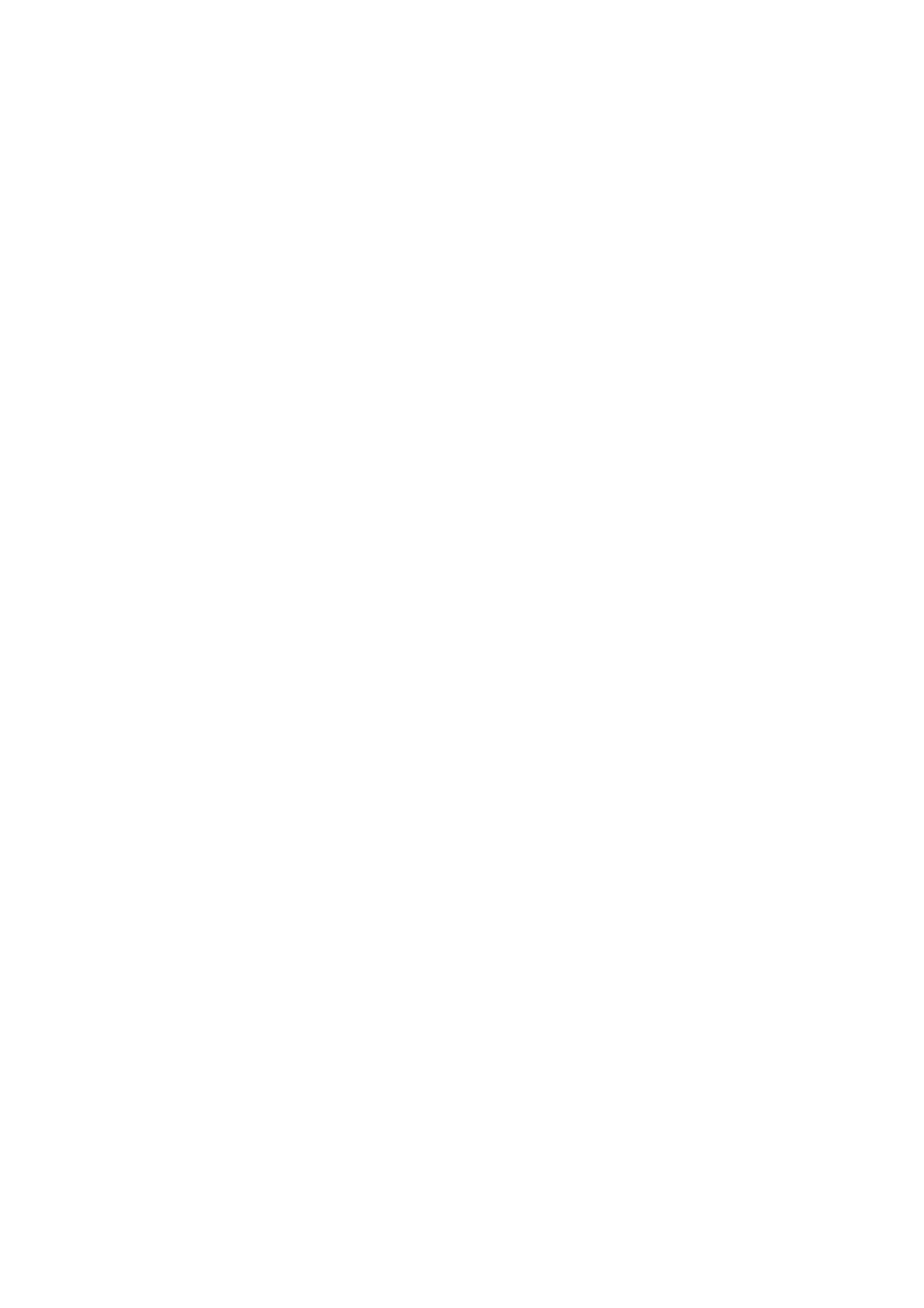
1. GENERAL INFORMATION
As detailed in 7C1, material contained within this Section, details service operations that can be carried out on a
transmission while it is still installed in the vehicle. In addition, the procedures required to remove and reinstall the
transmission assembly from/to the vehicle are also detailed.
General servicing information is also included in this Section and it is recommended that this material be read and
followed, whenever servicing operations are to be carried out on this transmission.
Dependent on vehicle specifications for different markets, the gearshift selector mechanism may be fitted with a
Brake Transmission Selector Interlock (BTSI) device that is colloquially referred to as “Bitsi”. Refer to
Section 7C1 GENERAL INFORMATION for a description of this device and its operation. Within this Section, the
service procedures for both selector types are described.
1.1 GENERAL SERVICE PRECAUTIONS
RECOMMENDATIONS
When servicing the transmission, all parts should be cleaned and inspected as outlined under 'Clean and Inspect',
in these recommendations. Individual units should be reassembled before disassembly of other units to avoid
confusion and interchanging of parts.
1. Thoroughly clean the transmission exterior before removal of any component.
2. Disassembly and reassembly must be made on a clean work bench. Cleanliness is of the utmost importance.
The bench tools, and parts must be kept clean at all times.
3. Before installing screws and other fasteners into aluminium parts, DIP SCREWS INTO TRANSMISSION FLUID
(Only use Dexron III) to prevent galling aluminium threads and to prevent screws from seizing.
4. To prevent thread stripping, always use a torque wrench when installing screws.
5. If threads in aluminium parts are stripped or damaged, the part can be made serviceable by the use of
commercially available, thread inserts.
6. Protective tools must be used when assembling seals to prevent damage. The slightest flaw in the sealing
surface of the seal can cause an oil leak.
7. Aluminium castings and valve parts are very susceptible to nicks, burrs, etc., and should be handled with care.
8. Internal snap rings should be expanded and external snap rings compressed if they are to be re-used. This will
ensure proper seating when reinstalled.
9. O-rings, gaskets and oil seals that are removed should not be re-used.
10. Teflon oil seal rings should not be removed unless damaged.
11. During assembly of each unit, all internal moving parts must be lubricated with transmission fluid.
OIL COOLER PIPES
Should any transmission fluid cooling pipe suffer accidental damage, then a genuine replacement pipe must be
fitted. Refer to the current release of PartFinder® to determine the correct part number for the particular engine
and pipe involved. Reworking of damaged pipes or hand made replacements are not permitted.
Clean And Inspect
After complete disassembly of a component, wash all metal parts in a clean solvent and dry with compressed air.
Blow oil passages out and check to make sure they are not obstructed. Small passages should be checked with tag
wire. All parts should be inspected to determine which parts are to be replaced.
Pay particular attention to the following:
1. Inspect linkage and pivot points for excessive wear.
2. Bearing and thrust surfaces of all parts should be checked for excessive wear and scoring.
3. Check for broken seal rings, damaged ring lands and damaged threads.
4. Inspect seal and O-rings.
5. Mating surf aces of cas tings should be chec ked for burrs . Irregularities m ay be rem oved by lapp ing the surf ace
with emery paper. The emery paper is laid on a flat surface, such as a piece of plate glass.
6. Castings should be checked for cracks and porosity.
NOTE: Do not use solvents on neoprene seals, composition faced clutch plates or thrust washers as damage to
parts may occur.