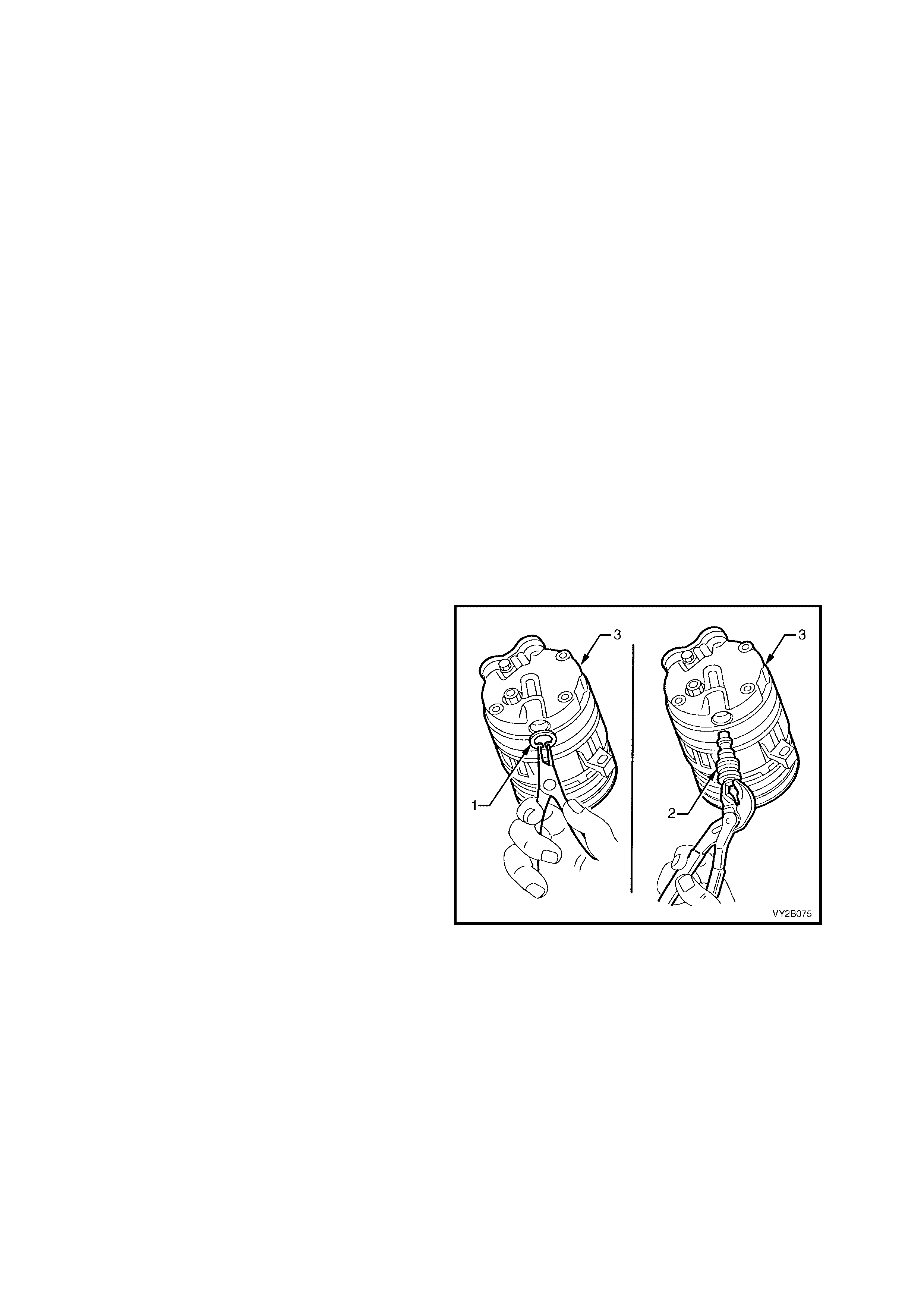
16. M INOR A/C COMPRESSOR REPAI R PROCEDURES
Illustrations used in the following procedures show the compressor removed from the vehicle for easier viewing.
When servicing the compressor, remove only the parts that preliminary diagnosis shows are in need of service.
Removal and installation of external parts of the compressor and disassembly/assembly of internal parts must be
performed on a clean workbench. The work area, tools and parts must be clean at all times.
NOTE: The only components that can be serviced are:
• Control Valve
• Port Sealing Washers
• Clutch Drive Plate and Hub Assembly
IMPORTANT: The total quantity of lubricating oil in the air conditioning system must be maintained. If a
compressor, evaporator, condenser, filter drier receiver, hose or pipe is to be replaced, a specified quantity of
lubricating oil must be added to the system to compensate for oil removed with the original component. Refer to
Section 2C, 2.4 LUBRICATING OIL COMPENSATION.
16.1 A/C COMPRESSOR CONTROL VALVE
LT Section – 08-200
REMOVE
1. Discharge the A/C system. Refer to Section 2C, 2. DISCHARGING SYSTEM – REFRIGERANT
RECOVERY.
2. Rais e fr ont of vehic le and support on saf ety stands. Refer to Section 0A, GENERAL INFORMAT ION for the
location of jacking and support points.
3. On GEN III V8 models remove the four bolts securing the under-tray to the crossmember and remove tray
from vehicle. Refer to Section 6B-3, 2.12 OIL PAN UNDER-TRAY.
4. From beneath the vehicle remove the lower air baffle / shute as required. Refer to
Section 6B-3, 2.13 AIR BAFFLES.
5. F rom beneath the vehicle r em ove the circ lip (1)
securing the control valve (2) to the
compressor (3).
6. Using a pair of s uitable cir c lip pliers r emove the
control valve from the compressor by pulling
downwards. Quickly insert the replacement
control valve (this will avoid any minor oil loss).
REINSTALL
1. Lubricate the control valve O-rings and
carefully push the control valve into the
compressor.
NOTE: V6 and GEN III V8 control valves have
different control settings. Ensure that the correct
control valve is installed.
2. Inspect the control valve retaining circlip. If it is
undamaged, reuse it to secure the control
valve. If it is not serviceable, replace it with a
new circlip. Ensure that the circlip is fully
seated in the circlip groove.
3. If A/C lubricating oil has been lost during
control valve removal procedure, add new
lubricating oil as required, through the suction
port of the A/C compressor. Refer to
Section 2C, 2.4 LUBRICATING OIL
COMPENSATION.
4. Install the lower air baffle / shute and under-tray
where fitted.
5. Evacuate and charge the A/C system with
775 – 825 g of R134a refrigerant, Refer to
Section 2C, 2. DISCHARGING SYSTEM –
REFRIGERANT RECOVERY.
Figure 2B-152