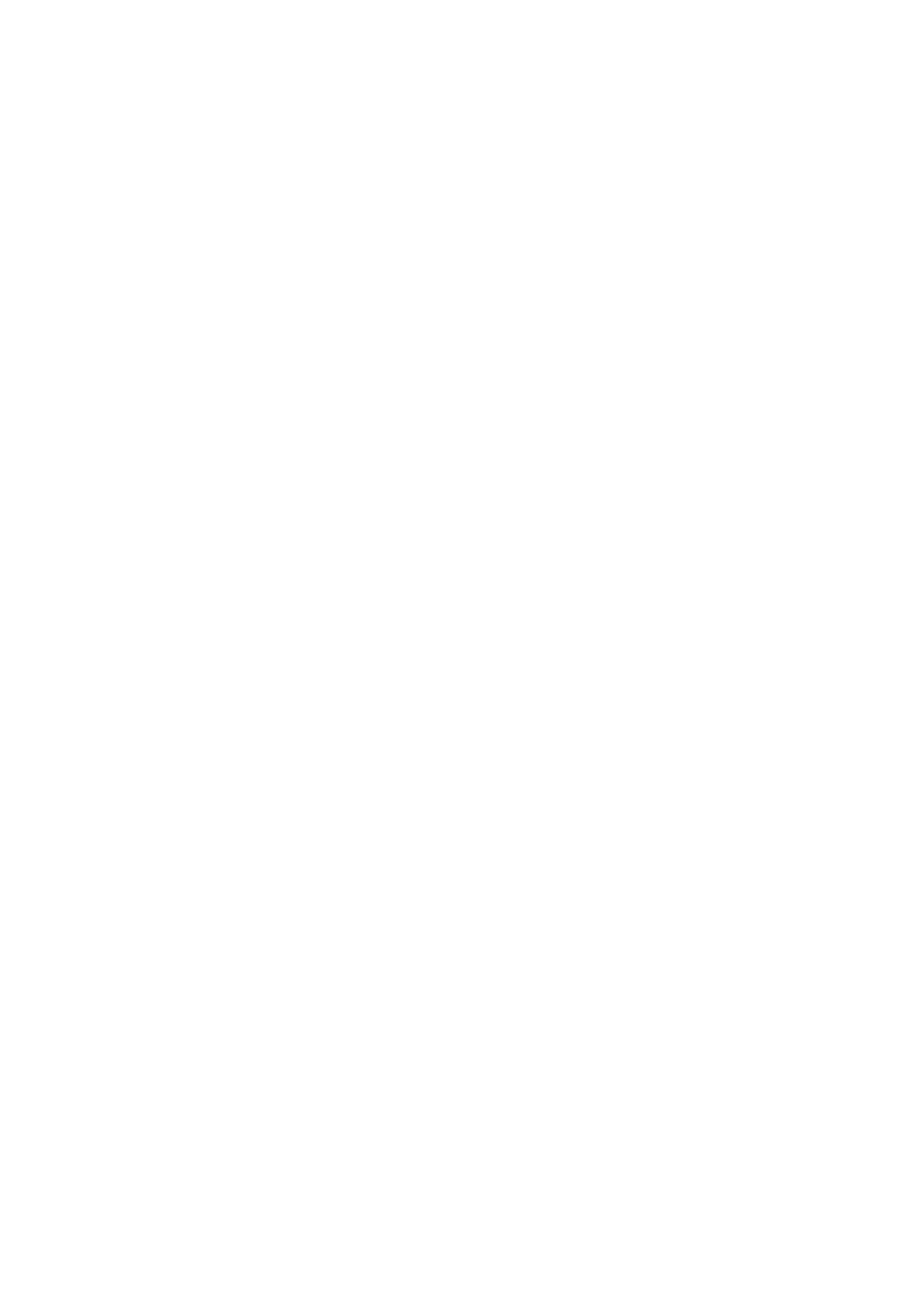
ADAPTIVE LEARNING
Adaptive learning is the ability of the PCM to determine and remember its most recent operating experience. The
PCM uses this rem embered inform ation to learn from experience and to make adjustm ents with respect to what it
learnt. If the engine were to develop a restricted fuel f ilter, the PCM will chan ge the fuel injector pulse widt h richer
to com pensate for this con dition and will rem em ber to k eep this fuel inj ector p ulse in m em ory until the r estri ction is
corrected. After the restriction has been f ixed, the PCM will eventually go back to the original preprogrammed fuel
injector pulse. Adaptive learning is an on-going process that continues throughout the life of the engine.
SHORT TERM FUEL TRIM
Short Term Fuel Trim (ST FT) represents short term corrections to t he fuel inject or pulse width calculations, based
on the oxygen sensor input signals to the PCM.
When the engine is started cold, in open loop, the PCM will control the fuel injection pulse width based upon
various sensor inputs such as RPM, ECT, MAF and TP sensor until the oxygen sensors become hot enough to
operate properly. During this open loop period, both Short Term Fuel Trim (STFT) and Long Term Fuel Trim (LTFT)
are disabled and will read 0% on a TECH 2 scan tool.
When the oxygen sensors have reached normal operating temperature, they will produce a varying voltage to the
PCM and provide a good indication of what has happened in the combustion chambers.
At this time the PCM will switch from open loop to closed loop and the STFT will start to constantly monitor the
oxygen sensor signals, so that the PCM can modify fuel injector pulse width with greater accuracy than in open
loop.
STFT monitors the oxygen sensor signals so that it can adjust the fuel injector pulse width to maintain an air/fuel
ratio of 14.7 to 1 f or maximum catalytic convert er efficiency. An ST FT value of 0% is equiva lent to an air/fuel ratio
of 14.7 to 1 and an average oxygen sensor signal voltage of 450 mV.
The normal position for STFT is 0%, any change from this value indicates the STFT is changing the fuel injector
pulse width. The amount of pulse width change depends upon how far the STFT value is from 0%. If the STFT
value is above 0%, the fuel injector pulse width is being increased, thus adding more fuel. If the STFT value is
below 0%, the fuel injector pulse width is being decreased, thus removing fuel. The normal operating range of
STFT is considered to be between -22% and +25% ; any value out of this range is usually caused by a malfunction.
If an engine has a restricted fuel filter, the low fuel pressure will result in less fuel being injected and allows more air
into the air charge than is needed to ignite the amount of fuel the fuel injector has delivered, therefore, a lean
air/fuel ratio exists in the combustion chamber. After combustion has taken place, the exhaust gases still contain
mor e ox ygen content th an nor mal and the oxygen sen sor s read this as lo w volta g e, s a y 200 mV. The ST FT detects
that the oxygen sensor signals are low and will increase the value to richen up the air/fuel m ixture. On a TECH 2
scan tool it will display STFT as a value above 0%. This STFT change will increase the injector pulse width allowing
the fuel injectors to stay open longer and inject more fuel.
If the additional fuel was injected and the oxygen sensor signal voltages are still low, the STFT will continue to
increase its value until the oxygen sensor signal voltages go above 450 mV. If the STFT continues to detect low
oxygen s ensor signal vo ltages it will c ontinue to tr y an d compensate f or the lean exhaus t condition u ntil it runs out
of its authority in the particular Long Term Fuel Trim (LTFT) cell it's operating in. At this point, the PCM will reset
STFT to 0% and go through this procedure again until it can control the system.
If af ter a specif ied amount of r esets have been tr ied and fa iled, the PC M knows t hat it cannot co ntrol for the failure
and the STFT will remain at its maximum value.
STFT values are based on the oxygen sensor signal voltage readings, therefore, STFT is used by the PCM to
make quick changes to the fuel injector pulse width over a short period of time.
LONG TERM FUEL TRIM
LTFT is used to adjus t for eng ine to engin e varia tion and t o adj ust f or engin e agein g. LT FT is a port ion of the PCM
memory used to a dj us t f uel del ivery acros s all operat in g c ond itions of th e engine. T he PCM monitor s the STFT and
will adj ust th e long ter m trend of the f uel inje ctor puls e widt h if the ST FT has bee n at a va lue f or a cer tain period of
time. LTFT is used to change the long term fuel injector pulse width and is only operational when the fuel control
system is in Closed Loop. A normal LTFT value is 0% and should follow the STFT value.
If an eng ine has a r estricte d fuel filt er, the lo w fuel pr essur e will resul t in less f uel being injected an d will c ause the
STFT value to go higher than 0%, say 2%. If this STFT value change does not compensate for the restricted fuel
filter, the PCM will continue to increase the STFT value. The STFT may climb as high as its maximum calibrated
value if there is a severe restriction. The PCM will continue to monitor STFT as it climbs, but it will not make any
changes to the LTFT for a specific period of time. After a specific period of time has elapsed and the STFT value
has rem ained ab ove sa y +8%, the LTFT wil l move up to sa y 4% and wait ag ain to de tect if the STF T has dr opped
back down to 0%. If not, the STFT will gradually move toward its maximum calibrated value limit until it gains
control of the fuel injection system. If STFT and LTFT are both set at their maximum value limit, the fuel control
system is out of the limits of control and will set either a Diagnostic Trouble Code (DTC) P0131, or DTC P0151
(lean exha ust) or DT C P0132, or DTC P01 52 (rich exhaust) and go into open loop operat ion. Under the co nditions
of power enrichment, (W ide Open Throttle, WOT), the PCM sets the STFT to 0% and freezes it there until power
enrichment is no longer in effect. This is done so that LTFT will not try to correct for the commanded richness of
power enrichment.