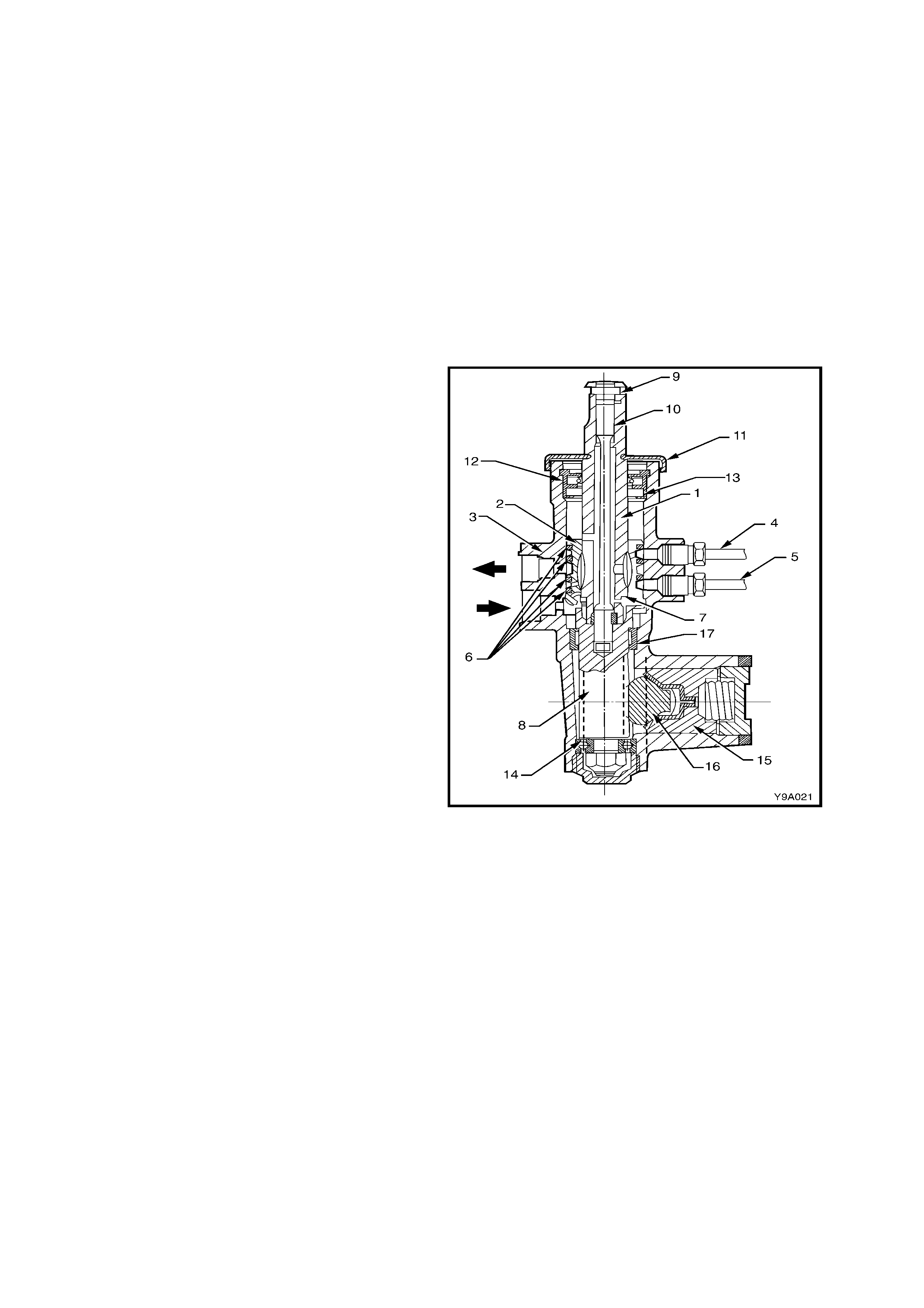
1.1 GENERAL DESCRIPTION - POWER STEERING RACK AND PI NION
The power steering gear features a variable ratio rack and pinion that is made possible by the unique
design of the r ac k teeth. This means that the effec tive pitc h radius of the pinion is les s in the st raight ahead
position than on turns. This results in less turns being required from lock to lock. For example, 3.5 turns
would be required if the ‘on centre’ ratio was used from lock to lock, whereas only 2.7 turns are required
with this Gear design.
Referring to Figure 9-1, the helical toothed pinion (8) is supported in the steering gear housing (2) by a
needle roller bearing (13) at the upper end, a ball race ( 14) at the lower end and a roller bear ing (17) at the
upper end of the pinion teeth.
The rack (16) operates within the housing and is supported at one end by a rack bearing and at the other
end by the pinion ( 8) and a s pring loaded pad (15), which m aintains slack free adjus tment of the r ack (16)
with the pinion (8).
The tie rods are connec ted to each end of the rack by pre-as sembled soc kets and to the steer ing arms by
sealed for life type tie rod end sockets.
PRINCIPLES OF OPERATION
With the engine running and the steering wheel in
the neutral position (s traight ahead) , power steering
fluid flows continuously from the power steering
pump to the steering gear and back to the pump,
via the power steering fluid reservoir. In this
steering mode, very little pressure is required to
maintain the high power s teering fluid flow rate that
occurs at this time. As a result, little engine power
is required to operate the system.
When turning the steering wheel to either side,
power steering fluid flow from the pump is directed
by a rotary control valve fitted to the steering gear,
to whichever side of the rack piston is appropriate,
as indicated by the steering wheel position. The
power steering fluid pressure then increases as
necessary, to provide the required steering
assistance.
This rotary control valve assembly, is located
between the input shaft (1) and the pinion (8), in the
steering gear.
As shown, the rotary valve assem bly consists of an
inner member (1) which forms part of the input
shaft and a surrounding sleeve member (2). The
whole valve, rotates in the steering gear housing
(3) as the steering wheel is turned, but it is the
slight relative movement of the inner and the sleeve
members that controls and directs the power
steering fluid flow.
Power steering fluid is fed to the valve (➨) and from
there, to the left ( 4) and right (5) sides of the power
piston via circumferential grooves in the outer
sleeve, that are sealed by PTFE seals (6). Excess
power steering fluid is returned to the reservoir.
The outer s leeve is coupled by a s tepped pin (7) to
the rack pinion (8), while the input shaft (1) is
coupled to the rack pinion by a pinned (9), flexible,
torsion bar (10) that provides a mechanical but
flexible link between the two members.
In the straight ahead position, the valve remains
centred. As steering effort requirements increase,
the torsion bar flexes, causing slight relative
rotation between the input shaft and sleeve,
directing power steering fluid and providing power
assistance as needed.
Figure 9-1