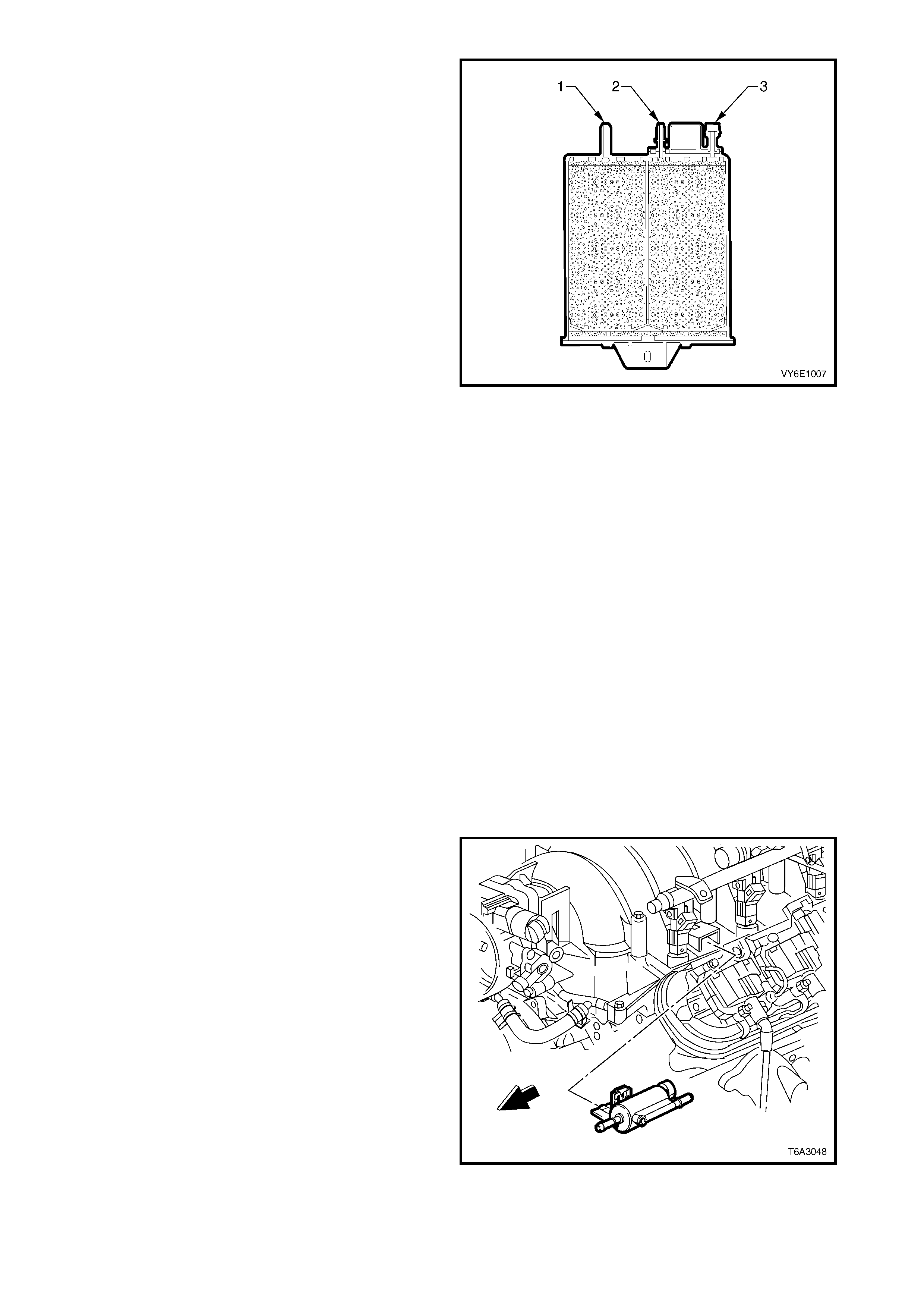
Fuel vapour from the fuel tank enters the canister via
the tank vent port (3). The fuel vapour is absorbed by
the charcoal within the canister.
W hen the engine is running at or above idle, manifold
vacuum on the canis ter purge port (2) caus es air to be
drawn in from the canister vent port (1). This air flow
purges fuel vapour from the canister which is then
transferred to the throttle body. The fuel vapour is
consumed in the normal combustion process.
The EVAP canister purge valve controls the manifold
vacuum that is applied to the canister. The PCM
energises the EVAP canister purge valve by supplying
an earth signal (purge on). The EVAP canister purge
valve control is Pulse Width Modulated (PWM). (This
means that the canister purge valve is turned on and
off several times a second.)
The PCM c ontrolled PW M output is com manded when
the appropriate conditions have been met, such as:
• Engine coolant temperature is below 20 °C at cold
start up and the engine has been running longer
than 3 minutes and 10 seconds, or
• Engine coolant temperature is above 80 °C and
the engine has been running longer than
5 seconds, or
• Engine is not in decel fuel cutoff mode and the
throttle opening is less than 96%, or
• The engine is in closed loop fuel mode.
Figure 6E3-10
A higher purge rate is used under conditions that are
likely to produce large amounts of vapour, when the
following conditions have been met:
• Intake Air Temperature (IAT) is above 50 °C, or
• Engine Coolant Temperature (ECT) is above
100 °C, or
• The engine has been running for more than
15 minutes.
The EVAP purge PW M duty cycle varies according to
operating conditions determined by mass air flow, fuel
trim and intake air temperature. The EVAP canister
purge valve is re-enabled when throttle position angle
decreases below 96%.
The EVAP purge PW M duty cycle varies according to
operating c onditions, determ ined by m ass air flow, fuel
trim and intake air temperature. The EVAP canister
purge valve is re-enabled when TP angle decreases
below 96%.
Figure 6E3-11