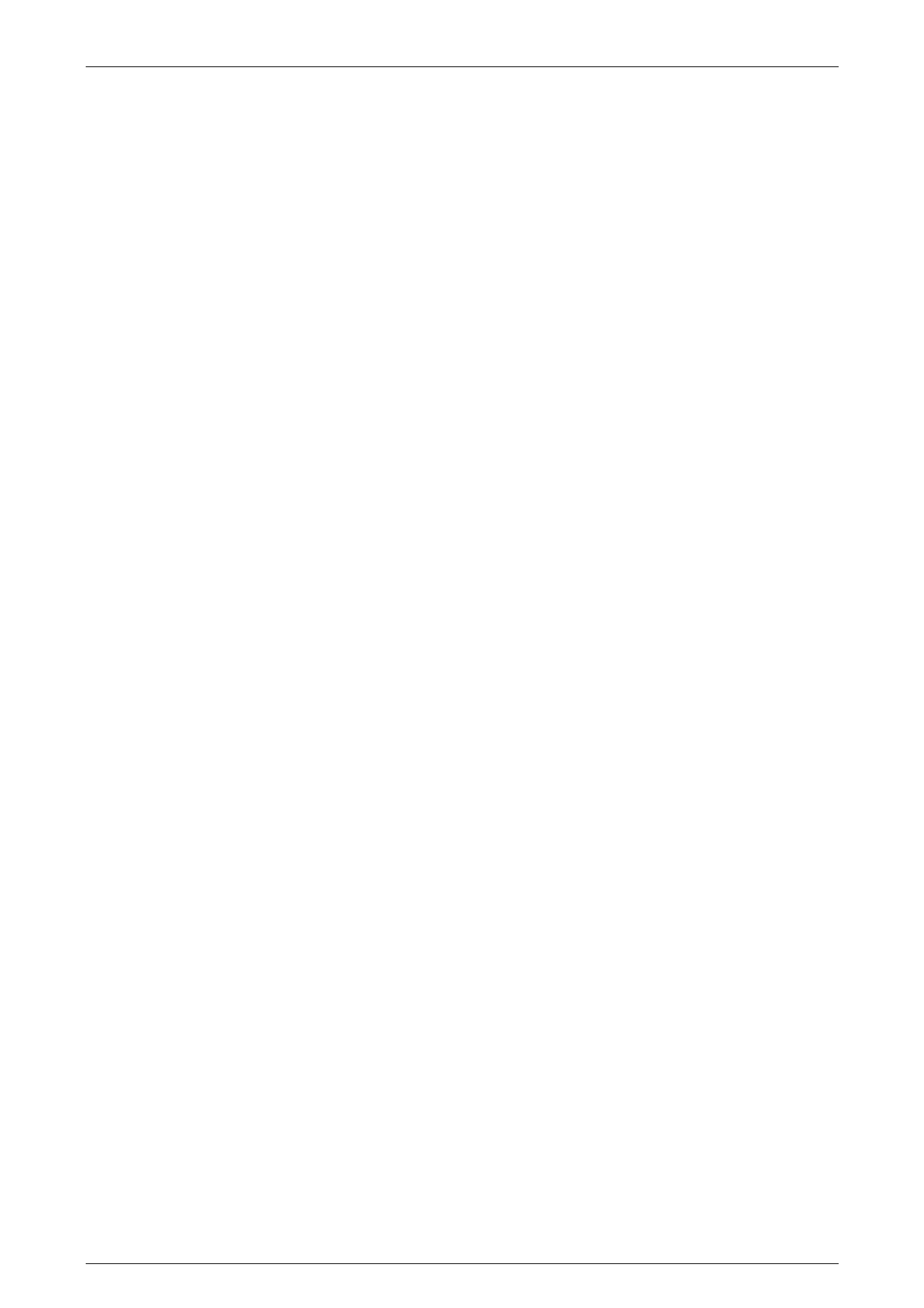
Rear Axle Page 4B –2
Page 4B–2
3.2 Rear Axle and Differential Housing Assembly...................................................................................................56
Preliminary Check ................................................................................................................................................57
Disassemble .........................................................................................................................................................58
Inspect...................................................................................................................................................................62
Reassemble ..........................................................................................................................................................62
3.3 Differential Assembly – M78 Series (Standard Non LSD) .................................................................................63
Disassemble .........................................................................................................................................................63
Inspect...................................................................................................................................................................66
Differential Case ...............................................................................................................................................66
Differential Side and Pinion Gears....................................................................................................................67
Ring Gear and Pinion Gear ..............................................................................................................................69
Bearings ...........................................................................................................................................................69
Reassemble ..........................................................................................................................................................70
3.4 Differential Assembly – M78 Series (Cone Type Limited Slip) .........................................................................73
Disassemble .........................................................................................................................................................74
Inspect...................................................................................................................................................................76
Differential Case ...............................................................................................................................................76
Differential Side Gears and Pinion Gears.........................................................................................................76
Ring Gear and Pinion .......................................................................................................................................77
Bearings ...........................................................................................................................................................77
Reassemble ..........................................................................................................................................................77
3.5 Differential Assembly – M86 Series (Multi-Disc Type Limited Slip) .................................................................82
Disassemble .........................................................................................................................................................83
Inspect...................................................................................................................................................................87
Differential Case ...............................................................................................................................................87
Differential Side Gears and Pinion Gears.........................................................................................................87
Differential Concentric Grooved Disc’s, Clutch Plates, Retainers and Dished Spacers....................................87
Ring Gear and Pinion .......................................................................................................................................87
Bearings ...........................................................................................................................................................88
Reassemble ..........................................................................................................................................................88
3.6 Differential Assembly Adjustment and Installation Procedures – All Models ................................................92
Differential Side Bearing Preload And Shim Selection .....................................................................................92
Side Bearing Preload Shim Selection Chart .....................................................................................................93
Hypoid Pinion Bearing Preload Shim Selection ................................................................................................96
Hypoid Pinion Shim Selection Table.................................................................................................................99
Hypoid Pinion Bearing Preload Shim Selection Chart ......................................................................................99
Pinion Installation............................................................................................................................................100
Differential Backlash Setting.............................................................................................................................103
Ring Gear and Pinion Contact Pattern .............................................................................................................105
Tooth Marking Terminology ............................................................................................................................105
Ideal Contact.......................................................................................................................................................107
Drive Side .......................................................................................................................................................107
Coast Side ......................................................................................................................................................107
Acceptable Heel Contacts .................................................................................................................................108
Drive Side .......................................................................................................................................................108
Coast Side ......................................................................................................................................................108
Acceptable Toe Contacts...................................................................................................................................109
Drive Side .......................................................................................................................................................109
Coast Side ......................................................................................................................................................109
4. Diagnosis............................................................................................................................................ 110
4.1 General Information ...........................................................................................................................................110
Road Test............................................................................................................................................................110
Tyre Noise...........................................................................................................................................................110
Front Wheel Bearings ........................................................................................................................................110
Transmission Rear Bearing (Manual Transmission).......................................................................................111
Backlash Clunk...................................................................................................................................................111
Drive-Line Snap.................................................................................................................................................. 111
Engine and Other Contributing Factors: .........................................................................................................111
Vehicles with Manual Transmission:...............................................................................................................111