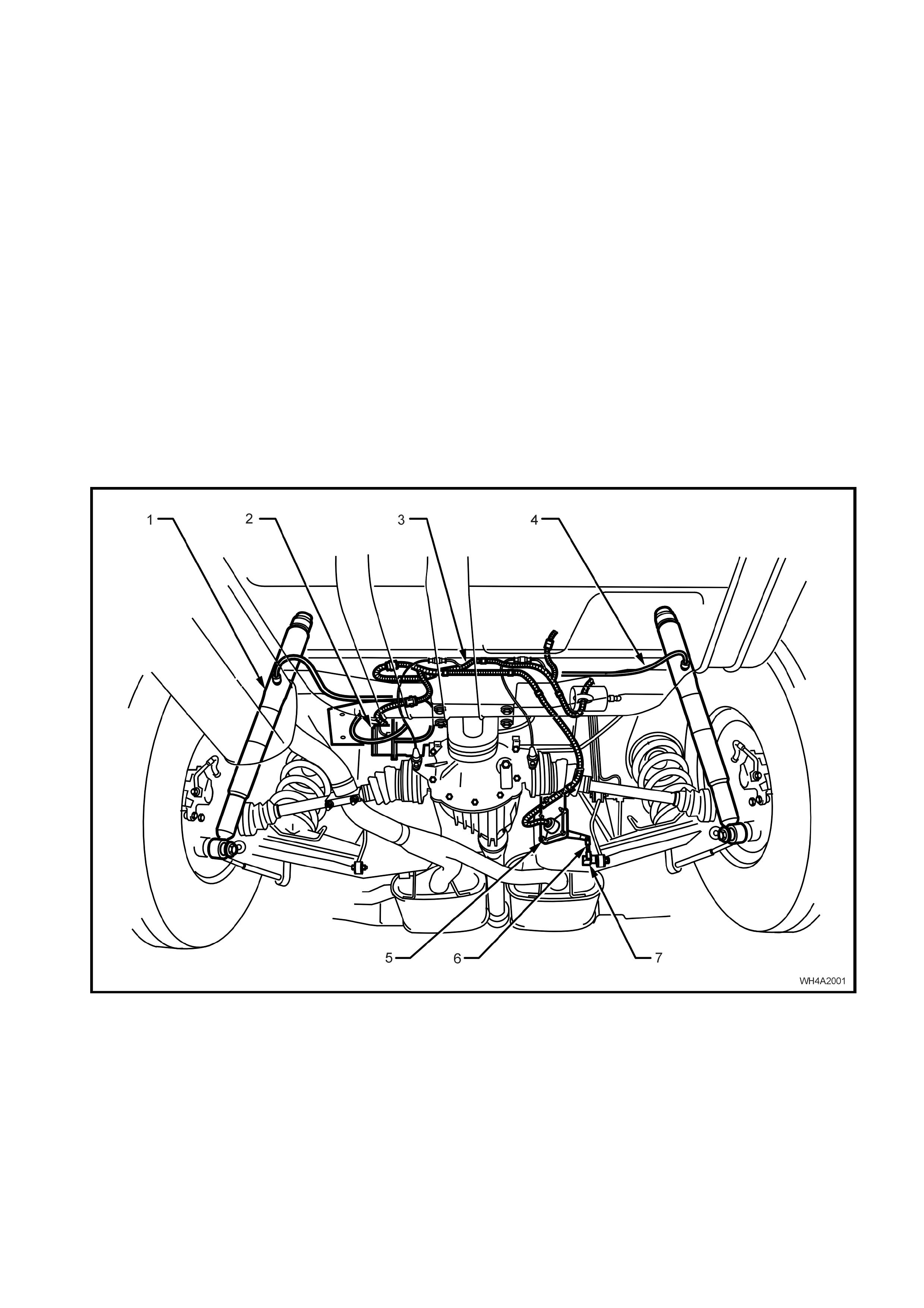
2. GENERAL DESCRIPTION
Automatic level ride is an electronically controlled system that maintains the vehicle at a constant trim height,
regardless of vehicle load. This feature uses a specifically designed electronic ride height sensor (5), fixed to the
rear crossmember on the right hand side. This sensor controls an electric motor driving a single cylinder air
compr ess or (2) and a n ex h aus t sol eno id v al ve. T he c ompress or (2) suppli es th e n ec es sary pressur e t o o per a te the
“Superlif t” shock absorber s (1) v ia “snap o n” air li nes (4) . The “Sup erlift” shock absorbers ass ist the rear s prings in
supporting the vehicle body under all loads.
The ride height sens or (5) has an integr ated electro nic controller that is pr ogramm ed to adjust the ride heig ht only
when necessary, ignoring sudden changes, as experienced on bumpy roads. The design of the system maintains
trim at all times when the ignition is on. As a safeguard to prevent the battery discharging, an electronic timer
switches off the compressor if it runs for a prolonged period (i.e. due to an air leak in the system).
The compressor assembly includes a maximum pressure release valve and an air drier. All air entering or
exhausting the system flows through the drier, which has an internal minimum retention valve preventing the air
bag, surrounding each shock absorber, from com pletely exhausting, indepen dent of the sensor controlled exhaust
valve.
Electric power to operate the system is supplied by an integrated wiring harness (3).
There are two main benefits resulting from the automatic level ride feature:
• Headlamp aim and rear view mirror adjustment being maintained independent of load.
• Rear tyre camber and toe-in are held to their optimum alignment to minimise tyre wear.
NOTE: If air pressure is lost from the system while the vehicle is in service (e.g. an air leak), the Superlift shock
absorber air bag wil l ver y pr obab ly be dam aged, re quir ing re plac ement.
1. Superlift Shock Absorbers 5. Ride Height Sensor
2. Air Compressor Assembly 6. Ride Height Sensor Connecting Link
3. Level Ride Wiring Harness 7. Ride Height Sensor Ball Stud Plate
4. Air Lines
Figure 4A-1