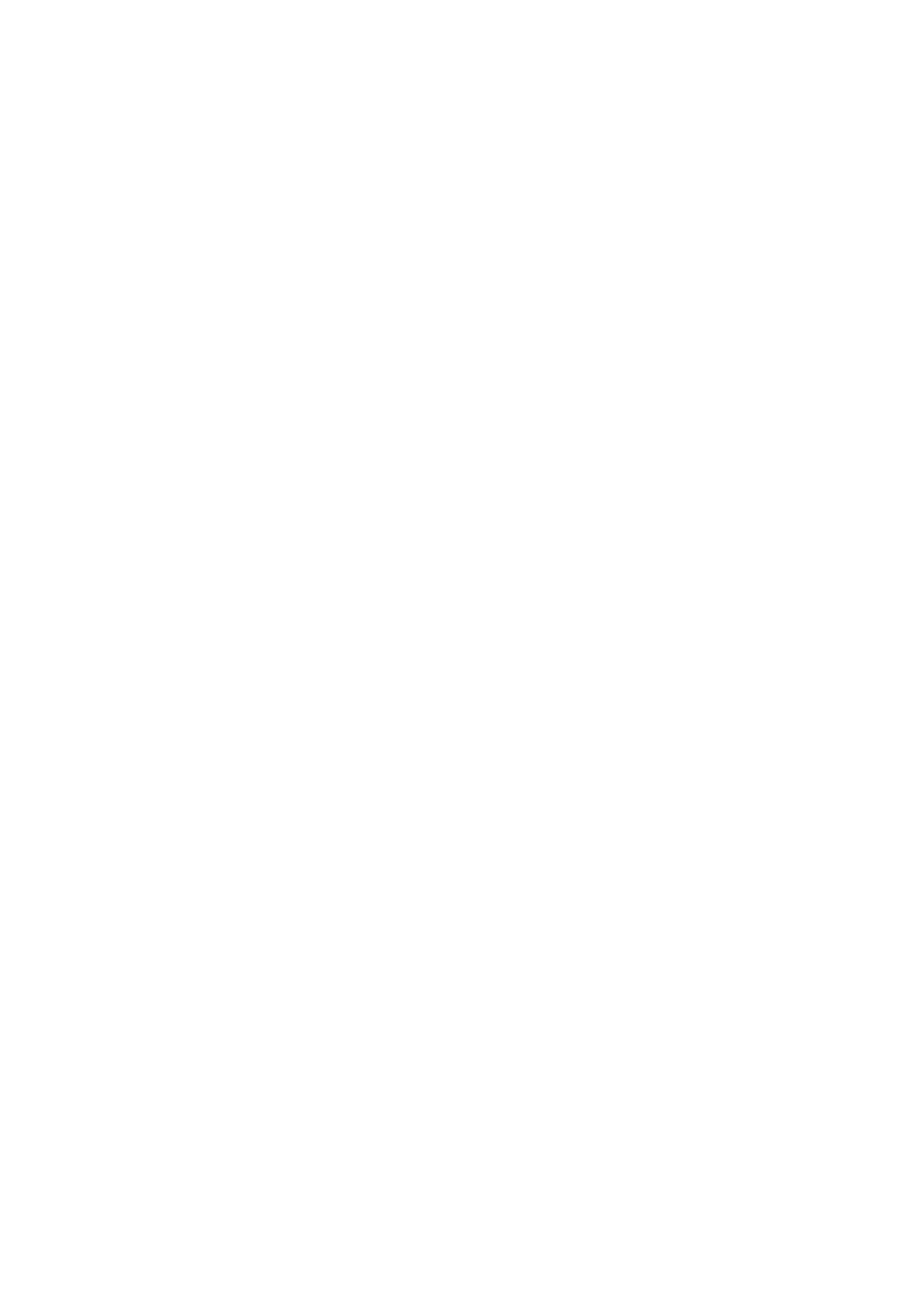
2.6 ABS/TCS PRINCIPLES OF OPERATION - EXCLUDING ABS
NON-ANTI-LOCK BRAKING / NON-TRACTION CONTROL
Under normal braking and driving conditions, the anti-lock braking system functions much like a conventional
braking system. Brake fluid pressure is provided by the brake master cylinder and the power booster.
For non-ant i-lock br aking, hydraul ic pressure is applied to the brak e caliper with out any interve ntion from the ABS.
At this t ime, the hydraulic modulator establishes an open two-wa y f luid pat h from the m aster cylinder to the brake
caliper. Non-anti-lock braking occurs when the wheel sensors do not detect wheel lock-up tendencies. However,
even though the ABS is passive during normal braking, the ABS/TCS module is constantly monitoring for rapid
acceleration (wheel slip) and deceleration (wheel lock) of any of the wheels and a signal from the brake switch
(brakes applied input).
ANTI-LOCK BR AKING
When the ABS senses any tendency for wheel lock-up, it enters the anti-lock mode. During anti-lock braking, the
ABS m odulates hydraulic pressur e in the brake circ uits to control wheel sli p to 10 - 20%. For anti-l ock brak ing, the
ABS control module controls current flow to the hydraulic modulator solenoid valves to control (by maintaining,
decreasing or increasing) hydraulic pressure in the brake circuits.
NOTE: The hydraulic modulator cannot increase brake circuit hydraulic pressure above the pressure supplied by
the brake master cylinder during anti-lock braking.
ELECTRONIC TRACTION CONTROL
W hen the ABS/TCS control module s enses spin fr om the dr ive wheels du e to too much engine tor que for the road
conditions, it enters the traction control mode. While the ABS/TCS module monitors both front and rear wheel
speeds through the wheel speed sensors, the action taken will change, depending on the engine fitted to the
vehicle.
V6 Engined Veh ic les
During acceleration, if the ABS/TCS module detects drive wheel slip at any time, it will request (on the Torque
Request circuit) the Powertrain Control Module (PCM) to bring engine torque into a specific range. This is
accomplished via two high speed Pulse Width Modulated (PWM) circuits between the ABS/TCS module and the
PCM. The PCM wi ll the n adj ust spar k firing and a ir/fuel r atio, alterin g boos t dut y c ycle ( Superc harged engin e onl y),
and shutting OFF up to five (5) injectors (if necessary), and report the modified torque value (on the Torque
Achieved circuit) back to the ABS/TCS module. Simultaneous with engine torque management, the ABS/TCS
module will activa te the ABS isolation valves, turn on the ABS pum p motor and supply brake pressure to the over
spinning wheel(s).
GEN III V8 Engined Ve hicl es
If at any time during acceleration, the ABS/TCS module detects drive wheel slip, it will request:
• The PCM, via the spark retard circuit, to retard the amount of spark advance.
• The throttl e r el axer c ontro l module to r e duce the engine thr ott le ope ni ng by a cer t ain perc ent age to bring en g ine
torque into a specific range.
The throttle relaxer control module accomplishes this by commanding the throttle relaxer to override the
accelerator pedal cable and physically reduce the throttle body butterfly opening by winding the throttle cable
back.
T his is achieved via two hi gh speed Pulse Width Mod ulated (PW M) circuits between the AB S/TCS m odule and
the throttl e r e laxer c on tr ol module. T he A BS/TCS c o n tr ol module s ends a mes s age to the thr ot tle r el axe r c o ntr ol
module on the requested throttle position (DKR) circuit. The throttle relaxer control module then reports the
modified throttle position opening back to the ABS/TCS control module via the actual throttle position (DKI)
circuit.
Simultaneously with eng ine s par k retard and throttl e p os ition i nter vent io n, th e A B S/TCS contr ol module will ac tiv ate
the ABS isolation valves, turn on the ABS pump motor and supply brake pressure to the over spinning wheel(s).
The isolation valves isolate the front brake hydraulic circuits from the master cylinder and rear brake hydraulic
circuits. Once the rear brake hydraulic circuits are isolated, pressure can be applied to the rear wheels without
aff ecting an y other brak e hydraul ic circuits . The AB S/T CS hydraulic module opens the priming valve, a llowing f luid
to be drawn from the master cylinder to the pum p motor, which is then activated, building pressure. The hydraulic
module, in let and outlet va lves begin c ycli ng and the switchi ng valve clos es, ensuring f luid is direct ed to the wheel
and not back into the master cylinder.
The inlet and outlet valve cycling assists in obtaining maximum road surface traction in the same manner as the
Anti-Lock Brake mode. The difference between Traction Control and Anti-Lock Brake mode is that brake fluid
pressure is increased to lesson wheel spin (Traction Control mode), rather then reduced to allow greater wheel spin
(Anti-Lock Brake mode).
If at any time during Traction Control mode, the brakes are manually applied, the brake switch signals the
ABS/TCS module to inhibit brake intervention and allow for manual braking. However, engine intervention (V6
engines) or, throttle reduction and spark retard intervention (GEN III V8), can still occur if necessary.