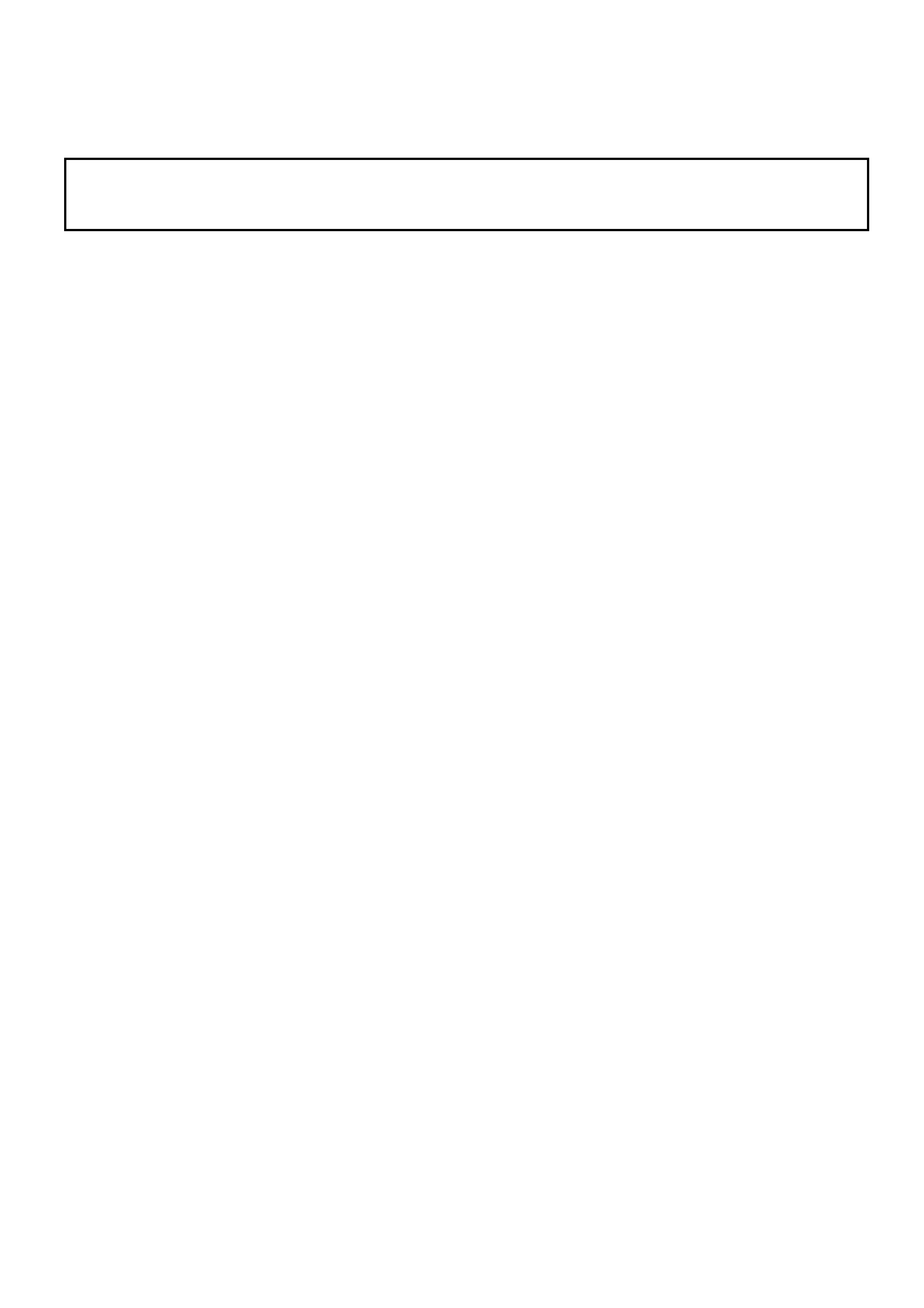
SECTION 6C3-2A - DIAGNOSTIC TABLES –
GEN III V8 ENGINE
IMPORTANT
Before performing any Service Operation or other procedure described in this Section, refer to Section 00
CAUTIONS AND NOTES for correct workshop practices with regard to safety and/or property damage.
CONTENTS
1. GENERAL INFORMATION
1.1 SYSTEM COMPONENT LOCATIONS
1.2 PCM WIRING DIAGRAMS
1.3 PCM CONNECTOR END VIEWS
PCM CONNECTOR A84-X1 (BLUE)
PCM CONNECTOR A84-X2 (RED)
1.4 PCM CONNECTOR TERMINAL DEFINITIONS
PCM CONNECTOR A84-X1 (BLUE)
PCM CONNECTOR A84-X2 (RED)
1.5 PIM CONNECTOR END VIEW
1.6 PIM CONNECTOR TERMINAL DEFINITIONS
1.7 ENGINE CONTROL CONNECTOR END VIEWS
1.8 AUTOMATIC TRANSMISSION IN-LINE
HARNESS END VIEWS
1.9 AUTOMATIC TRANSMISSION INTERNAL
CONNECTOR END VIEWS
1.10 ENGINE DIAGNOSTIC TROUBLE CODES
(DTC) – GEN III V8 – PCM
1.11 DIAGNOSTIC TROUBLE CODES (DTC) –
PIM GEN III V8 – PIM
1.12 DIAGNOSTIC TROUBLE CODES (DTC) –
GEN III V8 AUTOMATIC TRANSMISSION
2. GENERAL DIAGNOSTIC TABLES
2.1 TABLE A-1 – ON-BOARD DIAGNOSTIC (OBD)
SYSTEM CHECK
2.2 TABLE A-2 – CHECK POWERTRAIN
MALFUNCTION INDICATOR LAMP
2.3 DATA LINK CONNECTOR DIAGNOSIS
2.4 ENGINE CRANKS BUT DOES NOT RUN
2.5 ENGINE CONTROL RELAY DIAGNOSIS
2.6 FUEL PUMP RELAY CIRCUIT DIAGNOSIS
2.7 FUEL PUMP ELECTRICAL CIRCUIT
(UTILITY ONLY)
2.8 FUEL SYSTEM DIAGNOSIS
2.9 STARTER CRANKING CIRCUIT
3. DIAGNOSTIC TROUBLE CODE TABLES
DTC P0101 - MASS AIR FLOW SYSTEM
PERFORMANCE
DTC P0102 - MASS AIR FLOW SENSOR
CIRCUIT LOW FREQUENCY
DTC P0103 - MASS AIR FLOW SENSOR
CIRCUIT HIGH FREQUENCY
DTC P0107 - MANIFOLD ABSOLUTE
PRESSURE SENSOR CIRCUIT LOW
VOLTAGE
DTC P0108 - MANIFOLD ABSOLUTE
PRESSURE SENSOR CIRCUIT HIGH
VOLTAGE
DTC P0112 - INTAKE AIR TEMPERATURE
SENSOR CIRCUIT LOW VOLTAGE
DTC P0113 - INTAKE AIR TEMPERATURE
SENSOR CIRCUIT HIGH VOLTAGE
DTC P0117 - ENGINE COOLANT
TEMPERATURE SENSOR CIRCUIT
LOW VOLTAGE
DTC P0118 - ENGINE COOLANT
TEMPERATURE SENSOR CIRCUIT
HIGH VOLTAGE
DTC P0121 - THROTTLE POSITION
SENSOR CIRCUIT INSUFFICIENT
ACTIVITY
DTC P0122 - THROTTLE POSITION
SENSOR CIRCUIT LOW VOLTAGE
DTC P0123 - THROTTLE POSITION
SENSOR CIRCUIT HIGH VOLTAGE
DTC P0125 - ENGINE COOLANT
TEMPERATURE SENSOR EXCESSIVE
TIME TO CLOSED LOOP FUEL CONTROL
DTC P0131 - HEATED OXYGEN SENSOR
CIRCUIT LOW VOLTAGE BANK 1
SENSOR 1
DTC P0132 - HEATED OXYGEN SENSOR
CIRCUIT HIGH VOLTAGE BANK 1
SENSOR 1
DTC P0133 - HEATED OXYGEN SENSOR
SLOW RESPONSE BANK 1 SENSOR 1
DTC P0134 - HEATED OXYGEN SENSOR
INSUFFICIENT ACTIVITY BANK 1 SENSOR 1
DTC P0135 - HEATED OXYGEN SENSOR
HEATER CIRCUIT BANK 1 SENSOR 1
DTC P0151 - HEATED OXYGEN SENSOR
CIRCUIT LOW VOLTAGE BANK 2
SENSOR 1
DTC P0152 - HEATED OXYGEN SENSOR
CIRCUIT HIGH VOLTAGE BANK 2
SENSOR 1
DTC P0153 - HEATED OXYGEN SENSOR
SLOW RESPONSE BANK 2 SENSOR 1
DTC P0154 - HEATED OXYGEN SENSOR
INSUFFICIENT ACTIVITY BANK 2 SENSOR 1
DTC P0155 - HEATED OXYGEN SENSOR
HEATER CIRCUIT BANK 2 SENSOR 1
DTC P0171 - FUEL SYSTEM LEAN BANK 1
DTC P0172 - FUEL SYSTEM RICH BANK 1
DTC P0174 - FUEL SYSTEM LEAN BANK 2
DTC P0175 - FUEL SYSTEM RICH BANK 2
DTC P0218 - TRANSMISSION FLUID OVER-
TEMPERATURE
DTC P0230 – FUEL PUMP CONTROL CIRCUIT
DTC P0325 – KNOCK SENSOR SYSTEM
DTC P0327 – KNOCK SENSOR CIRCUIT
FRONT SENSOR
DTC P0332 – KNOCK SENSOR CIRCUIT
REAR SENSOR
DTC P0335 – CRANKSHAFT POSITION
SENSOR CIRCUIT
DTC P0336 – CRANKSHAFT POSITION
SENSOR CIRCUIT PERFORMANCE
DTC P0341 – CAMSHAFT POSITION
SENSOR CIRCUIT PERFORMANCE
DTC P0342 – CAMSHAFT POSITION
SENSOR CIRCUIT LOW VOLTAGE
DTC P0343 – CAMSHAFT POSITION
SENSOR CIRCUIT HIGH VOLTAGE
DTC P0351 – IGNITION CONTROL #1 CIRCUIT
DTC P0352 – IGNITION CONTROL #2 CIRCUIT