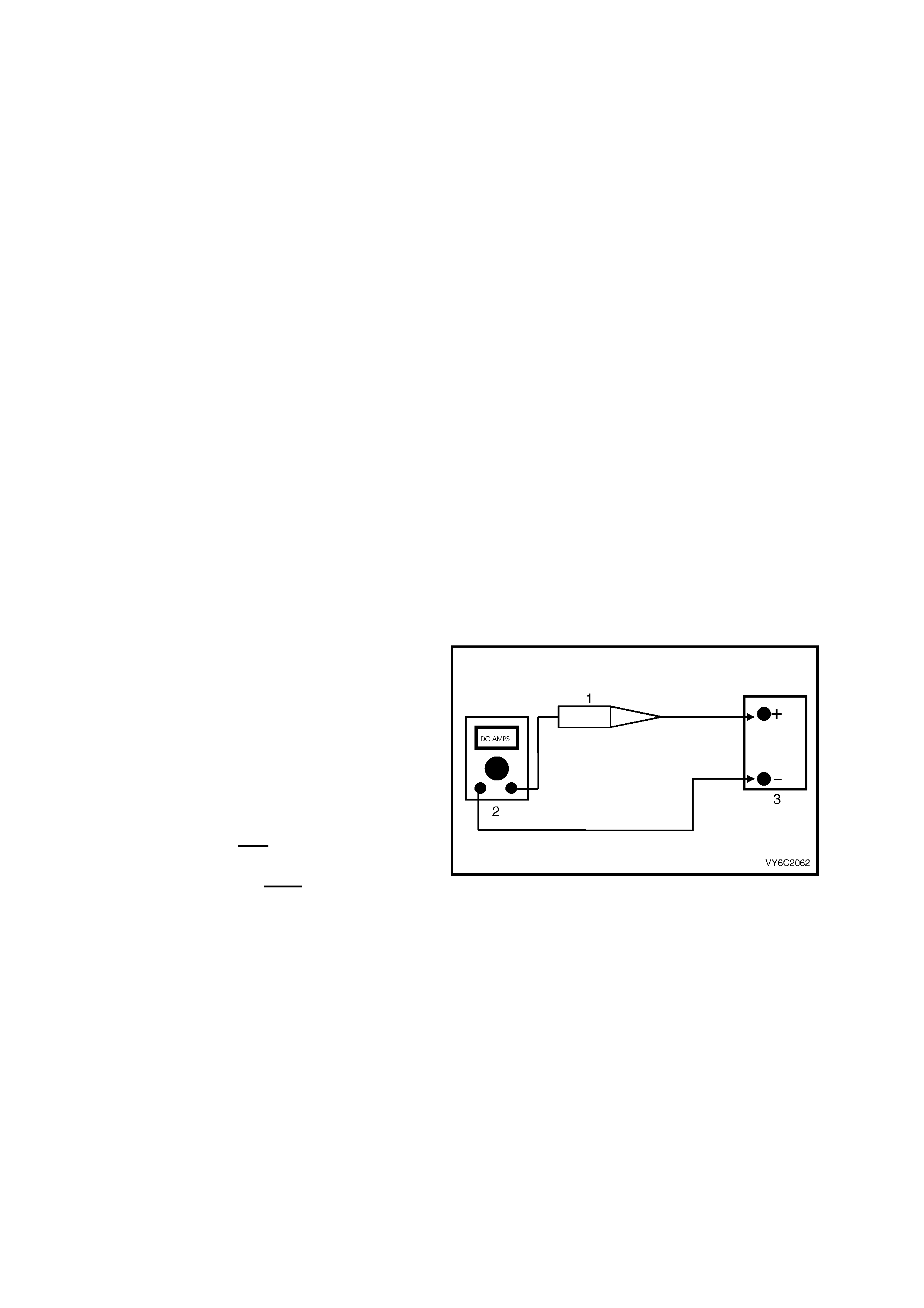
1. GENERAL DESCRIPTION
This Section describes the proper service procedures to repair components of the Powertrain Management
System, used with the V6 Supercharged engine. Emphasis is placed on the proper procedures and repair of
components related to this specific system.
1.1 SERVICE PRECAUTIONS
The following requirements must be observed when working on vehicles:
1. Before removing any PCM system component, disconnect the battery ground lead.
2. Never start the engine without the battery being solidly connected.
3. Never disconnect the battery from the on board electrical system while the engine is running.
4. When charging the battery, disconnect it from the vehicle's electrical system.
5. Never subject the PCM to temperatures above 80° C; i.e. paint oven. Always remove PCM first if this
temperature is to be exceeded.
6. Ensure that all cable harness plugs are connected solidly and that battery terminals are thoroughly clean.
7. The engine management system harness connectors are designed to fit in only one way; there are indexing
tabs and slots on both halves of the connector. Forcing the co nnector into place is not necessar y if it is be ing
installed with the proper orientation. Failure to take care to match the indexing tabs and slots to ensure the
connector is being installed correctly can cause damage to the connector, the module, or other vehicle
components or s ystem s .
8. Never connect or disconnect a cable harness plugs at the PCM when the ignition is switched "ON."
9. Before attempting any electric arc welding on the vehicle, disconnect the battery leads and the PCM
connectors.
10. When steam cleaning engines, do not direct the steam cleaning nozzle at PCM system components. If this
happens, corrosion of the terminals can take place.
11. Use only the test equipment specified in the diagnostic Tables, since other test equipment may either give
incorrect results or damage good components.
12. All vol tag e meas urements using a vo ltmeter mus t us e a dig ital voltmeter with an inter na l impedance r at in g of at
least 10 million ohms per volt (10 megohm/volt).
13. When a test light ( 1) is s pec ified, a " low-p ower"
test light must be used. Do not use a high –
wattage test light. While a particular brand of
test ligh t is no t sug geste d, a sim ple t est o n an y
test light will ensure it to be OK for PCM c ircuit
testing. Connect an accurate (2) Ammeter
(such as a high-impedance digital multimeter)
in series with the test light being tested, and
power the test light-ammeter circuit with the
ve hicle batt ery (3).
If the am meter indicat es less tha n 0.3 Am p current
flow (300 mA), the test light is OK to use.
If the ammeter indicates more than 0.3 Amp
current flow (or 300 mA), the test light is NOT OK
to use.
Figure 6C2-3-1
14. When fasteners are removed, always reinstall them at the same location from which they were removed. If a
fastener needs to be replaced, use the correct part number fastener for that application. If the correct part
number fastener is not available, a fastener of equal size and strength (or stronger) may be used. Fasteners
that are not to be re-used, or those requiring thread locking compound will be identified. The correct torque
value must be used when installing fasteners that require it. If the above conditions are not followed, parts or
system damage could result.