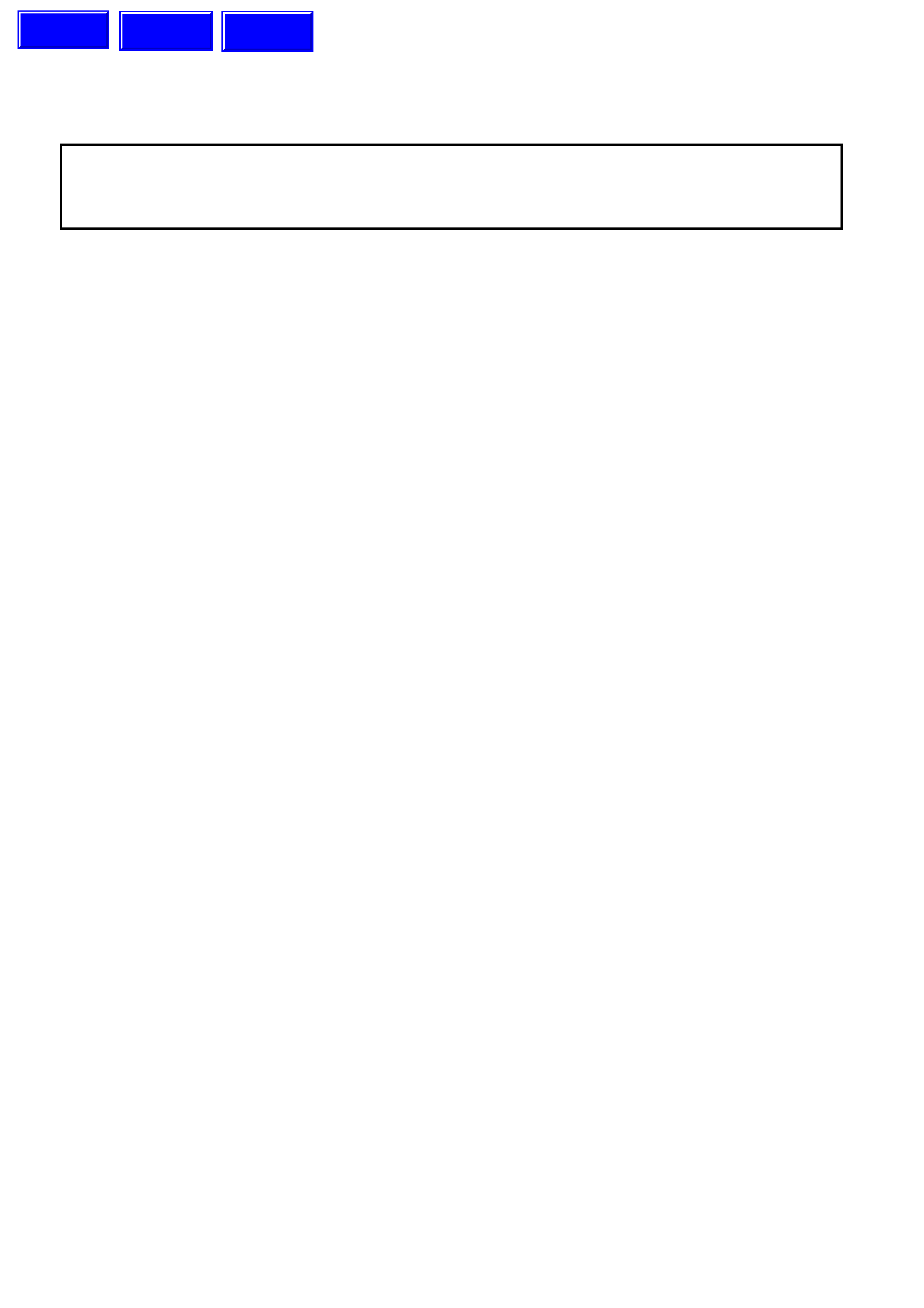
SECTION 2F HVAC OCCUPANT CLIMATE CONTROL
(AUTO A/C) – DIAGNOSTICS
IMPORTANT
Before performing any Service Operation or other procedure described in this Section, refer to
Section 00, CAUTIONS AND NOTES for correct workshop practices with regard to safety and/or
property damage.
CONTENTS
1. DIAGNOSTICS
1.1 TECH 2 DIAGNOSTICS
1.2 TECH 2 TEST MODES AND DISPLAYS FOR OCC
DIAGNOSIS
2. DIAGNOSTIC CHARTS
CHART A – DIAGNOSTIC CIRCUIT CHECK
CHART B – OCC SYSTEM DOES NOT POWER
UP
DTC 13 – AMBIENT TEMPERATURE SENSOR
VOLTAGE TOO HIGH
DTC 14 – AMBIENT TEMPERATURE SENSOR
VOLTAGE TOO LOW
DTC 15 – IN-CAR TEMPERATURE SENSOR
VOLTAGE TOO HIGH
DTC 16 – IN-CAR TEMPERATURE SENSOR
VOLTAGE TOO LOW
DTC 17 – EVAPORATIVE TEMPERATURE
SENSOR VOLTAGE TOO HIGH (LHD)
DTC 17 – EVAPORATIVE TEMPERATURE
SENSOR VOLTAGE TOO HIGH (RHD)
DTC 18 – EVAPORATIVE TEMPERATURE
SENSOR VOLTAGE TOO LOW (LHD)
DTC 18 – EVAPORATIVE TEMPERATURE
SENSOR VOLTAGE TOO LOW (RHD)
DTC 19 – SUN LOAD SENSOR ERROR
DTC 35 – NO SERIAL DATA FROM PCM
DTC 36 – NO SERIAL DATA FROM BCM
DTC 37 – ROM CHECKSUM ERROR
DTC 38 – EEPROM CHECKSUM ERROR
DTC 39 – RAM ERROR
DTC 40 – AIR MIX DOOR MOTOR DRIVER
ERROR (LHD)
DTC 40 – AIR MIX DOOR MOTOR DRIVER
ERROR (RHD DRIVERS SIDE MOTOR)
DTC 40 – AIR MIX DOOR MOTOR DRIVER
ERROR (RHD PASSENGERS SIDE MOTOR)
DTC 41 – SOLENOID DRIVER ERROR – LHD
DTC 41 – SOLENOID DRIVER ERROR – RHD
DTC 43 – DRIVER’S AIR MIX DOOR MOTOR
FEEDBACK CIRCUIT VOLTAGE TOO LOW
(LHD)
DTC 43 – DRIVERS AIR MIX DOOR MOTOR
FEEDBACK CIRCUIT VOLTAGE TOO LOW
(RHD)
DTC 44 – DRIVERS AIR MIX DOOR MOTOR
FEEDBACK CIRCUIT VOLTAGE TOO HIGH
(LHD)
DTC 44 – DRIVERS AIR MIX DOOR MOTOR
FEEDBACK CIRCUIT VOLTAGE TOO HIGH
(RHD)
DTC 45 – PASSENGERS AIR MIX DOOR
MOTOR FEEDBACK CIRCUIT VOLTAGE TOO
LOW
DTC 46 – PASSENGERS AIR MIX DOOR
MOTOR FEEDBACK CIRCUIT ZOLTAGE TOO
HIGH
DTC 47 – DRIVER AIR MIX MIN. CALIBRATION
ERROR (LHD)
DTC 47 – DRIVER AIR MIX MIN. CALIBRATION
ERROR (RHD)
DTC 48 – DRIVER AIR MIX MAX. CALIBRATION
ERROR (LHD)
DTC 48 – DRIVER AIR MIX MAX. CALIBRATION
ERROR (RHD)
DTC 49 – PASS AIR MIX MIN. CALIBRATION
ERROR
DTC 50 – PASS AIR MIX MAX. CALIBRATION
ERROR
3. ELECTRICAL COMPONENT TESTS
3.1 IN CAR TEMPERATURE SENSOR
3.2 EVAPORATIVE TEMPERATURE SENSOR TEST
LEFT-HAND DRIVE
RIGHT-HAND DRIVE
3.3 AMBIENT TEMPERATURE SENSOR
3.4 OCC BLOWER MOTOR RESISTOR
LEFT-HAND DRIVE
RIGHT-HAND DRIVE
3.5 VACUUM SOLENOID PACK
LEFT-HAND DRIVE
RIGHT-HAND DRIVE
3.6 WATER VALVE VACUUM SWITCH VALVE
4. VACUUM RETENTION TESTS
VACUUM LOSS DEFAULT SETTINGS
4.1 VACUUM SOLENOID PACK
4.2 VACUUM ACTUATOR LINES
LEFT- HAND DRIVE
RIGHT- HAND DRIVE
4.3 VACUUM MANIFOLD LINE
LEFT-HAND DRIVE
RIGHT-HAND DRIVE
4.4 WATER VALVE VACUUM SWITCH
5. WIRING DIAGRAMS
CONNECTORS: OCC SYSTEM
CONNECTORS: OCC SYSTEM CONTINUED
CONNECTORS: OCC SYSTEM CONTINUED
WIRING DIAGRAM: OCC SYSTEM – V6 LHD
WIRING DIAGRAM: OCC SYSTEM – V6 RHD
WIRING DIAGRAM: OCC SYSTEM – GEN III V8
LHD
WIRING DIAGRAM: OCC SYSTEM – GEN III V8
RHD
6. SPECIAL TOOLS