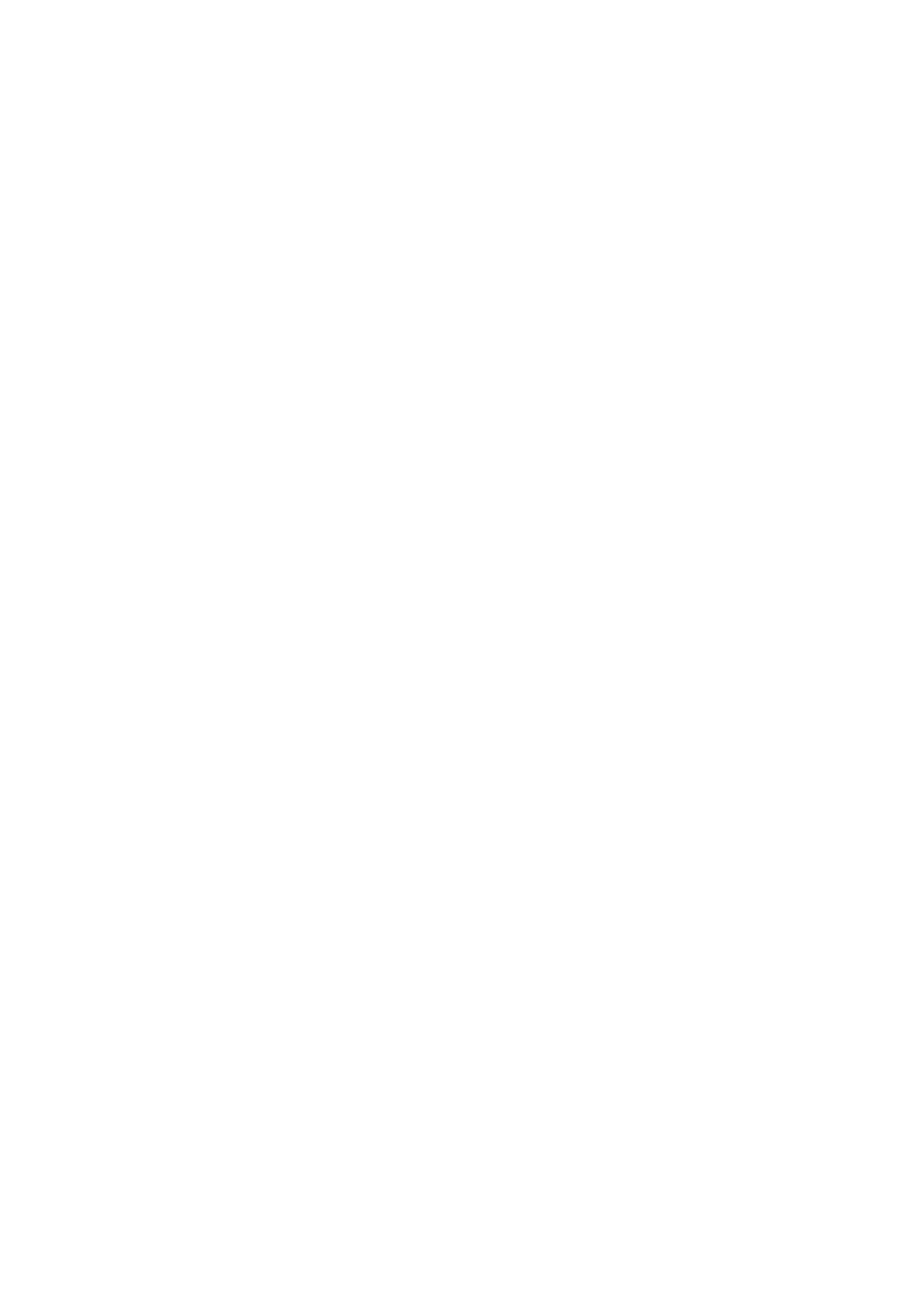
TECH 2: AUTOMATIC TRANSMISSION DATA DESCRIPTIONS
A list of explanations for each data message displayed on Tech 2 begins as follows. This information will assist in
track ing down emission or dr iveability problem s, since the displays can be viewed while the vehicle is being driven.
Refer to the "On-Board Diagnostic System Check" for additional information.
ENGINE SPEED – Range 0-9999 RPM – Displays the PCM's interpretation of actual engine speed, as received
from the reference input signal. Displays in increments of 1 RPM. Often useful to detect if extra reference pulses
are suspected. A sudden high RPM indication while at a steady throttle would indicate electrical interference in the
refer enc e input signal c irc uit. This inter f er ence is us ually caused by PCM wires too c lose to ignition s ec ondary wires
or an open reference ground circuit.
VEHICLE SPEED – Range 0-255 km/h – Displays the PCM's interpretation of vehicle speed as received from the
PCM. Also useful for checking speedometer accuracy.
TPS VOLTAGE – Range 0-5.00 Volts – This position shows the T hrottle Position sensor signal input to the PCM.
Values read will be in voltage and will interpret the throttle opening to the PCM. T he voltage should between 0.25 -
1.25 volts with the throttle closed and go up to approximately 4.5 volts at Wide Open Throttle (WOT).
THROTTLE ANGLE – Range 0-100% – This display is the PCM's interpretation of the percentage of throttle
opening. TPS angle should display zero (0%) with the throttle closed and 100% at Wide Open Throttle (WOT).
ECT SENSOR VOLTS/ENG COOLANT TEMP – Range –40°
°°
° C to 151°
°°
° C / 0 – 5.00 Volts – T he Engine Coolant
Tem perature ( ECT) sens or is m ounted in the inlet manif old and sends engine tem perature inf orm ation to the PCM.
The PCM applies 5 Volts to the coolant temperature sensor circuit. The sensor is a thermistor which changes
internal resis tance as temperatur e c hanges. When the s ens or is c old (inter nal res istanc e high) , the PCM monitors a
high signal voltage which it interprets as a cold engine. As the sensor warms (internal resistance decreases), the
voltage signal will decrease and the PCM will interpret the lower voltage as a warm engine.
TFT SENSOR VO L T S/TRANS FLUID TEMP – Range –40°
°°
° C to 151 °
°°
° C / 0 – 5.00 Volts – T his pos ition will display
the PCM's interpretation of temperature in the transmission. The Transmission Fluid Temperature (TFT) sensor is
mounted in the valve body and is wired to the PCM. The PCM monitors the difference in voltage between two
terminals, and Tech 2 will display TFT in voltage and a temperature shown in degrees Celsius. The TFT sensor
reading should read close to the air tem perature when the transmission is cold, and increases as the transmission
fluid tem perature incr eases. After the engine is started the tem perature s hould rise steadily to about 82 ° C to 94° C
then stabilise.
TFP SWITCH A/B/C VOLTS – Range 0 Volts or 12 VOLTS – These values represent the three fluid pressure
switch ass em bly signals. These lines are norm ally high and are taken low as the f luid press ure switch interprets the
manual valve position. The sequence of these signals is decoded by the PCM to determine the appropriate gear
range. Zero volts indicates closed, and 12 volts indicates open.
TFP GEAR – Tech 2 Displays P/N-R,D,3,2,1 – This value represents the decoded sequence of the Transmission
Fluid Pressure Manual Valve Position Switch Assembly (TFP). The TFP is used to determine the manual valve
position. The manual valve position is an input to the PCM used to control line pressure, TCC, and shift solenoid
operation.
PRNDL SWITCH – Tech 2 Displays Invalid or P, R, N, D, 3, 2, 1 – This display is invalid if the vehicle is not
equipped with a PRNDL switch or, if equipped, indicates what gear the driver has selected.
1-2 SHIFT SOLENOID A, 2-3 SHIFT SOLENOID B – T he 2 Displays "ON" or "OFF" – This displays the "ON" or
"OFF" state of the two shift solenoids. The shift solenoids are turned "OFF" or "ON" to change gears.
1-2 AND 2-3 SHIFT SOLENOID FEEDBACK – Tech 2 Displays "ON" or "OFF" – These values represent the true
electrical state of the solenoids. The PCM uses this information to set malfunction DTC(s).
1-2 SHIFT TIM E – Tech 2 Displays T ime – This value repres ents the time tak en to shift fr om firs t gear to second
gear. This information is only accurate if the shift was adaptable.
2-3 SHIFT TIM E – Tech 2 Displays T ime – This value r epresents the tim e taken to s hift fr om s econd gear to thir d
gear. This information is only accurate if the shift was adaptable.
COMMANDED PCS – Tech 2 Range 0 to 1000 Milliamps – This value represents the commanded pressure
control solenoid current. The com manded current is determ ined from the m anual valve position, transm ission fluid
temperature, transmission output speed, shift solenoid state, TCC, A/C status, engine speed, TCC slip and the
throttle pos ition sensor . The com manded pressur e control s olenoid current is then us ed to control the transm iss ion
line pressure.
ACTUAL PCS – Tech 2 Range 0 to 1000 Milliamps – This value represents the actual pressure control solenoid
current. This value should always be very similar to the desired pressure control solenoid current. If the actual
deviates from the desired by 0.16 amps, a DTC will set.
PCS DUT Y CYCLE – T ech 2 Range 0 to 100 % – This value represents the pres sure control solenoid duty cycle.
This value is determined by the desired pressure control solenoid current.