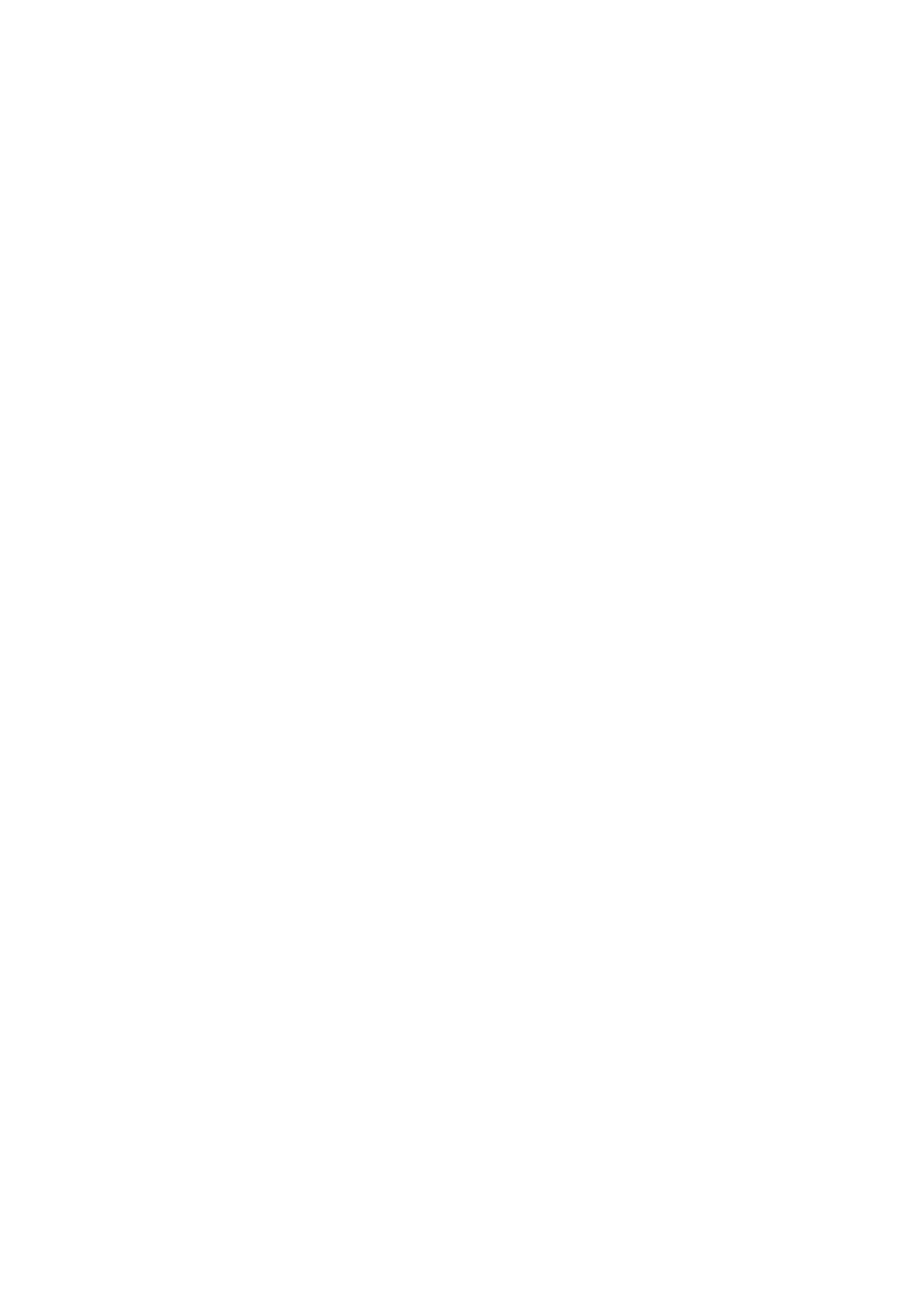
2.14 BODY STRUCTURE PANELS
UNDERBODY
1. Reinforcing assembly - inner seat attachment.
2. Reinforcing - floor panel side.
3. Floor assembly - front.
4. Mount assembly - power unit.
5. Extension assembly - floor panel front.
6. Brace - longitudinal to front floor.
7. Bracket - ABS modulator upper.
8. Bracket - ABS modulator lower.
9. Bracket - support modulator lower.
10. Tray assembly - battery.
11. Bracket assembly - -theft deterrent horn
mounting.
12. Panel assembly - front fender skirt.
13. Frame work - underbody front.
14. Cross member assembly - front (member
assembly - front lower).
15. Panel assembly – front.
16. Panel assembly - front upper.
17. Front panel - side.
18. Bracket - radiator support side.
19. Support - front panel side.
20. Bracket - bumper beam mounting
21. Console - front panel.
22. Longitudinal assembly (front).
23. Crossmember assembly (RH) centre.
24. Crossmember assembly (LH) centre.
25. Hook tie down rear.
26. Extension assembly - longitudinal (rear).
27. Crossmember assembly - rear.
28. Bracket assembly - brake hose.
29. Longitudinal - complete.
30. Frame work assembly - rear.
31. Reinforcement assembly - back panel lower.
32. Bumper beam mounting bracket assembly
(rear).
33. Heat shield assembly - intermediate muffler
LH.
34. Heat shield assembly - intermediate muffler
RH.
35. Heat shield - rear muffler.
36. Web plate – rear Left Hand.
37. Stand assembly - spare wheel.
38. Back panel assembly - lower.
39. Web plate – rear Right Hand.
40. Floor assembly - rear.
41. Reinforcement assembly - centre bearing.