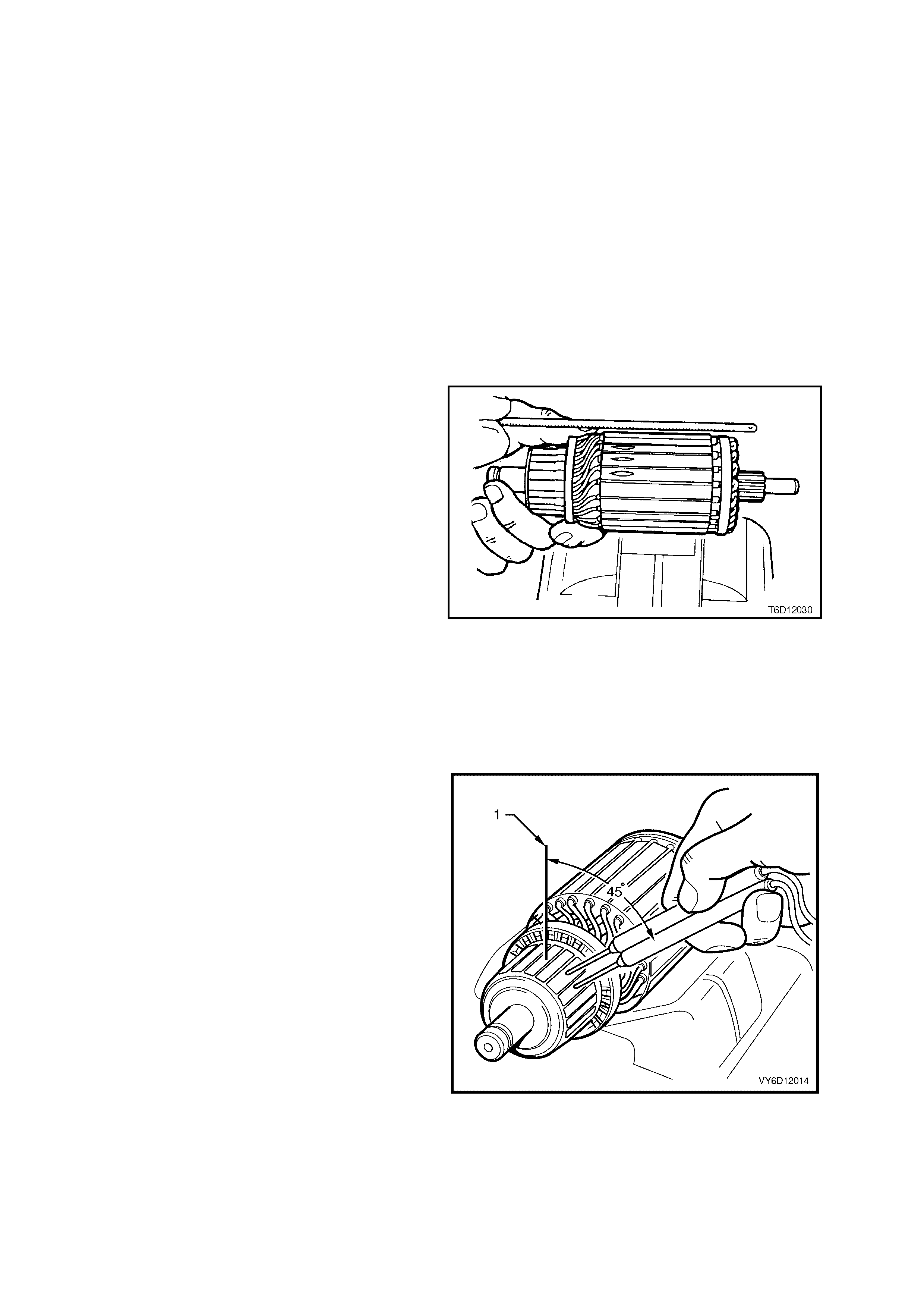
CLEANING AND INSPECTION
1. Clean and thoroughly inspect the disassembled components.
2. Wash all components (except the armature, brushes, solenoid switch and drive assembly) in a suitable cleaning
agent.
NOTE: Do not c lean the armatur e or permanent m agnets with cleaning solvent. Th is can damage the ins ulation or
contaminate the surfaces.
3. Clean the armature and permanent magnets with clean shop rags and compressed air.
NOTE: Do not clean the drive pinion assembly in solvent. This washes out the lubricant and can cause the drive
assembly to slip.
CAUTION: Use a non-volatile agent in a well ventilated area. Observe the safety regulations and
precautions issued by the manufacturer of the cleaning agent.
Check the Pole housing
1. Inspect the field housing and permanent magnet assembly for signs of damage, cracks and chips.
2. Replace the assembly if there are signs of damage.
Check the Armature
1. Check armature insulation res istanc e to gr ound
using a meggar or similar tester. A reading of
1 Megaohm or greater is required.
2. Check the armature for a short circuit.
3. Place the armature on a growler.
4. Switch the growler on.
5. Hold a hacksaw blade approximately 6 mm
above armature core and rotate the armature.
6. If the hacksaw blade vibrates significantly,
undercut the commutator, as follows:
a. Using a suitable small file, undercut
between each commutator segment to a
depth of approximately 0.8 mm.
b. Re-check the armature in the growler.
7. Replace the arm ature if the hacksaw blade still
vibrates significantly.
Figure 6D3-2-28
8. Exam ine the com mutator f or burnt or darkened s egments. A burnt or darkened com mutator s egment indicates
an open circuit winding attached to the segment.
9. Replace the armature if a segment is burnt or darkened.
10. Place the armature on a growler.
11. Use a voltmeter to measure the voltage
induced into the armature windings, as follows:
a. Choose two adjacent segments that are
approximately 45 degrees from the top of
the commutator (1).
b. Connect the voltmeter between the two
commutator segments.
12. Record the reading.
13. Rotate the armature in the growler so that the
next two commutator segments are in the
same position as the previous two.
14. Measure the voltage across these segments.
15. Record the reading.
16. Repeat these steps to measure the voltage
reading of all adjacent segments. The voltage
reading should be the same for each pair if
when positioned in the growler in the equivalent
location.
17. Replace the armature if a voltage reading
across any adjacent set of segments differs
significantly. This indicates that the armature
winding has an open circuit.
Figure 6D3-2-29