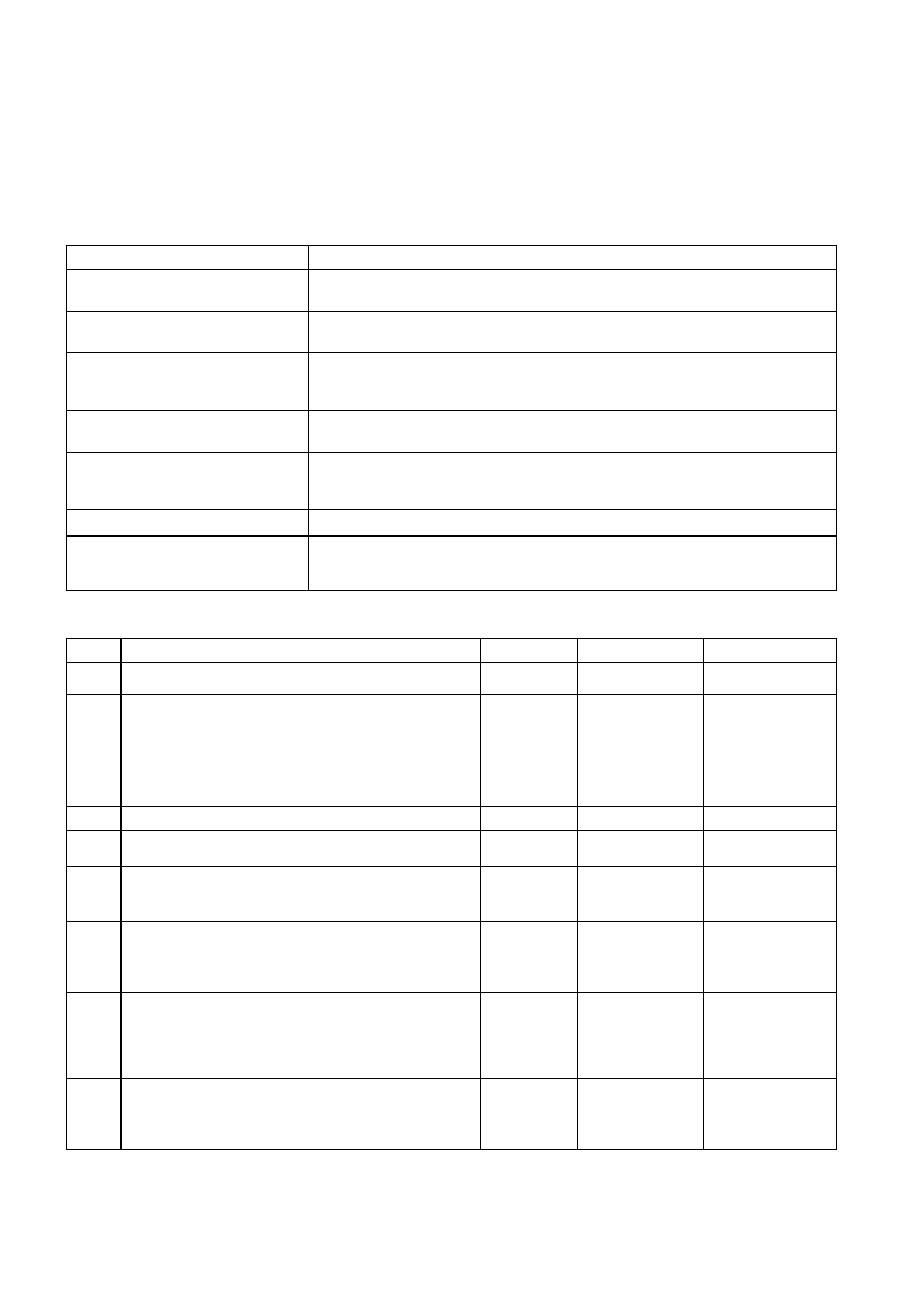
4. DIAGNOSIS
Many starting problems can be categorised as follows:
•
••
•
The starter motor will not crank the engine.
•
••
•
The engine cranks at normal speed, but will not start.
•
••
•
The starter motor cranks the engine very slowly.
W hen investigating a starting problem, f irst check the Probable Faults below; removing the starter motor might not
be neces sary. If the engine crank s over at the nor mal speed but will not star t, the problem is in the ignition system,
the fuel system or the engine.
SYMPTOM PROBABLE FAULT
Speed, torque and current low. •
••
•
High resistance in the motor. Poor positive brush terminal connection or
brush condition. Burnt segments on the commutator.
Speed and torque low, current high. •
••
•
Tight or worn bearings, bent armature shaft, insufficient end-play, armature
polling, short-circuit in the armature or grounded armature.
Armature does not rotate. No
current. •
••
•
Open circuit in the armature, positive brushes or solenoid. If the commutator
is burnt, there may be poor contact between the brushes and the commutator
and excessively worn or sticking brushes.
Armature does not rotate. High
current. •
••
•
Short-circuit in the solenoid switch. Armature physically prevented from
rotating.
Excessive brush movement
causing arcing at commutator. •
••
•
Low brush spring tension, worn or out-of-round commutator, thrown or high
segment on the commutator or insulation protruding between commutator
segments.
Excessive arcing at commutator. •
••
•
Defective armature winding, sticking brushes or dirty commutator.
Armature rotates but pinion does
not mesh with flexplate/flywheel
ring gear.
•
••
•
Pinion bearing fouled or burred. Damaged flexplate/flywheel ring gear or
broken pinion teeth.
NO CRANKING, NO SOUND FROM SOLENOID
STEP ACTION VALUE(S) YES NO
1 Turn headlamps and dome lamps on, turn ignition to
start position. Lamps dim Go to Step 2 Go to Step 3
2 1. Check battery
2. Charge battery
3. Check generator
4. Check current draw
5. Check cranking voltage at battery posts
Is 9.6 volts
present? Go to Step 7 Test battery.
If OK repair starter
motor.
3 6. Turn on radio. Operate OK Go to Step 4 Go to Step 6
4 7. Check voltage at solenoid switch terminal 50. Is 7.0 volts
present? Repair starter Go to Step 5
5 8. With key in start position, check at ignition
terminal 50. Is 7.0 volts
present? Repair wiring
ignition switch
starter motor
Replace ignition
switch
6 9. Check engine main wiring harness fusible link
and ignition connections. All OK Go to Step 7 Repair as
necessary and
recheck starting
system
7 10. Check voltage from engine block to battery
negative terminal, with key in start position
(positive lead on block).
Is 0.5 volts
or more
present?
Clean and
tighten negative
cable connection
and/or replace
cable
Go to Step 8
8 11. Check cranking voltage at starter ‘B’ terminal. Is 9.0 volts
present? Check fuse and
engine to main
wiring harness
connectors
Clean and tighten
positive cable
connection and/or
replace cable