting the connector bodies together. Deformation,
usually to the female terminal contact tang, can result in poor terminal contact, causing an open or intermittently
open circuit.
To check terminal contact:
1. Separate the connector bodies or the component connector.
2. Inspect the connector bodies or component for contamination. Contamination will result in a white or green
build-up within the connector body or between the terminals, causing high resistance, intermittent contact, or an
open circuit. An engine compartment or underbody connector that shows signs of contamination should be
replaced if it is serviced (refer to VY Parts information for connectors that are serviced) or the relevant wiring
harness should be replaced.
3. Using an equivalent male terminal, check the retention force of the female terminal in question by inserting and
removing the male terminal to the female terminal in the connector body. Good terminal contact will require a
certain amount of force to separate the terminals.
4. Using a known good condition equivalent female terminal, compare the retention force of this terminal to the
female terminal in question by inserting and removing the male terminal. If the retention force is significantly
different between the two female terminals, replace the female terminal in question.
If a visual (physical) check does not reveal the cause of the problem, the vehicle may be able to be driven with a
digital multimeter connected to the suspected circuit. An abnormal voltage reading when the problem occurs
indicates the problem may be in that circuit.