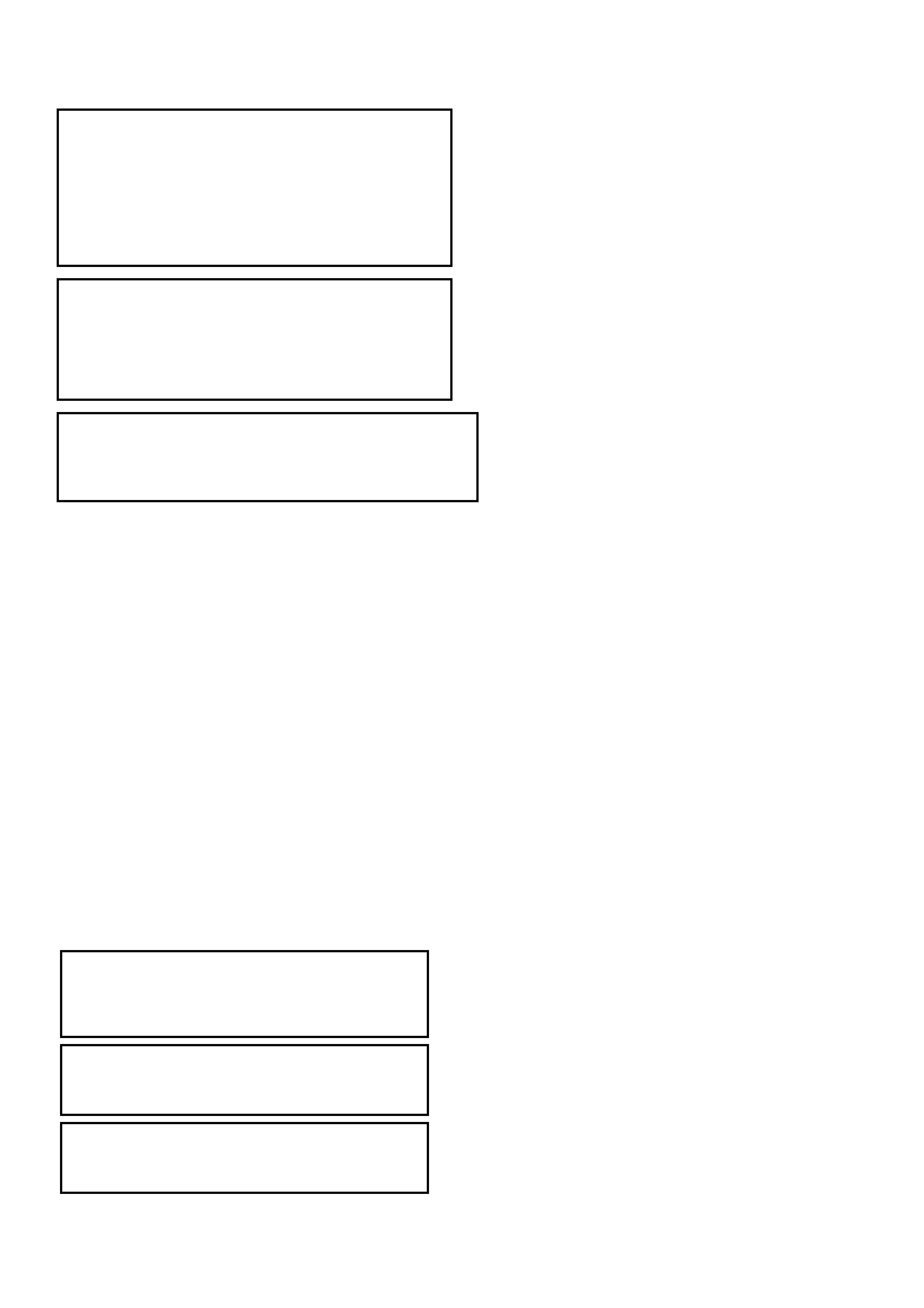
2.12 REAR WHEEL ALIGNMENT CHECKING
LT Section No. – 06-212
NOTE 1: The following fasteners have either micro
encapsulation or incorporate a mechanical thread lock
and should only be used once. If in doubt, replacement
is recommended when performing this operation:
♦ Rear suspension control arm to rear suspension
crossmember attaching nut.
♦ Rear suspension crossmember mounting brace to
underbody attaching bolts.
NOTE 2: The following fasteners MUST be replaced
when performing this operation:
!!!!$
$$
$ Rear suspension crossmember front mounting
bolt.
!!!!$
$$
$ Rear suspension crossmember mount to under
body attaching bolt.
NOTE 3: The following fasteners MUST be at curb height
before final tightening:
• Rear suspension control arm to rear suspension
crossmember attaching nut.
CAMBER AND TOE CHECK
The following conditions must be checked to ensure accurate measurement of rear wheel alignment.
1. Tread on rear tyres must be uniform and in a roadworthy condition.
2. Tyre pressures must be equal on both sides and to the correct pressure. Refer to the tyre placard on the vehicle
for correct tyre pressure s.
3. Wheel rim flange lateral run-out should be checked and to specification, refer to Section 10, WHEELS AND
TYRES.
4. T he vehic le must be at c urb height, ie. vehic le ready to drive with all fluids at r ec omm ended levels, fuel tank full,
without driver, passengers or luggage.
5. Stabilise vehicle springs by bouncing the rear of vehicle several times.
This step is very important, particularly if the vehicle was raised before checking. In that instance, the camber
angle m easur ed will be inc orrec t, because the r ear sus pension contr ol arm s will not have res um ed their norm a l
position.
NOTE 1: Camber is not adjustable. If there is any deviation from specification, the condition and alignment of the
crossmember, rear suspension control arms and bushing should be checked.
NOTE 2: W hen checking wheel toe, if one side has excessive toe-in and the opposite side has excessive toe-out,
this may be due to:
a. The rear suspension control arm attaching nuts being tightened when the vehicle was not at curb height.
b. The rear suspension crossmember not correctly aligned to the vehicle centreline.
To correct such a condition, check the rear suspension crossmember alignment, as detailed in
Section 1A2, BODY DIMENSIONS. Following the alignment procedure, tighten fastenings to the following torque
specifications.
( ! ) REAR SUSPENSION CROSSMEMBER
FRONT MOUNTING BOLT
TORQUE SPECIFICATION ................... 125 Nm, plus
30° – 40°
turn angle
( ! ) REAR SUSPENSION CROSSMEMBER
REAR MOUNT TO VEHICLE BODY
ATTACHING BOLT
TORQUE SPECIFICATION ................... 30 – 40Nm
( ! ) REAR SUSPENSION CONTROL
ARM TO REAR SUSPENSION
CROSSMEMBER ATTACHING NUT
TORQUE SPECIFICATION ................... 95 – 105Nm
Important: Alignment of the rear suspension crossmember requires the use of a special tool. Attempting to align
the rear suspension crossmember without it will not prove to be successful.