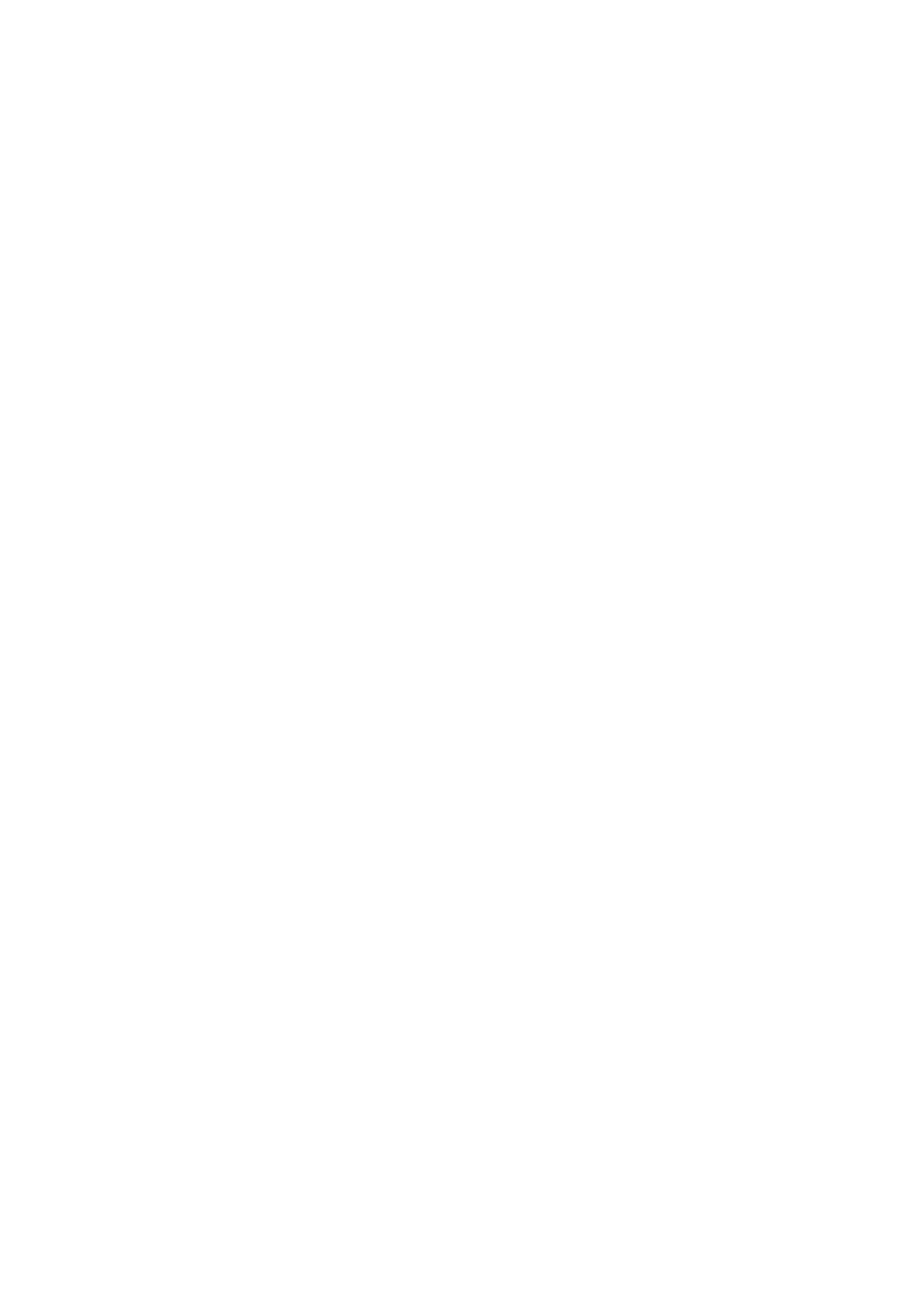
BARO: Tech 2 Displays a range of 10 to 105 kPa/0.00 to 5.00 Volts
The Barometric Pressure reading is determined from the MAP sensor signal. The PCM monitors the MAP signal
during key up and Wide-Open Throttle (WOT) conditions. The Barometric Pressure compensates for altitude
differences.
TPS ANGLE: Tech 2 Displays a range of 0 to 100%
Computed by the PCM from the TP sensor voltage. The TP angle should read 0% at idle to greater than 80% at
Wide Open Throttle.
TPS VOLTAGE: Tech 2 Displays a range of 0 to 5.10 Volts
Used by the PCM to determine the amount of throttle demanded by the driver. The TPS voltage should read
between 0.25 - 1.25 volts at idle to greater than 4 volts at wide open throttle.
AIR /FUEL RATIO: Tech 2 Displays a range of 0.00 : 99.99
The Air Fuel ratio is determined from the Heated Oxygen sensor outputs. The PCM uses the fuel trim to adjust
fuelling to attempt to maintain an Air Fuel Ratio of 14.7:1. A lower value indicates a richer commanded air fuel
mixture while a higher value indicates a leaner mixture.
FUEL SYSTEM STATUS: Tech 2 Displays “OPEN LOOP” or “CLOSED LOOP”
Closed Loop indicates that the PCM is controlling f uel delivery ac cording to oxygen sensor voltages. In Open Loop,
the PCM ignores the oxygen sensor voltage and bases the amount of fuel to be delivered on TP sensor, engine
coolant, and MAF sensor inputs only.
ENGINE LOAD: Tech 2 Displays a range of 0% to 100%
The PCM c alculates the engine load f r om engine speed and MAF sens or readings . The Engine Load increases with
an increase in RPM or airflow.
LEFT HO2S SENSOR READY (BANK 1) / RIGHT HO2S SENSOR READY (BANK 2): Tech 2 Displays “YES”
or “NO”
Indicates if the HO2S Sensors have reached operating temperature.
LEFT HO2S SENSOR (BANK 1) / RIGHT HO2S SENSOR (BANK 2): Tech 2 Displays a range of 0 to 1000 mV
The HO2S Bank 1 and Bank 2 Sensors parameter represents the fuel control exhaust oxygen sensor output
voltage. The voltage fluctuates constantly within a range between 10 mV (lean exhaust) and 1000 mV (rich
exhaust), while operating in Closed Loop.
LEFT SHORT TERM FUEL TRIM / RIGHT SHORT TERM FUEL TRIM: Tech 2 Displays the Percentage
The Short Term Fuel Trim represents a short-term correction to fuel delivery the PCM makes in response to the
amount of tim e the fuel contr ol oxygen sens or voltage spends above or below the 450 mV thr eshold. If the oxygen
sensor voltage mainly remains less than 450 mV, indicating a lean air/fuel mixture, short term fuel trim increases
into the positive range above 0% and the PCM adds fuel. If the oxygen sensor voltage stays mainly above the
threshold, the shor t term f uel trim decreas es below 0% into the negative range. The PCM reduces the fuel delivery
in order to compensate for the indicated rich condition. Under certain conditions such as an extended idle and a
high ambient temperature, the canister purge may cause the Short Term Fuel Trim to read in the negative range
during normal operation. The Fuel Trim values at maximum authority may indicate an excessively rich or lean
system.
LEFT LONG TERM FUEL TRIM / RIGHT LONG TERM FUEL TRIM: Tech 2 Displays the Percentage
The PCM derives the Long Term Fuel Trim from the Short Term Fuel Trim value. The Long Term Fuel Trim
represents a long-term correction of fuel delivery. A value of 0% indicates that the fuel delivery requires no
compensation in order to maintain the PCM commanded air/fuel ratio. A negative value significantly below 0%
indicates that the fuel system is rich and the PCM is reducing the fuel delivery (decreased injector pulse width). A
positive value significantly greater than 0% indicates that a lean condition exists and the PCM compensates by
adding f uel (increased injector puls e width). F uel trim values at m axim um authority indicates an exces sively rich or
lean system.
FUEL TRIM CELL: Tech 2 Displays a range of 0 to 23
The PCM determ ines from MAF and RPM inputs which fuel c ell to operate the engine in. A plot of RPM vs MAF is
broken into 24 cells. The fuel trim cell displayed on the scan tool is the cell that the engine is operating under.
FUEL TRIM LEARN: Tech 2 displays “ENABLED” or “DISABLED”
When conditions are appropriate f or enabling long ter m fuel tr im corr ections, the scan tool displays ENABLED. This
indicates that the long term fuel trim is responding to the short term fuel trim. If the scan tool displays DISABLED,
then long term fuel trim will not respond to changes in short term fuel trim.
LEFT SHORT TERM FUEL TRIM AVERAGE / RIGHT SHORT TERM FUEL TRIM AVERAGE: Tech 2 Displays
the Percentage
This parameter indicates the average of the short term fuel trim cells. The short term fuel trim cells are rated
(weighted) for the am ount of which they are used. F or exam ple, the PCM rates an idle cell higher than a wide open
throttle c ell. If a fuelling m alfunction is occurr ing in the idle cell and the wide open cell, the average would be more
affected by the idle cell. A negative value significantly below 0% indicates that the fuel system is rich and the PCM is
reducing the fuel delivery (decreased injector pulse width). A positive value significantly greater than 0% indicates
that a lean condition exis ts and the PCM is c om pensating by adding fuel (increas ed injector pulse width). When the
average of the cells reaches a predetermined high or low, a fuel trim DTC sets.