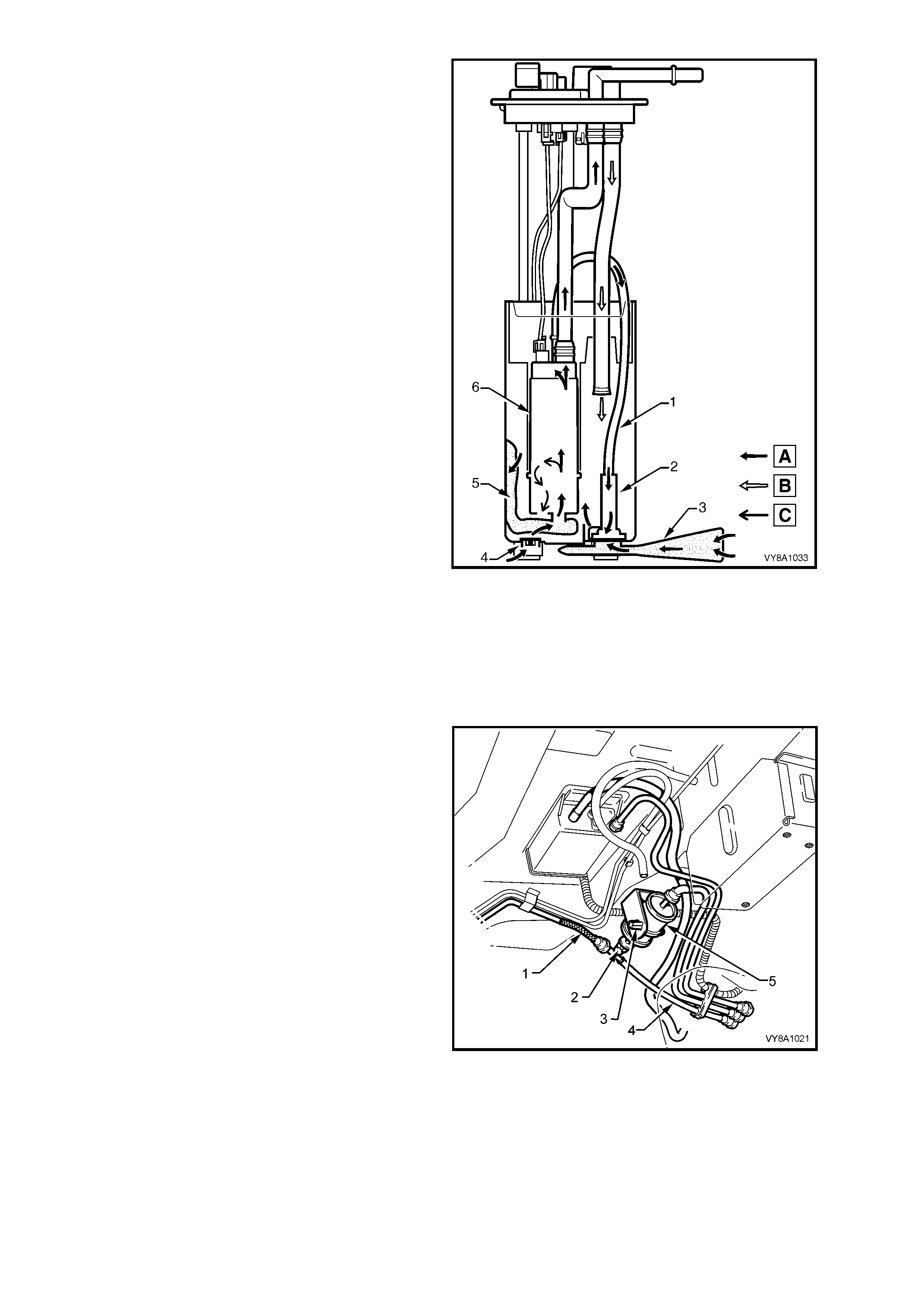
Fuel (A) enters the dual s tage turb ine f uel pum p (6)
via the ex ternal st rainer (3) and of the modular fuel
pump and sender assembly. In the first stage, the
pump separates the vapour (B) from the fuel. First
stage fuel is directed to the reservoir filling the
reservoir bucket.
Fuel levels in the reservoir are also maintained by
return fuel (B) via the return line. Reservoir fuel
flow proceeds through the fuel pump strainer (5),
bypassing the first stage impeller. Fuel then
proceeds to the second impeller and the high-
pressure third stage of the impeller pump.
High-press ure fuel then flows through the end cap.
Attached to the pump outlet is a diver ter that allows
the primary fuel volume to flow into the flex pipe
and deliver a portion of the f low to the jet pump via
an aspirator (1) and the rest to an externally-
mounted fuel filter and the engine.
The diverted fuel from the outlet of the fuel pump
passes through the j et pump filter (2). This c reates
a low pressure area at its base, causing the
umbrella valve (4) to unseat, drawing cooler fuel
into the reservoir area.
When the enigne is switched off, the reservoir
rem ains full of fuel, due to the action of the prim ary
umbrella valves. At higher fuel levels, fuel overflow
enters the reservoir over the top of the reservoir.
If the external strainer becomes blocked or restricts
fuel entry, the secondary umbrella valve (4)
unseats, allowing fuel to enter the reservoir area.
Electrical power is supplied to the fuel pump by a
connector secured to the cover. An internal
harness assem bly com pletes the connection to the
pump (not shown).
Figure 8A1–8
SINGLE LINE FUEL DELIVERY SYSTEM — GEN III V8 ENGINE
Fuel from the single turbine fuel pump is forced
through the fuel pump flex pipe and exits the
assem bly through the fuel feed output fitting on the
cover. Fuel then flows through the fuel filter (5)
mounted to a bracket (3) secured to the floor pan.
From here, fuel is directed through the fuel filter T -
piece (2) and the f lex ible f uel f eed line ( 1) and on to
the engine bay and fuel rail. When fuel line
pressure exceeds the pre-determined value of
410 k Pa, the fuel pressure regulator in the modular
fuel pump and sender assembly opens, allowing
excess system pressure to discharge back to the
module fuel sender assembly reservoir via the
flexible line (4). This process continuously occurs
while the pump is operating.
Figure 8A1–9