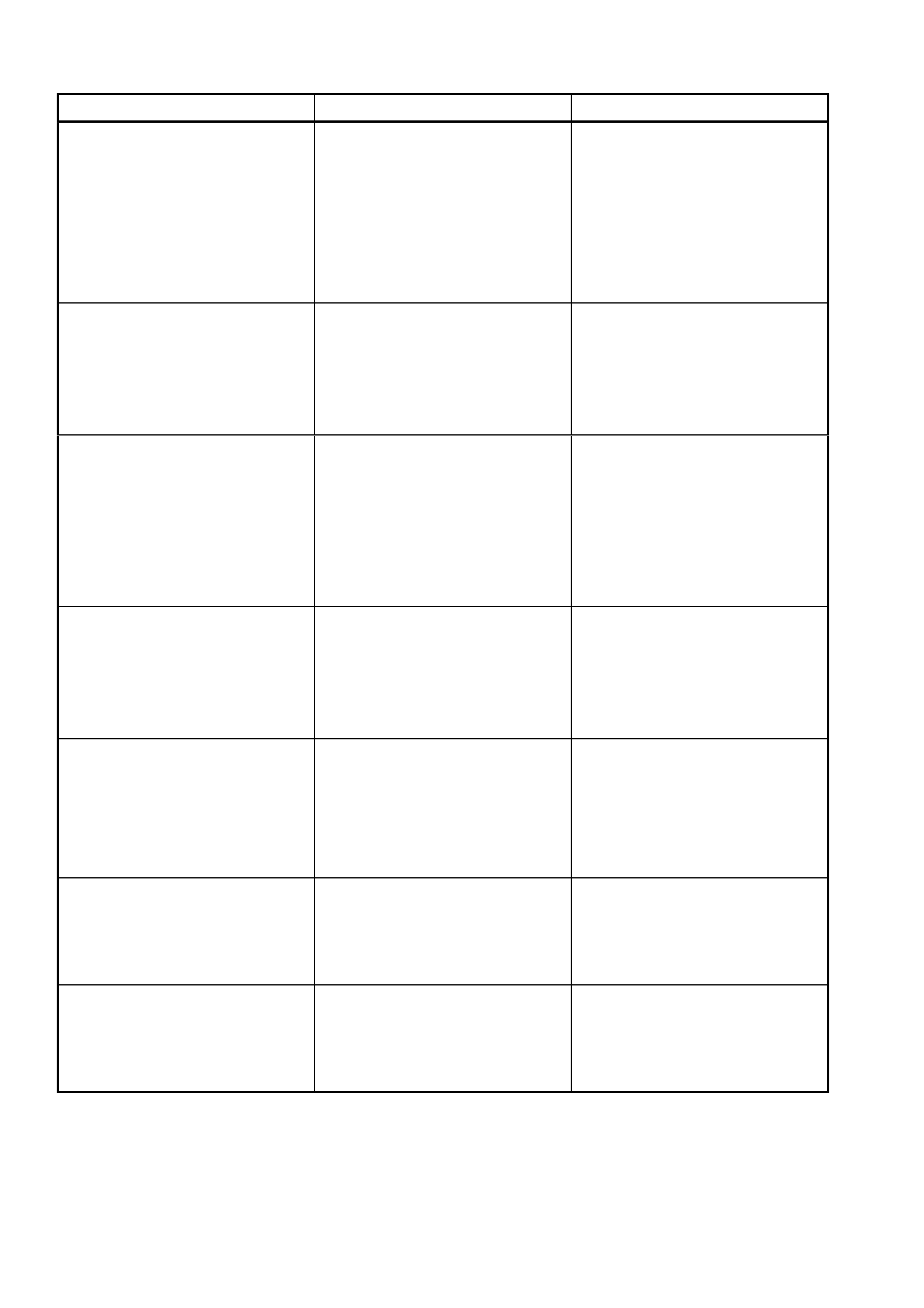
5. DIAGNOSIS
CONDITION PROBABLE CAUSE CORRECTION
TRANSMISSION SHIFT
HARD/HEAVY Clutch pedal high effort.
Shifter shaft binding.
Internal bind in transmission caused
by shift forks, selector shafts or
synchromes h assemblies.
Incorrect lubr ica nt.
Lubricate or replace as required.
Check for mispositioned shift fork roll
pin/s, loose bolts, worn shifter shaft or
shaft bores or distorted oil seal.
Repair as necessary.
Remove, disa ss em ble and ins pect
transmission. Replac e worn or
damaged components as necessary.
Drain and refill transmission.
GEAR CLASH WHEN SHIFTING
FROM ONE GEAR TO ANOTHER Lubricant level low or incorrect
lubricant.
Gearshift components or
synchromesh assemblies worn or
damaged.
Drain and refill transmission and
check for lubricant leaks if level was
low. Repair as necessary.
Remove, disa ss em ble and ins pect
transmission. Replac e worn or
damaged components as necessary.
TRANSMISSION NOISY Lubricant level low or incorrect
lubricant has been used.
Transmission housing to engine
attaching.
Gearshift mechanism, transmission
gears or bearing components worn or
damaged.
Drain and refill transmission. If
lubricant was low, check for leaks and
repair as necessary .
Check and correct bolt torque settings
as necessary.
Remove, disa ss em ble and ins pect
transmission. Replac e worn or
damaged components as necessary.
JUMPS OUT OF GEAR Gearshift mechanism, shift forks,
selector shafts, interlock pin, detent
balls/springs, worn or damaged.
Gear teeth worn or tapered,
synchromesh assemblies worn or
damaged.
Remove, disa ss em ble and ins pect
transmission assembly. Replace worn
or damaged components as
necessary.
Remove, disa ss em ble and ins pect
transmission. Replace all worn or
damaged components as necessary.
WILL NOT SHIFT INTO ONE GEAR Gearshift selector shaft/s, interlock pin
or selector arm, worn, damaged or
incorrectly assembled.
Synchromesh sleeves or hubs, worn
or damaged.
Remove, disa ss em ble and ins pect
transmi ssi on sel ector assembl ies.
Repair or replace components as
necessary.
Remove, disa ss em ble and ins pect
transmission. Replac e worn or
damaged co mpo nent s.
LOCKED IN ONE GEAR -
CANNOT BE SHIFTED OUT Shift shaft/s worn or damaged,
selector fork bent or broken.
Gearshift mechanism worn, damaged
or broken. Worn or damaged gear
train components.
Inspect and replace worn or damaged
components.
Disassemble transmission. Replace
damaged part s or assemble c orrect ly .
TRANSMISSION WILL NOT SHIFT
INTO REVERSE (ALL OTHERS OK) Worn or damaged internal
components.
Reverse block mechanism jammed
Remove transmission. Check for
damaged reverse gear trai n
components.
Dismantle transmission, inspect and
replace components as necessary.