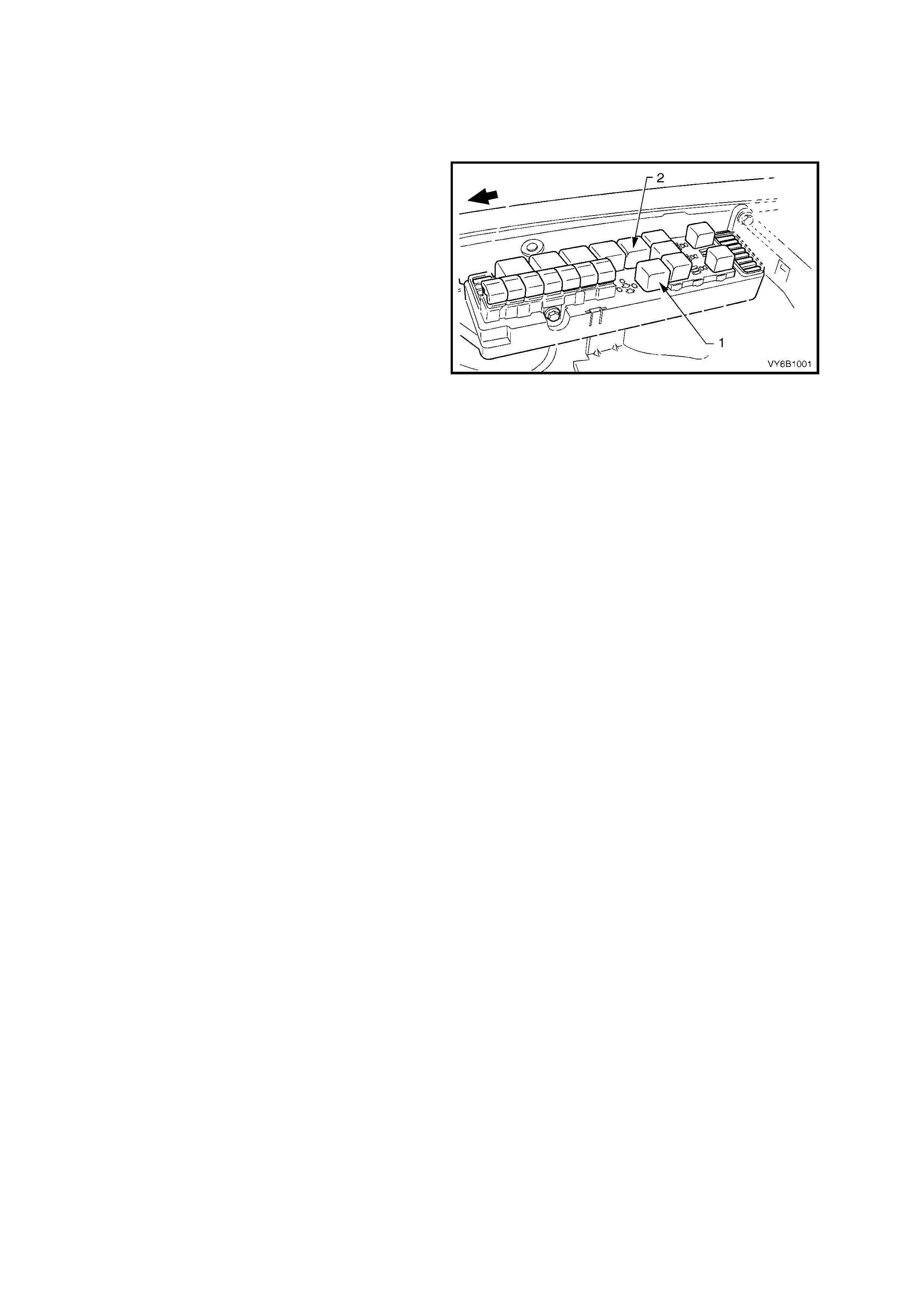
The fan motors are also connected electrically, as follows;
• The Low/Hi gh speed nega tive wir es from each motor go thr ough the rad iator fan c onnector s eparatel y and are
spliced together in the main wiring harness before reaching engine cooling fan relay 1.
• The High speed wires from each m otor are spliced together before the radiator fan connector and go through
the connector as one circuit, to engine cooling fan relay 2.
When the High/Low negative terminal from each
motor is connected to ground via engine cooling
fan relay 1, both cooling fans will operate at stage
1 (Large f an at 2, 00 0 ± 150 rpm, Small fan at 2,350
± 150 rpm). With engine cooling fan relay 1 still
activated, when the high speed negative terminal
from eac h motor is c onnected to gro und via eng ine
cooling fan relay 2, both fans operate at stage 2
(Large fan at 2,300 rpm ± 150 rpm, Small fan at
2,700 ± 150 rpm). .
Stage 1 cooling fan operation is enabled when the
engine cooling fan micro relay 1 (located in the
underhood electrical centre) is energised by the
Body Contr ol Mo du le (BCM ) , via a r equest f r om the
Powertrain Control Module (PCM).
The PCM will request stage 1 enable or disable,
via the serial data Normal Mode Message to the
BCM on circui t 800 (Red/Black wire).
Figure 6B1-4 – Underhood Fuse & Relay Centre
After the PCM reques ts a change in the state of the low sp eed rela y ( i.e. OFF to ON or ON to OFF), the BCM will
send a serial data response message back to the PCM confirming it received the message. Should a response
from the BCM fail to occur, a PCM DTC P1064, will set.
The PCM determines when to enable stage 1, based on inputs from the A/C request signal, Engine Coolant
Temperature (ECT) sensor and the Vehicle Speed Sensor (VSS).
There are also suppression capacitors incorporated into the fan motor, located on the brush holders. These
suppression capacitors help eliminate fan motor noise through the radio speakers. As these capacitors are not
serviced separately, should a problem occur with either capacitor, then the motor assembly must be replaced.
Stage One Fan Operation
1. The cooling fan relay 1 will be turned ON when:
• Air conditioning request indicated (YES) and the vehicle speed is less than 30 km/h or:
• Air conditioning pressure is greater than 1,500 kPa or:
• Coolant temperature is greater than 104° C or:
• An engine coolant temperature sensor failure is detected by the PCM, refer to
Section 6C1 POWERTRAIN MANAGEMENT – V6 ENGINE for additional information.
• When the ignition switch is turned from ON to OFF and the engine coolant temperature is above 117° C,
the BCM will continue to energise engine cooling fan micro relay 1 for approximately four minutes.
2. The PCM will requ es t the B CM to s witc h of f engine c o oli ng f an re lay 1 when the fo llo wing c ond it ions ha ve b e en
met:
• Air conditioning request not indicated (NO) and the coolant temperature is less than 99° C or:
• Air co nditioning r equest indic ated (YES) with pres sure less than 1,170 k Pa, vehicle sp eed greater t han 5 0
km/h and coolant temperature less than 99° C.
Stage Two Fan Operation
The PCM determines when to enable the engine cooling fan relay 2, based on inputs from the ECT sensor.
1. Engine cooling fan relay 2 will be turned ON if the engine cooling fan relay 1 has been energised for one
second and the following conditions have been met:
• If there is a BCM message response fault, setting a PCM DTC P1064 or:
• An engine coolant temperature sensor failure is detected by the PCM, refer to
Section 6C1 POWERTRAIN MANAGEMENT – V6 ENGINE for additional information or:
• Engine coolant temperature is above 108° C or:
• Air conditioning pressure is greater than 2,000 kPa.
2. If stage 2 has been enabled, the PCM will revert to stage 1 operation when:
• The engine coolant temperature is less than 103° C and:
• Air conditioning request is not indicated (NO) or:
• Air conditioning request is indicated (YES) and the pressure is less than 1,500 kPa.