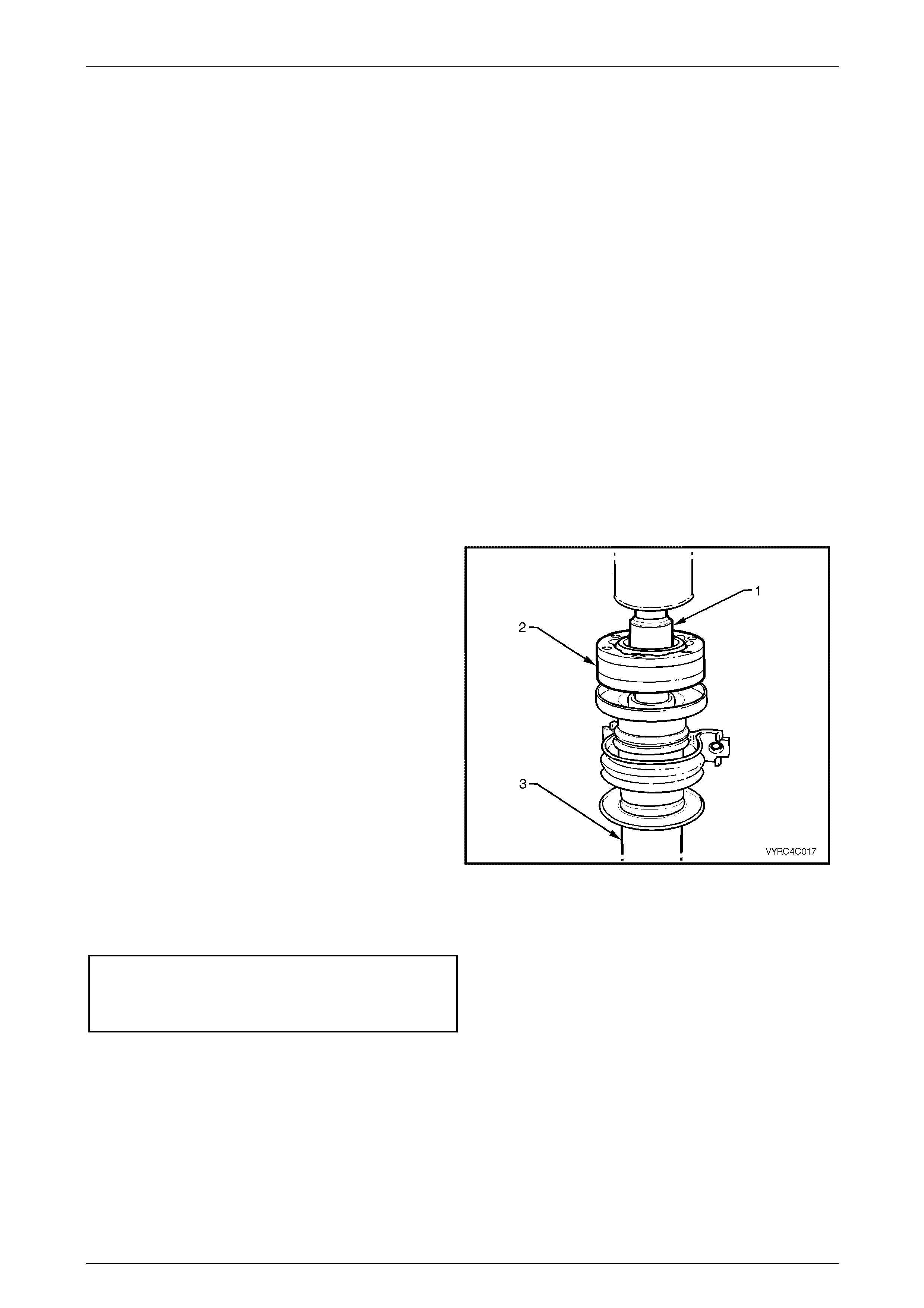
Propeller Shaft And Universal Joints Page 4C –11
Page 4C–11
Reassemble
The reassembly procedure for the constant velocity joint is the reverse of the disassembly procedure, noting the following
points:
1 Ensure all alignment marks are aligned to return all components to there original orientation.
2 Check the multi direction movement of the constant velocity joint for binding or restriction.
3 Pack the cons tant velocity joint with the recommended lubricating grease; refer to 3, Specifications in this Section.
4 Ensure the reassembled constant velocity joint is kept free from contamination until required for reinstallation to the
propeller shaft.
Reinstall
The installation procedure is the reverse of the removal procedure, noting the following points:
1 Ensure the cons tant velocity joint and associated parts are clean to ensure maximum life expectancy.
2 Inspect the dust shield and rubber boot assembly for cracks, tears or damage and replace if necessary then install
it to the front propeller shaft spindle.
3 Pack the cons tant velocity joint with the recommended lubricating grease, refer to 3, Specifications in this Section
or use the lubricating grease supplied in the repair kits available for the constant velocity joint, the dust shield and
rubber boot. Ensure the grease is worked in by hand onto all surfaces inside the joint.
4 Prior to pressing the constant velocity joint onto the front propeller shaft spindle, ensure all alignment marks are
aligned.
5 Using a suitable socket or tube (1), press the constant
velocity joint (2) onto the propeller shaft spindle (3)
while ensuring the socket or tube presses only on the
inner race of the joint only. Refer to Figure 4C-17.
6 Install the constant velocity joint retaining circlip to the
propeller shaft spin dle.
7 Ensure the mating surfaces of the constant velocity
joint, dust shield and rear propeller shaft companion
flange is clean.
8 Install a new gasket between the constant velocity
joint and the rear propeller shaft companion flange.
9 Apply a bead of the recommended sealant to the
mating surfac es of the dust shield and constant
velocity joint. For details on the sealant refer to
3 Specifications in this Section.
10 Install the rubber boot to propeller shaft spindle
retaining clip.
11 Install the constant velocity joint to rear propeller shaft
the attaching bolts and locking plates then tighten to
the correct torque specification.
(8) Constant velocity joint
to rear propelle r shaft
attaching bolts
torque specification ...................................... 32 – 36 Nm
12 Install the propeller shaft, as detailed in
2.1 Propeller Shaft in this Section.
Figure 4C-17