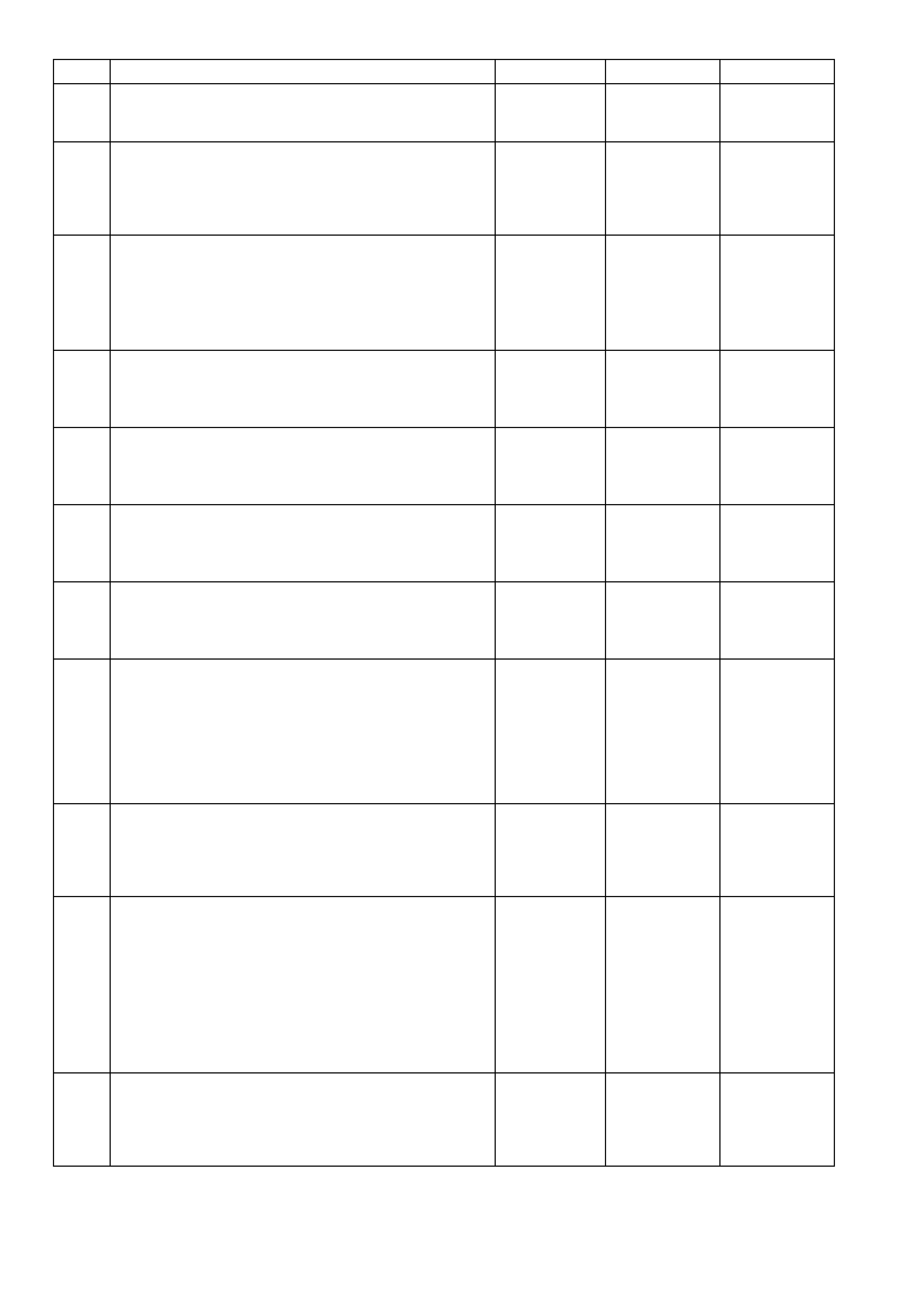
STEP ACTION VALUE YES NO
5. 1. Measure the resistance from terminal P of the J 39775
jumper harness to the transmission case.
Is the resistance greater than the specified value?
50 kΩ Go to Step 7 Go to Step 6
6. 1. Disconnect the A/T wiring harness connector from the
TFP manual valve position switch.
2. Measure the resistance from terminal D of the TFP
manual valve position switch to the switch housing.
Is the resistance greater than the specified value?
50 kΩ Go to Step 16 Go to Step 19
7. 1. Run the engine at idle.
2. Firmly apply the park brake.
3. Place the gear selector in R (Reverse).
4. Measure the resistance from terminal N of the J 39775
jumper harness to the transmission case.
Is the resistance less than the specified value?
200 ohm Go to Step 8 Go to Step 16
8. 1. Place the gear selector in 1 (First).
2. Measure the resistance from terminal N of the J 39775
jumper harness to the transmission case.
Is the resistance less than the specified value?
200 ohm Go to Step 9 Go to Step 16
9. 1. Place the gear selector in 3 (Third).
2. Measure the resistance from terminal R of the J 39775
jumper harness to the transmission case.
Is the resistance greater than the specified value?
50 kΩ Go to Step 10 Go to Step 16
10. 1. Place the gear selector in D (Drive).
2. Measure the resistance from terminal P of the J 39775
jumper harness to the transmission case.
Is the resistance less than the specified value?
200 ohm Go to Step 11 Go to Step 16
11. 1. Place the gear selector in 2 (Second).
2. Measure the resistance from terminal P of the J 39775
jumper harness to the transmission case.
Is the resistance greater than the specified value?
50 kΩ Go to Step 12 Go to Step 16
12. 1. Ignition OFF.
IMPORTANT: The resistance of the TFT sensor is
temperature dependent, and therefore varies far more than
any other device. Refer to Transmission Fluid Temperature
Sensor in this Section.
2. Measure the resistance from terminal L to terminal M
(TFT sensor) of the J 39775 jumper harness.
Is the resistance within the specified range?
3088 – 3942 Ω
@ 20°C
to
159 – 198 Ω
@ 100°C
Go to Step 13 Go to Step 14
13. 1. Measure the resistance from terminal L to the
transmission case.
2. Measure the resistance from terminal M to the
transmission case.
Are both resistances greater than the specified value?
50k Ω System OK Go to Step 14
14. 1. Disconnect the A/T wiring harness connector from the
TFP manual valve position switch.
IMPORTANT: The resistance of the TFT sensor is
temperature dependent, and therefore varies far more than
any other device. Refer to Transmission Fluid Temperature
Sensor in this Section.
2. Using a DMM, measure the resistance between
terminal A and terminal B of the TFP manual valve
position switch (TFT sensor).
Is the resistance within the specified range?
3088 – 3942 Ω
@ 20°C
to
159 – 198 Ω
@ 100°C
Go to Step 15 Go to Step 19
15. 1. Measure the resistance from TFP manual valve
position switch terminal A to the transmission case.
2. Measure the resistance from TFP manual valve
position switch terminal B to the transmission case.
Are both resistances greater than the specified value?
50k Ω Go to Step 16 Go to Step 19