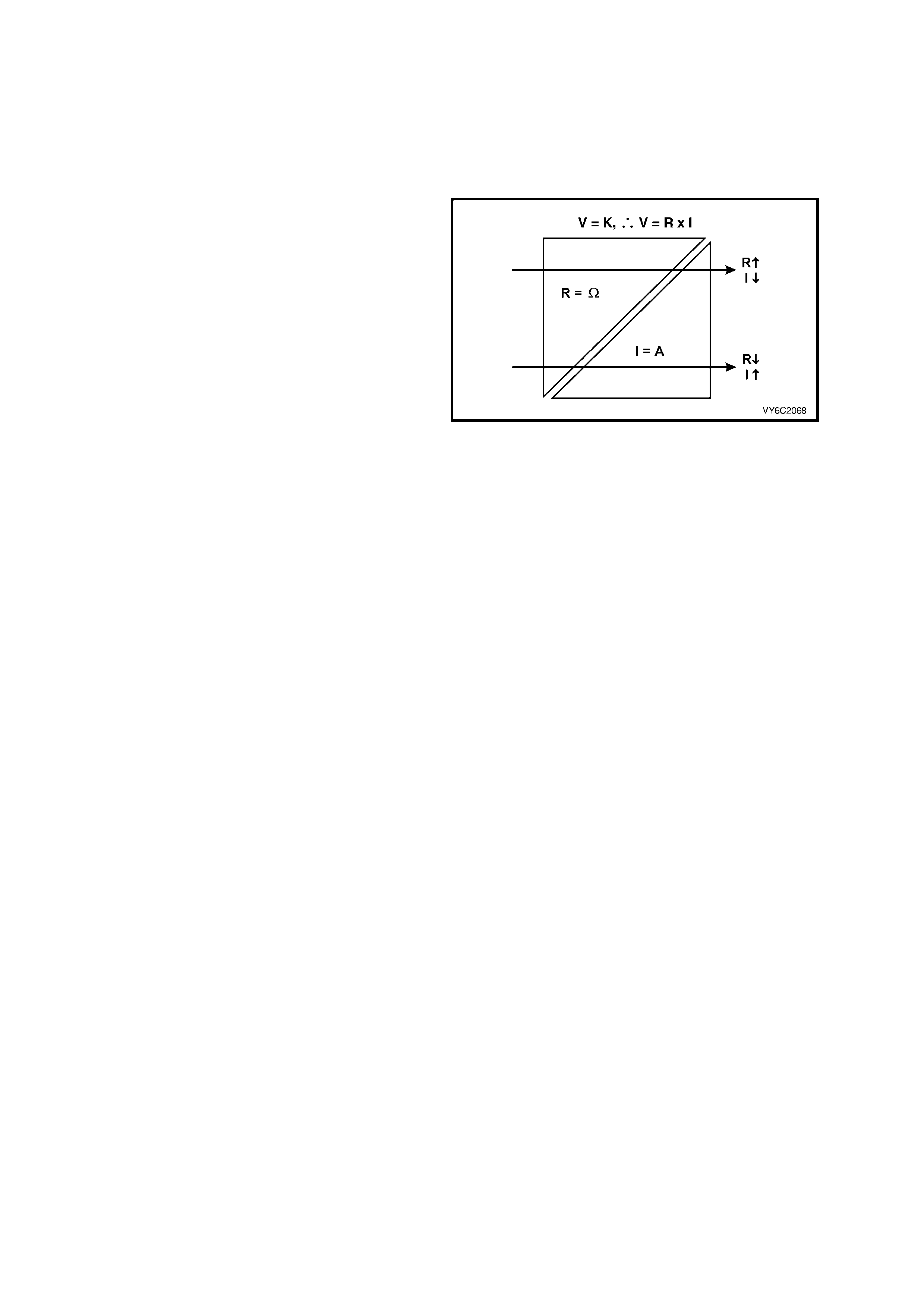
TESTING GROUNDS
Unusual displays in the instrument, lamps that are dim or flash unexpectedly, stop lamps that come on when the
indicators are used, are all classic symptoms of ground problems.
This section discusses the importance of good ground circuits and starts by explaining some basic theory. Then, the
diagnosis of a solid-state circuit ground condition is detailed, to help show how to correct a problem, should it occur.
BASICS
For a circuit to operate properly, three things are
needed:
a. A good power supply to components;
b. Good components and,
c. Sound ground circuits.
Circuits are complete systems; current must flow
from beginning to end as des igned, not hinder ed by
unexpected resistance anywhere in the circuit.
While some Technicians realise that the power
supply to a circuit must be free of unwanted
resistance, they can have difficulty in visualising
why a ground cir cuit mus t also be fr ee of unwanted
resistance.
For current to flow, the circuit must be complete; it
must pass through and out of a component like
water flowing thr ough a bathtub. With a free f lowing
tub (no plug inserted), the water can flow out as
freely as it flows in. In electrical term s , current m ust
also enter and leave components freely, if they are
to perform as they are designed.
Figure 6C2-2B-2
Sensitive, solid-s tate systems have their own ground points; high c urrent devic es (e.g. m otor s) do not ground at the
same location. High current devices can cause voltage spikes (sudden changes in voltage) when turned "ON" or
"OFF." To prevent these spikes from affecting sensitive solid-state circuits, two different types of different ground
location systems are used. An exam ple is the use of a dedicated wire to connec t an isolated ground junction bloc k
to the battery negative terminal. This wire reduces the effect of spikes on sensitive circuits at the ground junction
block.
Solid-state circuits are particularly sensitive to poor circuit continuity because, in most cases, they use low current
flow. T his Sec tion on ground c irc uits , c oncer ns itself with one solid-state devic e; the PCM. However, the inf or mation
included here can also be applied to all solid-state ground circuits.
Severe restrictions (i.e. resistance) in the ground circuit can cause resets and intermittent codes to set, in solid-state
systems. The PCM operates devic es such as fuel injec tors, idle air control (IAC), etc., and receives inputs from low
voltage sensors, such as the manifold absolute pressure sensor (MAP), crankshaft speed/position (CKP). These
input and output devices need good circuitry for correct operation.
Remember that, when maladjusted or imperfect sensors cause values to shift, they are usually accompanied by
driveability problems. If there is excessive resistance in the ground circuit, then the result will be the same; shifted
sensor outputs with corresponding driveability conditions. These conditions may not be severe enough to set
diagnostic trouble codes, but they will reduce vehicle efficiency and performance and may be noticed by the
customer.
SENSOR CIRCUIT GROUND SENSITIVITY – AN EXAMPLE.
Looking at the Throttle Position (TP) sensor circuit will provide an example of how a little resistance in the ground
circuit can cause problems. Figure 6C2-2B-3 shows a throttle position sensor (1) first with a good ground circuit (‘A’)
and then with a poor c onnection (‘B’) in the ground cir cuit. Refer to this illustration, as you proceed through the text
that follows:
First, the throttle position sensor consists of a resistor and a wiper and, one terminal of the resistor is connected to a
supply voltage (5 V) , while the other is connected to ground. As the wiper moves ac ross the r esistor, the voltage of
the wiper terminal progressively changes, with a change in the throttle position. If the wiper is near the supply
voltage end of the resistor, the wiper output will approach the supply voltage (over 4.5 volts at wide open throttle).
As the wiper m oves toward the grounded end of the resistor , the voltage of the wiper output decreases to near zero
(about 0.5 volts for the closed throttle in this example). Note though, that the actual closed and wide open throttle
voltage specifications may vary for different engines. Also, the sensor output should never be greater than reference
supply voltage or less than 0.20 volts. (The PCM would set a DTC, should this situation occur.)