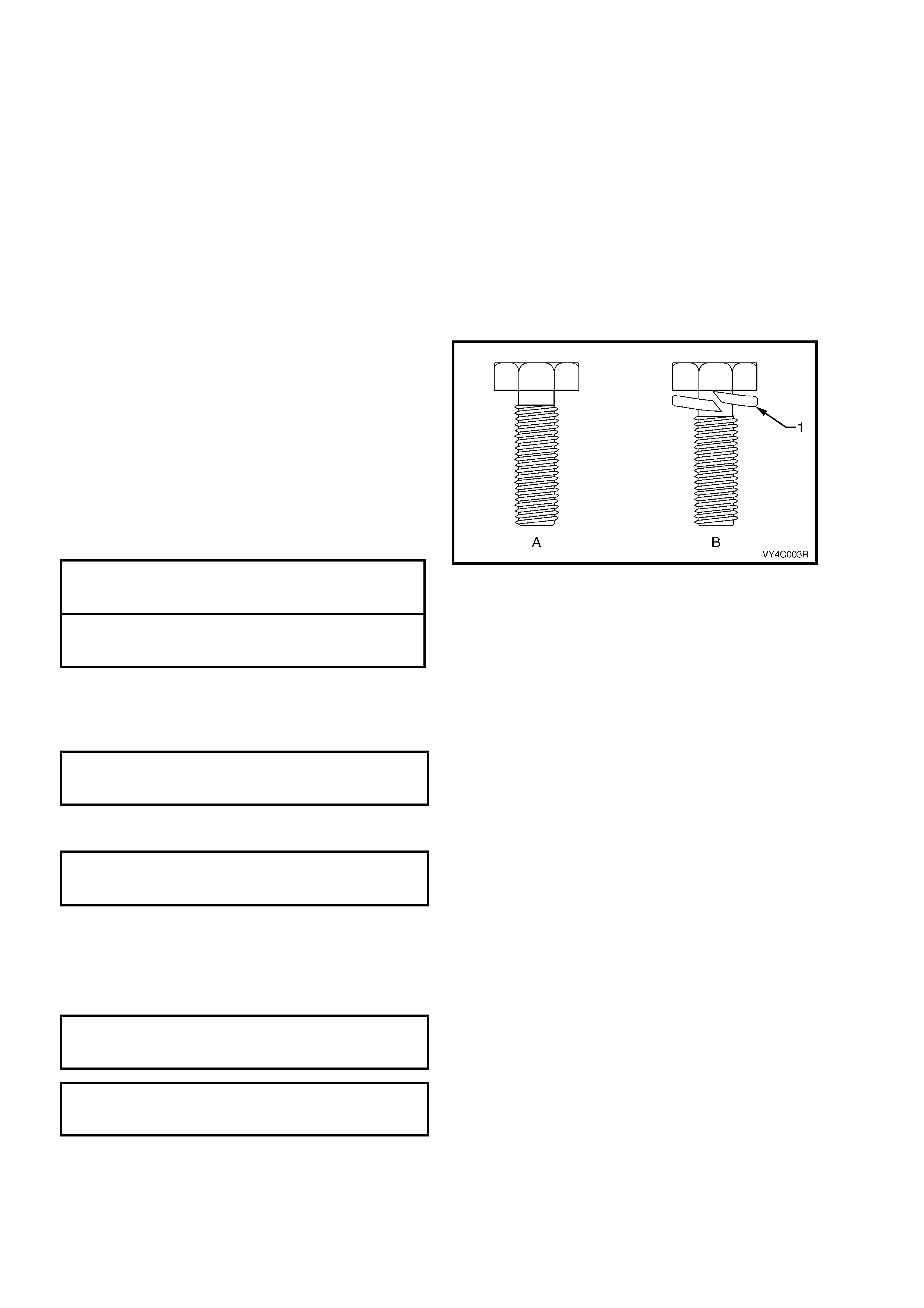
REINSTALL
Installation is the reverse of removal procedures noting the following:
1. Lubricate both the transmission output shaft (V6 engine and manual transmission) and the rear suspension
differential assembly pinion spigots with a molybdenum disulphide grease such as Molybond GA10 or Shell
ML10.
2. For those MY 2003 VY and V2 Series Models with a sliding front yoke, remove any foreign matter that may
have adhered to the f r ont univer sal j oint yoke and lubric ate with transmiss ion lubric ant. Inser t the yoke on to the
transmission mainshaft, indexing the splines.
3. Clean the threads of the centre bearing carrier to underbody reinforcement bolts and underbody weld nuts.
4. Install the front of the propeller shaft assembly first, supporting the centre and rear sections.
5. While still supporting the centre bearing area, slide the propeller shaft assembly forward to allow engagement of
the rear spigot, then slide rearward to fully engage.
6. Raise the centre bear ing assem bly and ins tall the bolts and washers to secure to the underbody reinforcem ent.
Tighten both bolts to the correct torque specification.
NOTE 1: There are two types of centre bearing
carrier to underbody reinforcement bolts. The first
type (A), is a micro encapsulated bolt and was used
at the start of production. T he sec ond type (B), was
introduced as a running change and is a zinc
coated bolt inc or porating a loc king washer (1) . The
mo st visible identification c an be determined by the
presence of, or lack of a locking washer.
NOTE 2: Micro encapsulated bolts should only be
re-used once. If in doubt, replacement is
recommended. If not replacing bolts, apply Loctite
242 or an equivalent to the cleaned threads.
( # ) TYPE 'A' CENTRE BEARING
CARRIER RETAINING BOLT
TORQUE SPECIFICATION 19 – 25 Nm
TYPE 'B' CENTRE BEARING
CARRIER RETAINING BOLT
TORQUE SPECIFICATION 20 – 35 Nm
Figure 4C-5
7. Before installing the attaching bolts and washers into the propeller shaft rear coupling and pinion flange, align
the marks made during removal of the pinion flange and rear coupling, refer to Figure 4C-3.
8. Provided no thread damage is evident, reinstall the original rear propeller shaft coupling to rear suspension
differential assembly pinion flange bolts, tightening to the correct torque specification.
PROPELLER SHAFT REAR
COUPLING TO PINION FLANGE
BOLT TORQUE SPECIFICATION 105 – 125 Nm
9. Vehicles with V6 Engine and Manual Transmission, install new rubber coupling to transmission output flange
retaining nuts before tightening to the correct torque specification.
( ! ) RUBBER COUPLING TO TRANSMISSION
OUTPUT SHAFT FLANGE RETAINING
NUT TORQUE SPECIFICATION 50 – 85 Nm
10. Install the exhaust system noting the following;
For vehicles fitted with a V6 engine and manual transmission:
a. Check that the catalytic converter to intermediate exhaust pipe bolts, springs and sealing ring are all in a
serviceable condition prior to installation.
b. Tighten all exhaust fasteners to the specified torque.
EXHAUST PIPE FLANGE TO
EXHAUST MANIFOLD NUT
TORQUE SPECIFICATION 18 – 35 Nm
INTERMEDIATE EXHAUST PIPE
TO CATALYTI C CONVERTER
BOLT TORQUE SPECIFICATION 40 – 50 Nm
c. Ensure that both wiring harnesses to the oxygen sensors are properly connected.