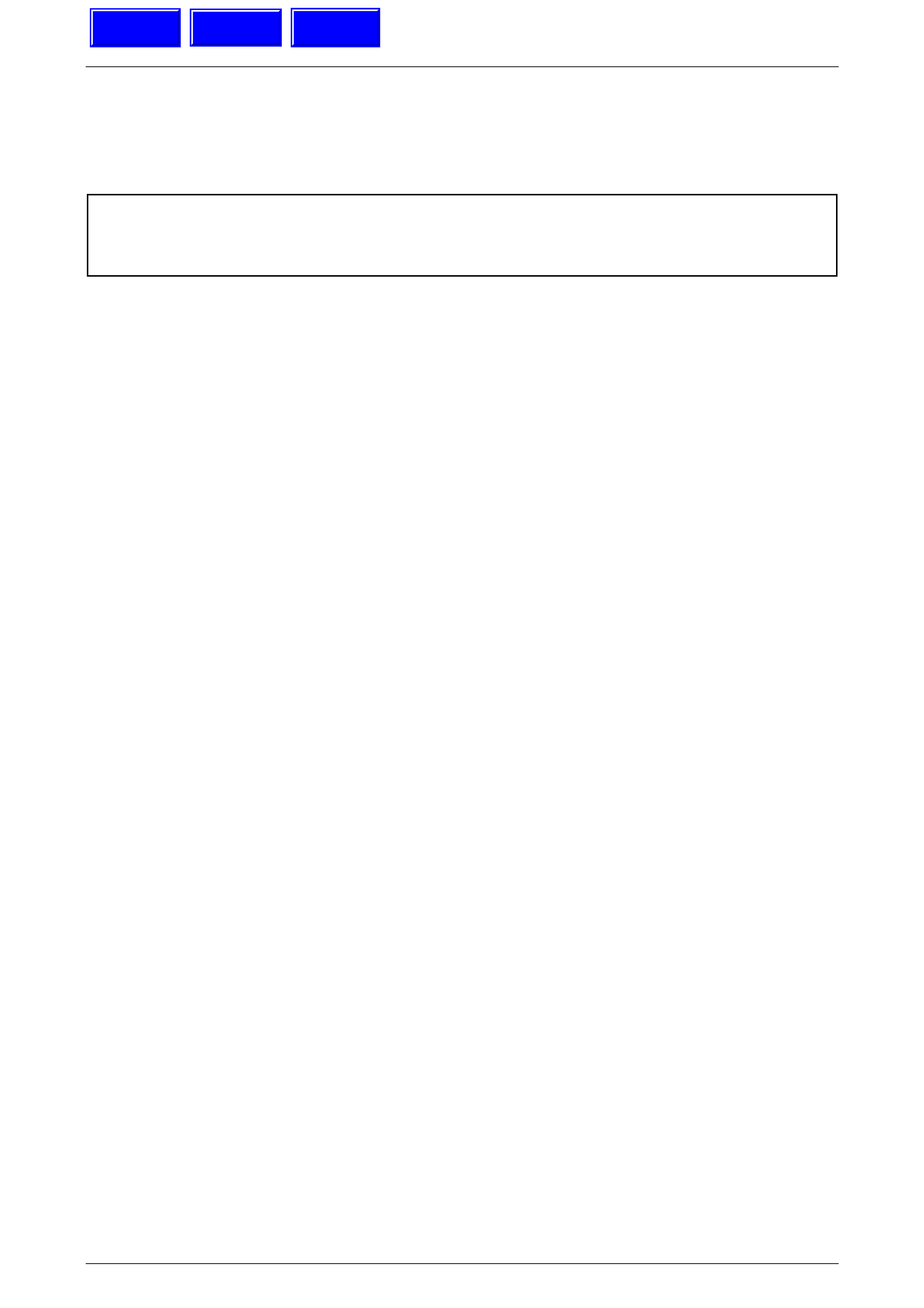
Service An d Pa r k Br a king Syste m Page 5A –1
Page 5A–1
Section 5A
Service and Park Braking System
ATTENTION
Before performing any Service Operation or other procedure described in this Section, refer to Section 00
CAUTIONS AND NOTES for correct workshop practices with regard to safety and/or property damage.
1 General Information............................................................................................................................... 3
1.1 General Description ...............................................................................................................................................3
1.2 Brake Pipes and Hoses..........................................................................................................................................4
Description..............................................................................................................................................................4
1.3 Pressure Differential Spool Valve.........................................................................................................................5
Description..............................................................................................................................................................5
1.4 Load Sensing Proportioning Valve.......................................................................................................................6
Description..............................................................................................................................................................6
Operation ................................................................................................................................................................7
1.5 Rear Brake Backing Plates and ABS Sensors.....................................................................................................8
Description..............................................................................................................................................................8
2 Minor Service Operations..................................................................................................................... 9
2.1 Service Notes..........................................................................................................................................................9
General Information...............................................................................................................................................9
Important Items...................................................................................................................................................9
2.2 Rear Park Brake Cables.......................................................................................................................................11
Remove .................................................................................................................................................................11
Reinstall ................................................................................................................................................................12
2.3 Rear Caliper Brake Hose......................................................................................................................................13
Remove .................................................................................................................................................................13
Reinstall ................................................................................................................................................................13
2.4 Rear Brake Supply Hose......................................................................................................................................15
Remove .................................................................................................................................................................15
Reinstall ................................................................................................................................................................16
2.5 Load Sensing Proportioning Valve.....................................................................................................................17
Remove .................................................................................................................................................................17
Reinstall ................................................................................................................................................................19
3 Major Service Operations ................................................................................................................... 20
3.1 Service Notes........................................................................................................................................................20
General Information.............................................................................................................................................20
Important Items.................................................................................................................................................20
3.2 Master Cylinder ....................................................................................................................................................22
3.3 Brake Booster.......................................................................................................................................................23
3.4 Brake Caliper (Front and Rear) ...........................................................................................................................24
3.5 Front Brake Disc...................................................................................................................................................25
3.6 Rear Brake Disc....................................................................................................................................................26
3.7 Park Brake Lining Wear, Check ..........................................................................................................................27
3.8 Park Brake Shoe, Adjust ......................................................................................................................................28
3.9 Park Brake Shoe...................................................................................................................................................29
3.10 Front Disc Brake Shield.......................................................................................................................................30
3.11 Rear Disc Brake Backing Plate and Disc Shield................................................................................................31
Remove .................................................................................................................................................................31
Inspect...................................................................................................................................................................35
Reinstall ................................................................................................................................................................35