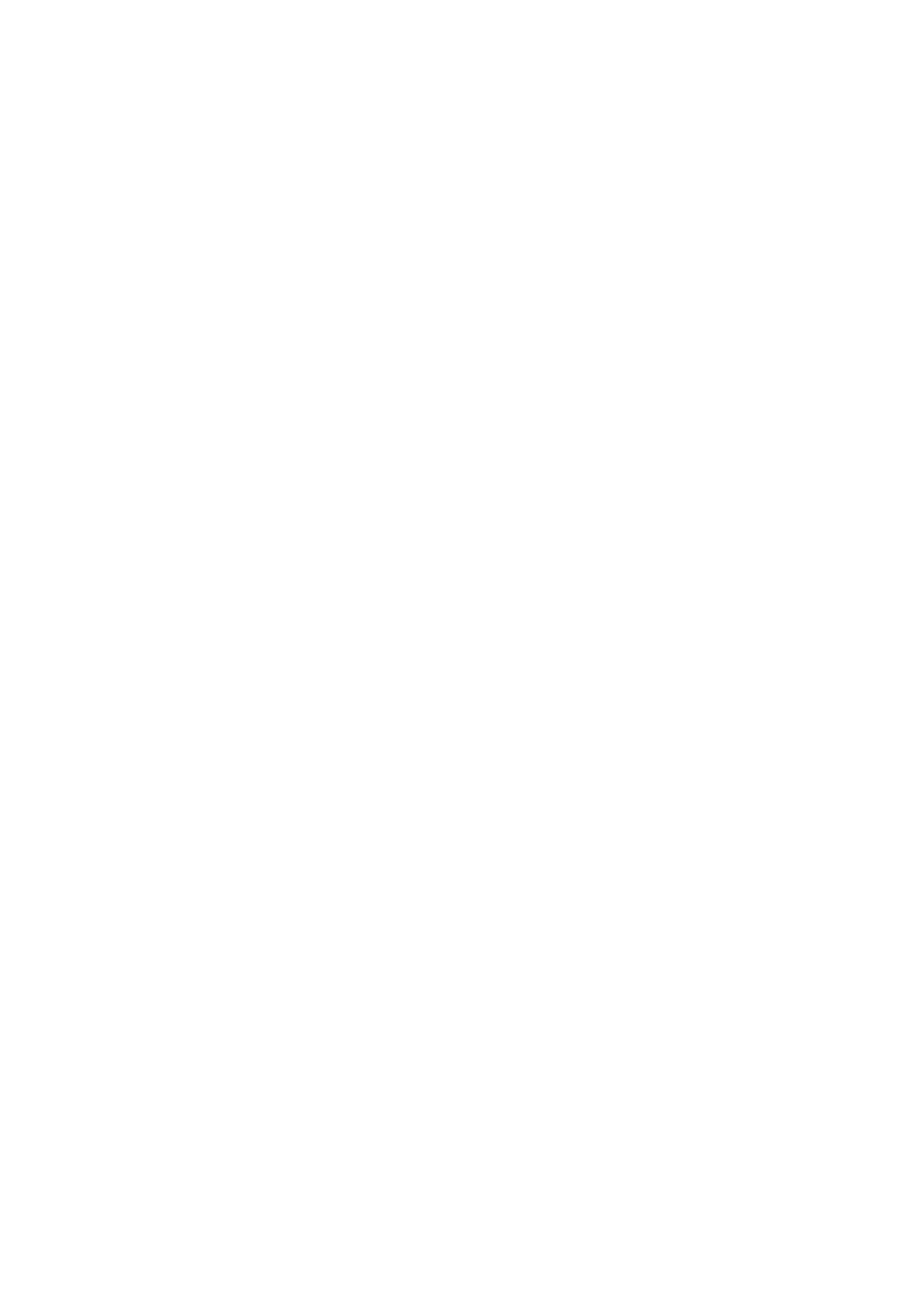
1. GENERAL INFORMATION
1.1 GENER AL DESCRIPTION
Some illustrations in this Section may show components that are not fitted to all vehicles. Where differences in
service procedures apply, then relevant information relating to those differences are made.
Except f or thos e v eh icles e qui ppe d with A BS as s tand ar d equ ipment, the f r ont an d rear disc br ak es on M Y20 03 V Y
and V2 Series vehicles, are served by separate brake circuits by means of a tandem master cylinder, working
through a vacuum booster. T he dual brake circuit arrangement is designed to provide adequate braking, should a
fault occur in either circuit.
All MY200 3 VY and V2 Series vehicles are f itted with a Steppe d Tandem , Vacuum Suspended t ype brak e booster
and a 25.4 mm bore master cylinder, regardless of the brake system used. The brake booster is not able to be
serviced and must be replaced if proven to have become defective.
All MY2003 VY and V2 Series vehicle are fitted with ventilated discs at the front and solid discs at the rear. The
brake calipers are the sliding, reaction type, with twin pistons in the front calipers and single in the rear.
The front disc brake caliper is attached to the steering knuckle support by two bolts, as is the front wheel bearing
hub, using three bolts. The front dust shield is also attached to the steering knuckle support by three pop rivets.
The rear brake backing plate assembly is bolted to the trailing arm, as is the disc brake caliper. The machined inner
surface of the disc hub acts as the brake drum for the park brake.
The single shoe, Banksia park brake is a drum type with a manual adjustment incorporated into the design. The
park brake is operated by two separate cables at the rear, connected to an equaliser bracket. Park brake
application force is applied to this equaliser bracket, via a single cable, connected to the floor mounted, button
release, park brake lever. Adjustment of the parking brake cables is provided for, by a threaded end on the front,
single cable, at the park brake lever end.
For servici ng deta ils of the ABS Br aking System , ref er to Section 5B in this Service Information.
1.2 MASTER CYLINDER
DESCRIPTION
A ma ster cylinder with a 25 .4 mm (1”) diameter bore is used on all MY2003 V Y and V2 Ser ies vehicl es, regar dless
of the braking system fitted. The only differences being:
a. The m aster cylinder used with ABS has a sc rew in blank ing plug i nstalled into the lower of the two front brake
outlets in the master cylinder.
b. The master cylinder fitted to MY2003 VY Series Utility vehicles does not have a brake proportioning valve
incorpora t ed in to t he master cylinder but us es a s eparate, lo ad sensing pr o porti o nin g val ve , c ou ple d t o the rear
suspension. This ensures that the front to rear braking balance, relative to vehicle load, is maintained.
The master cylinder is a tandem, centre valve design, incorporating a fast fill valve that provides a reduced pedal
travel. T he m aster cylinder is m ounted to th e vacuum brak e booster whic h in turn, is m ounted to t he eng ine side of
the dash panel.
CONSTRUCTION
This tandem m aster cylinde r arr angement prov ides s e p arate hydraulic c irc u its f or the applic at io n of the brakes, in a
front to rear split arrangement.
Both of these circuits are fed by separate fluid feed and compensating ports, through a common fluid reservoir,
sealed by a diaphragm fitted inside the reservoir cover. This diaphragm provides an effective seal against any
atmospheric moisture coming into contact with the hygroscopic brake fluid. This provision maintains the brake
fluid's boiling point, for a maximum period of time.
The internal parts of the master cylinder comprise a primary piston with an L type seal and an O-ring seal, a
secondary valve which incorporates a centre valve, a caged spring and two L type seals, a return spring, a
secondary piston stop pin, and a fast fill valve.
In all vehicles except MY2003 VY Series Utility, a proportioning valve is located in a parallel bore in the same
casting of the master cylinder. This valve is used to maintain the front to rear hydraulic pressure balance. Should
one of the two separate systems fail, a separate piston and brake pressure differential warning switch is
incorporated into the design so that the vehicle operator can be warned of a system malfunction.
The MY20 03 VY Series Ut ilit y has a load s ensing pro portioning valve locat ed at the rear of the veh icle. A pr essure
diff erential spool va l ve replaces the propor tioni ng va l v e, n or mally locat ed in the s ec ond bor e of the master cylind er .
This spool valve can move back and forth to operate the brake pressure differential warning switch, should a
pressure loss occur in either the front or rear brake circuits.