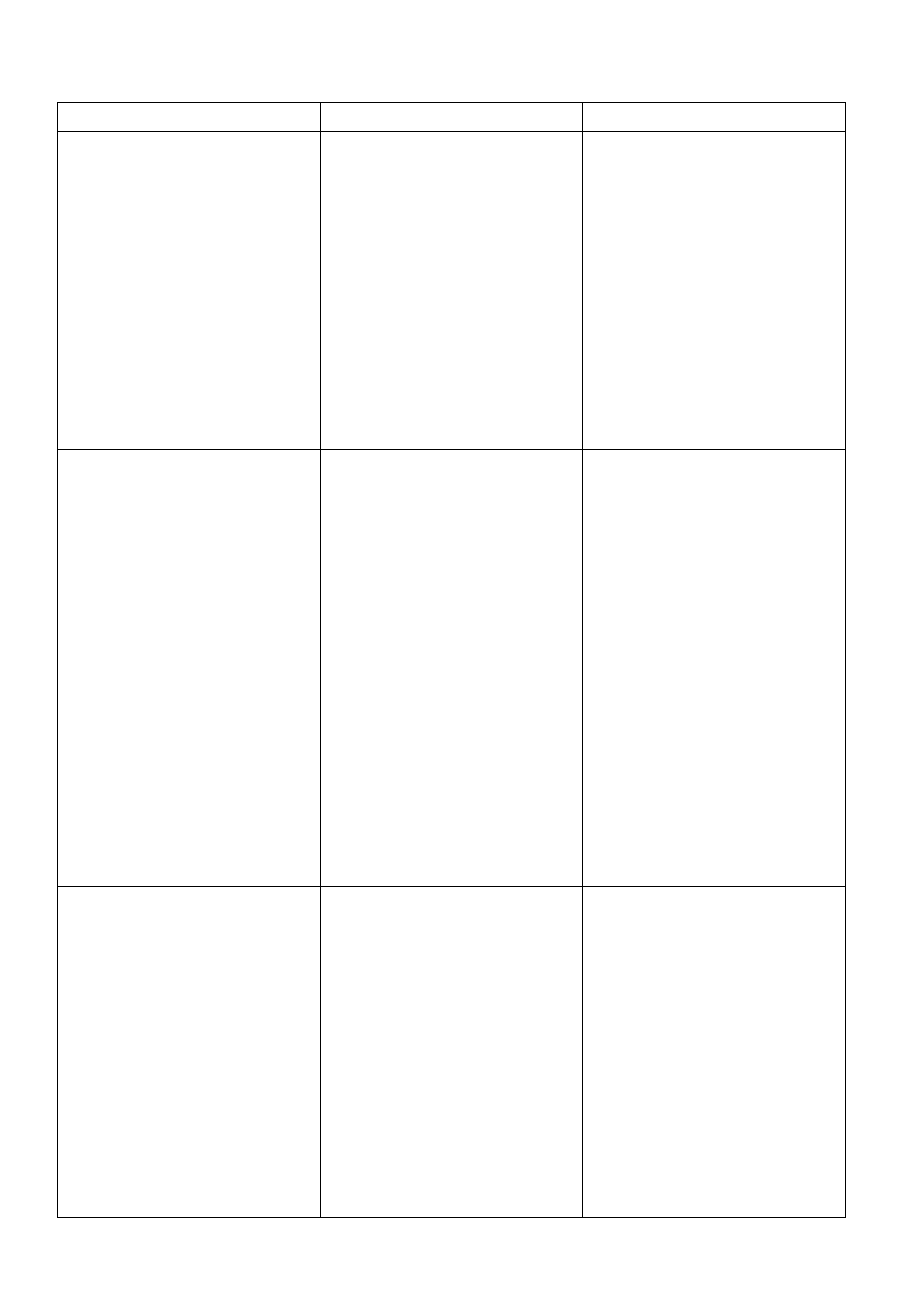
4. DIAGNOSIS
CONDITION PROBABLE CAUSE CORRECTIVE ACTION
SLIPPING Worn or oil-soaked lining.
Grease on linings from excessive
application to the input shaft
splines.
Driven plate sticking on main drive
gear splines.
Weak or broken diaphragm spring.
Master or actuating cylinder
defective
Replace driven plate, correct oil
leak.
Replace driven plate, remove
excess lubrication.
Clean spli nes and check clutch hub
for a free sliding fit.
Replace pressure plate and
diaphragm assembly. Refer
3.9 Clutch Driven Plate, Pressure
Plate and/or Throwout Bearing,
in this Section.
Overhaul defective cylinder as
detailed in 3.5 Master Cylinder or
3.6 Clutch Actuating Cylinder, in
this Section.
DRAG OR FAILURE TO
RELEASE Air trapped in hydraulic system.
Leak In hydraulic system.
Clutch master or actuating cylinder
defective.
Cracked or oil-soaked linings.
Excess ive dri ven pl ate run- out or
distorted.
Driven plate sticking on splines.
Main drive gear spigot partially
seized in crankshaft spigot bush.
Bleed system as outlined under
3.3 Clutch H ydraulic S ystem Bleed,
in this Section.
Correct leak and bleed hydraulic
system .
Overhaul defective cylinder as
outlined under 3.5 Master Cylinder
or 3.6 Clutch Actuating Cylinder, in
this Section.
Replace clutch driven plate. Refer
3.9 Clutch Driven Plate, Pressure
Plate and/or Throwout Bearing, in
this Section.
Replace driven plate. Refer
Operation 3.9 Clutch Driven Plate,
Pressure Plate and/or Throwout
Bearing, in this Section.
Clean spli nes and check clutch hub
for a free sliding fit.
Remove clutch, replace bush.
Refer 3.11 Cr ank shaf t Spig ot Bush,
in this Section.
GRAB OR CHATTER Oil on linings.
Worn main drive gear splines.
Rough, or grooved, flywheel or
pressure plate.
Loose engine m ountings .
Loose or worn prope ll er sh af t
coupling/s or damaged pinion
flange.
Defective clutch dr i ven plat e.
Defective dual mass flywheel.
Replace driven plate, correct oil
leak.
Replace main drive gear.
Replace flywheel or replace both
flywheel and pr ess ur e plate.
Tighten or replace mountings.
Tighten or replace propeller shaft
coupling/s and/or pinion flange.
Replace clutch driven plate. Refer
3.9 Clutch Driven Plate, Pressure
Plate and/or Throwout Bearing, in
this Section.
Replace dual mass flywheel. Refer
3.10 Dual Mass Flywheel, in this
Section.