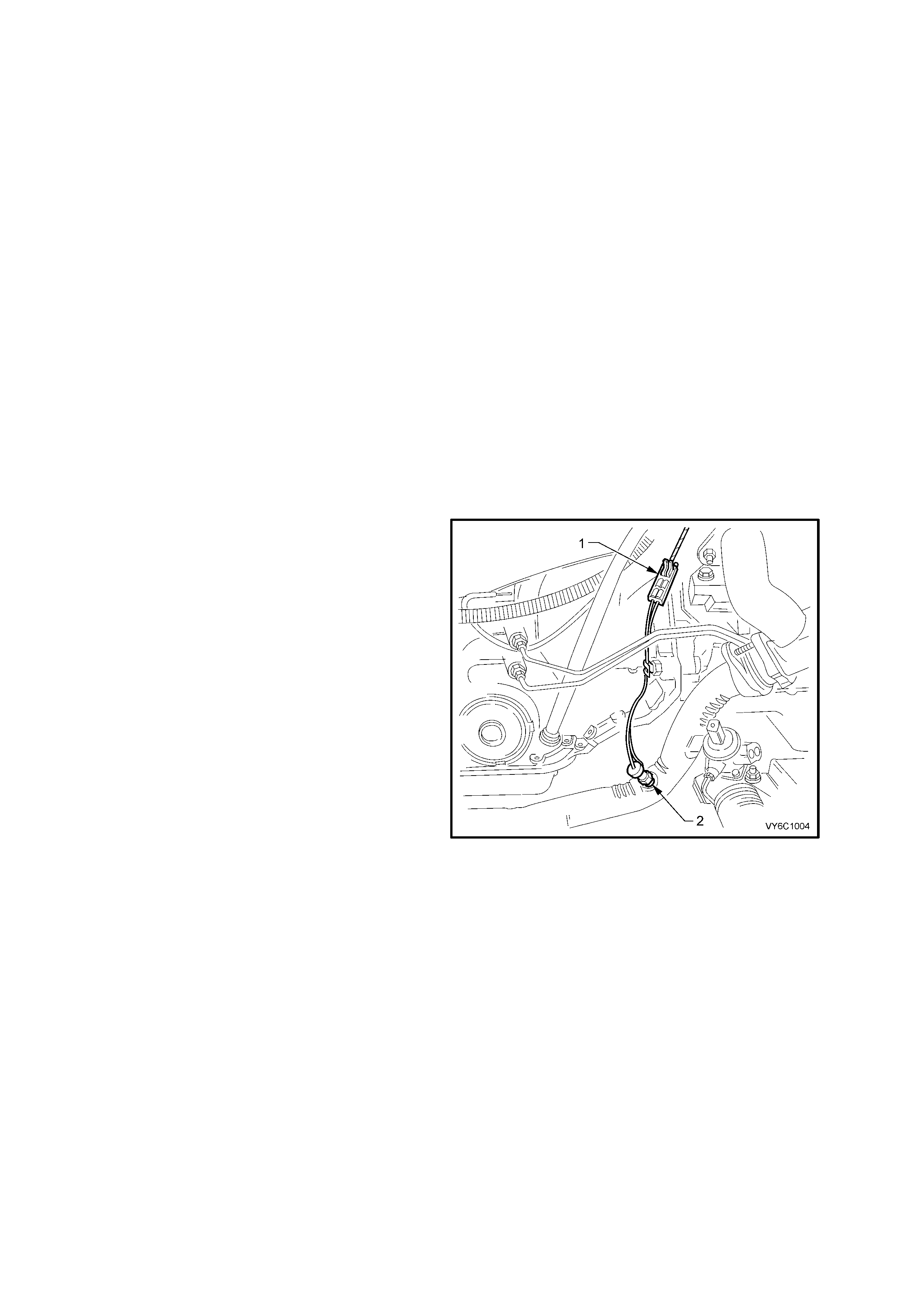
2.6 OXYGEN SENSOR
LT Section No. – 00-450
NOTE 1: The oxygen sensor uses a permanently attached pigtail and connector. This pigtail should not be
rem oved from the ox ygen sens or. Damage or r emova l of the pigta il or connector will affec t proper operation of the
oxygen sensor.
NOTE 2:Take care when handling the oxygen sensor. The in-line electrical connector and louvred end must be
kept free of grease, dirt or other contaminants. Avoid using any cleaning solvents. Do not drop or roughly handle
the oxygen sensor.
NOTE 3: The ox ygen sens or m ay be diff icult to remove when e ngine temper ature is below 60 ° Celsius. Excessive
force may damage threads in the exhaust pipe or sensor.
NOTE 4: Under no c ircumstances ar e the wiring harnes s connectors as sociated with the ox ygen sens or circuits to
be sealed in any way, by using grease or other substance. To do so, would result in an inadequate supply of
refer ence air to be able t o reach the atm ospheric reference c avity of eac h sensor, res ulting in a DTC to be s et. If a
flexible sealant is used (i.e. grease), then this would be drawn into the sensor cavity, poisoning the sensor,
resulting in a premature failure. Also, should connector damage be evident, then the sensor and lead must be
replace d, as soldering of the wiri ng wou ld also neg ate the ‘br eat hi ng ’ capa bility of the sensor wiri ng.
REMOVE
1. Disconnect battery ground lead.
IMPORTANT: Disconnection of the battery affects
certain vehicle electronic systems. Refer to
Section 00 CAUTIONS, 5. Battery
Disconnection Procedures before disconnecting
the battery.
2. Lift up retaining tang on oxygen sensor wiring
harness connector (1) and pull connector from
sensor pigtail connector.
For RH sensor, the connector (1) is located at
the rear of the RH cylinder head and is
accessed from the rear of the engine
compartment. The sensor pigtail leads are
further retained by a c lip attac hed to the torque
converter housing (automatic transmission).
For LH sensor (refer Figure 6C3-1-14), the
connector is located at the rear of the LH
cylinder head and is accessed from the rear of
the engine compartment.
3. Raise vehicle and support on safety stands.
Refer to Section 0A GENERAL
INFORMATION in the MY 2003 VY and V2
Series Service Information, for the location of
jacking and support points.
4. Carefully unscrew oxygen sensor (2) from
exhaust pipe referring to the ‘NOTES’ above.
NOTE: While the RHD vehicle arrangement is
shown, the LHD is similar.
Figure 6C1-3-13 – RH Sensor Location
REINST ALL
NOTE 1: A special anti-s eize c ompound is us ed o n
the oxygen sensor threads. The compound
consists of a liquid graphite and very small glass
beads. The graphite will burn away, but the glass
beads will remain, making the sensor easier to
remove.
NOTE 2: Genuine replacement sensors will
already have the compound applied to the threads.
If a sensor is removed from an engine, and, if for
any reason it is to be reinstalled, the threads
MUST have the specified anti-seize compound
applied before reinstallation.