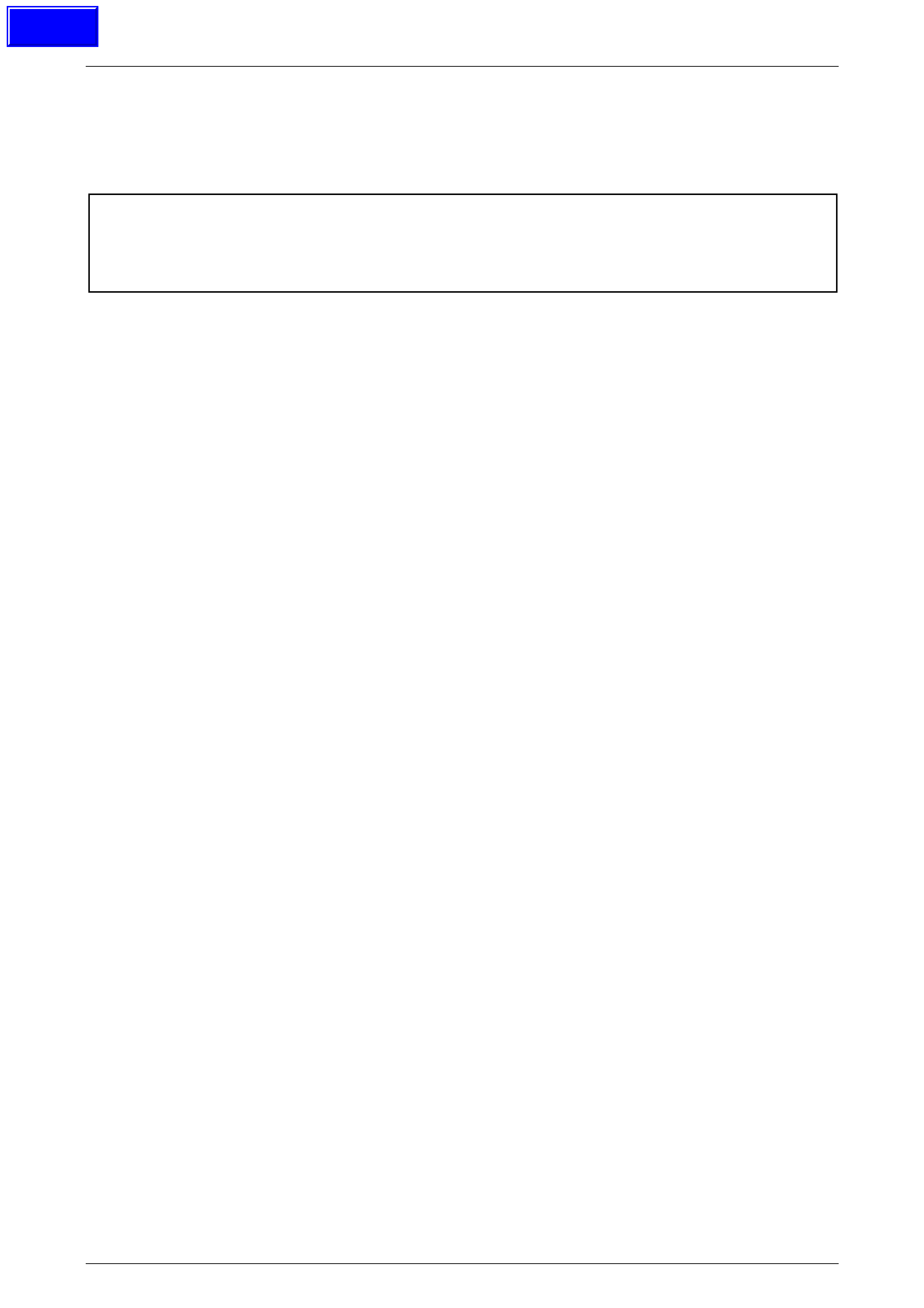
LPG System Page 8A2–1
Page 8A2–1
Section 8A2
LPG System
ATTENTION
Before performing any Service Operation or other procedure described in this Section, refer to Section 00
WARNINGS, CAUTIONS AND NOTES for correct workshop practices with regard to safety and/or property
damage.
1 General Information............................................................................................................................... 3
2 Service Operations................................................................................................................................5
2.1 Safety Precautions.................................................................................................................................................5
2.2 Service Lines..........................................................................................................................................................6
Front Service Line..................................................................................................................................................6
Remove..............................................................................................................................................................6
Reinstall..............................................................................................................................................................8
Intermediate Service Line......................................................................................................................................9
Remove..............................................................................................................................................................9
Reinstall............................................................................................................................................................11
2.3 Leak Testing .........................................................................................................................................................12
Gas Detectors.......................................................................................................................................................12
Combustible......................................................................................................................................................12
Foam ................................................................................................................................................................13
Leak Test Procedure............................................................................................................................................14
Leak Test Locations..........................................................................................................................................15
2.4 Fuel Mode Switch.................................................................................................................................................18
Remove .................................................................................................................................................................18
Reinstall ................................................................................................................................................................18
3 Diagnosis.............................................................................................................................................. 19
3.1 General Information.............................................................................................................................................19
3.2 Prerequisites to Diagnosis and Troubleshooting..............................................................................................20
Preliminary System Requirements.....................................................................................................................20
Safety Requirements............................................................................................................................................20
Checking Equipment ............................................................................................................................................20
3.3 LPG Vehicle Preliminary Diagnosis....................................................................................................................21
Test Description...................................................................................................................................................21
Test Procedure.................................................................................................................................................21
3.4 Vehicle Does Not Operate on LPG......................................................................................................................23
Test Description...................................................................................................................................................23
Test Procedure.................................................................................................................................................23
3.5 Fuel Mode Switch Does Not Operate..................................................................................................................25
Test Description...................................................................................................................................................25
Test Procedure.................................................................................................................................................25
3.6 Engine Does Not Crank .......................................................................................................................................27
Test Description...................................................................................................................................................27
Test Procedure.................................................................................................................................................27
3.7 Engine Cranks But Will Not Start on LPG..........................................................................................................28
Test 1 Description................................................................................................................................................28
Test Procedure.................................................................................................................................................28
Test 2 Description................................................................................................................................................30
Test Procedure.................................................................................................................................................30
Test 3 Description................................................................................................................................................32
Test Procedure.................................................................................................................................................32