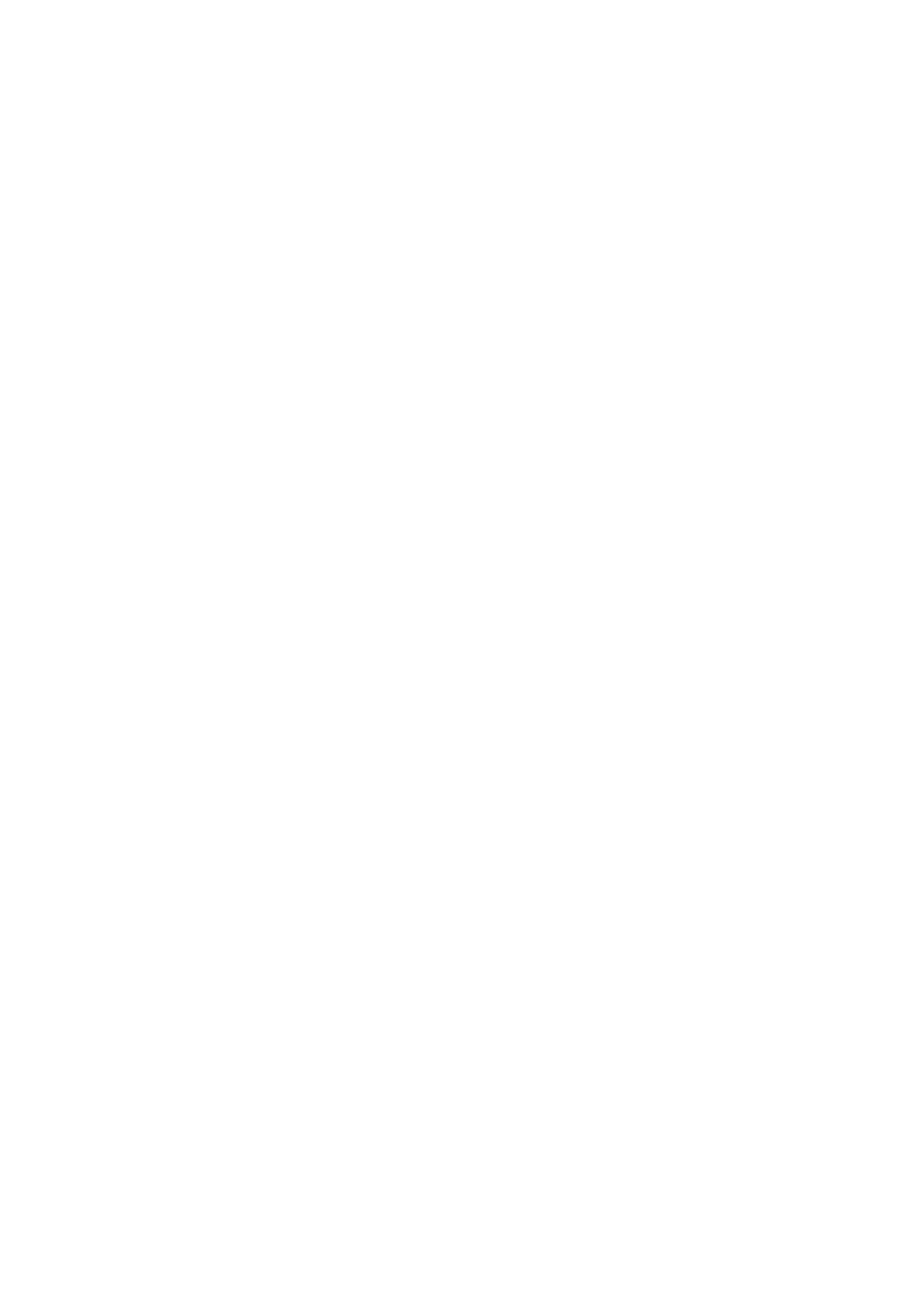
Housing............................................................ Semi-sealed, zinc coated steel with drain hole
Direction of rotation.......................................... Anti-clockwise (viewed from fan motor side)
Rotational speed.............................................. 2350 ± 150 RPM*
Power............................................................... 120 Watts (nominal)*
Current – constant ........................................... 20 – 22 Amps *
HIGH POWER COOLING FAN SYSTEM – V6
Engine Cooling Fan 1 (LHS)
Fan
Design.............................................................. Symmetric, curved blades with outer ring
Material ............................................................ Polyamide, with zinc coated metal hub insert
Number of blades............................................. 8
Diameter of blades .......................................... 365 mm
Diameter of outer ring...................................... 384 mm
Fan motor
Manufacturer.................................................... Gate
Model ............................................................... MP8125
Type................................................................. Dual speed, 4 brush and 4 permanent magnets
Housing............................................................ Semi-sealed, zinc coated steel with drain hole
Direction of rotation.......................................... Anti-clockwise (viewed from fan motor side)
Rotational speed – Stage 1.............................. 2250 ± 150 RPM*
Rotational speed – Stage 2.............................. 2500 ± 150 RPM*
Power............................................................... 220 Watts (nominal)*
Engine Cooling Fan 2 (RHS)
Fan
Design.............................................................. Symmetric, curved blades, with outer ring
Material ............................................................ Polyamide, with zinc coated metal hub insert
Number of blades............................................. 8
Diameter of blades .......................................... 263 mm
Diameter of outer ring...................................... 280 mm
Fan motor
Manufacturer.................................................... Gate
Model ............................................................... MP8120
Type................................................................. Dual speed, 4 brush and 4 permanent magnets
Housing............................................................ Semi-sealed, zinc coated steel with drain hole
Direction of rotation.......................................... Anti-clockwise (viewed from fan motor side)
Rotational speed – Stage 1.............................. 2500 ± 150 RPM*
Rotational speed – Stage 2.............................. 2800 ± 150 RPM*
Power............................................................... 180 Watts (nominal)*
Engine Cooling Fan Motors – Constant Current
Stage 1.................................................................... 25 – 27.5 Amps*
Stage 2.................................................................... 31 – 34 Amps*
COOLING FAN SYSTEM – GEN III V8
Engine Cooling Fan 1 (LHS)
Fan
Design.............................................................. Asymmetric, curved blades, with outer ring
Material ............................................................ Polyamide, with zinc coated metal hub insert
Number of blades............................................. 5
Diameter of blades .......................................... 275 mm
Diameter of outer ring...................................... 298 mm
Fan motor
Manufacturer.................................................... Gate
Model ............................................................... MP8120
Type................................................................. Dual speed, 4 brush and 4 permanent magnets
Housing............................................................ Semi-sealed, zinc coated steel with drain hole
Direction of rotation.......................................... Anti-clockwise (viewed from fan motor side)