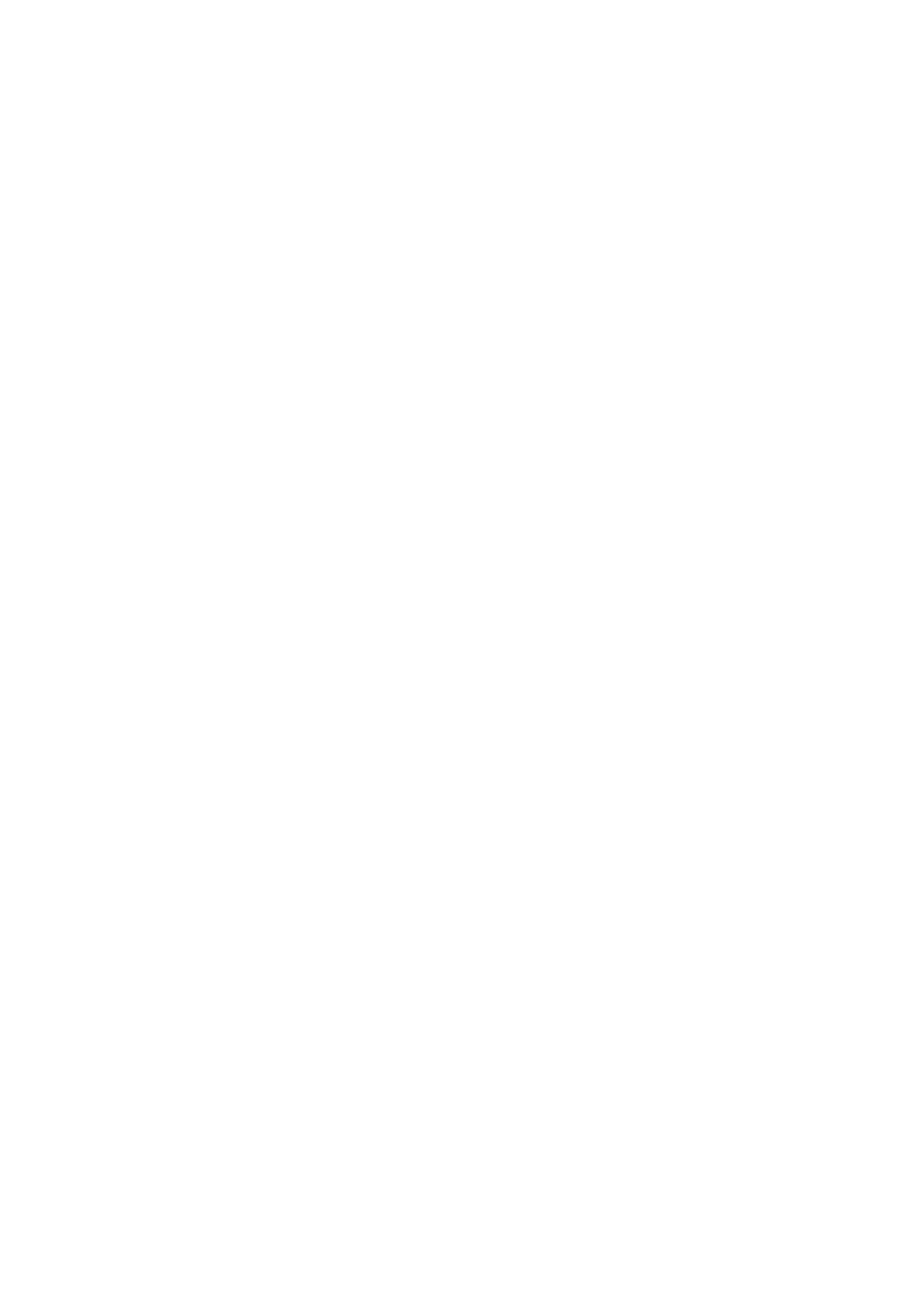
• The seat belt pretensioner is very hot immediately after activation. Wait for at least half an hour
for it to cool before proceeding work.
• As with many service procedures, gloves and safety glasses should be worn to prevent any
possible irritation of the skin or eyes.
WARNING:
• If a collision was light enough not to cause airbags to activate, inspect system parts and other
related parts according to instructions under 3.2 REPAIR AND INSPECTION REQUIRED AFTER AN
ACCIDENT in Section 10B.
• When servicing parts other than airbag system, if shocks may be applied to airbag system
component parts, remove those parts beforehand.
• When handling the airbag (inflator) modules, seat belt pretensioners or SDM, be careful not to
drop or apply an impact to it. If an excessive impact was applied, never attempt disassembly or
repair but replace it with a new one.
• If grease, cleaning agent, oil, water, etc. gets onto an airbag (inflator) module or seat belt
pretensioner, wipe it off immediately with a dry cloth.
• The airbag wire harness can be identified easily as it is covered with a yellow protection tube. Be
very careful when handling it.
• When an open in airbag wire harness, damaged wire harness, connector or terminal is found,
replace the wire harness, connectors and terminals as an assembly.
• Do not apply power to the airbag system unless all components are connected or a diagnostic
chart requests it, as this will set a diagnostic trouble code.
• Never use airbag system components from another vehicle.
• When electric welding, temporarily disable the airbag system, refer to
3.1 SERVICE PRECAUTIONS in Section 10B.
• Never expose the airbag system component parts directly to hot air (drying or baking the vehicle
after painting) or flames.
• WARNING/CAUTION labels are attached on each part of airbag system components. Follow the
instructions.
• After the vehicle is completely repaired, perform 2.4 AIRBAG DIAGNOSTIC SYSTEM CHECK in
Section 10B.
1.2 GENERAL PRECAUTIONS
The warnings and cautions below describe some of the general precautions that you should observe when
servicing a vehicle. These general precautions apply to many of the service procedures described in this
service information and will not necessarily be repeated with each procedure to which they apply.
WARNING:
• Whenever raising a vehicle for service, follow the instructions under 4. VEHICLE LIFTING POINTS
in this Section.
• When service work is required while the engine running, ensure the park ing brake is fully ON and
the transmission is in Neutral (manual transmission) or Park (automatic transmission). Keep
hands, hair, clothing, tools, etc. away from the fan and belts when the engine is running.
• When it is necessary to run the engine indoors, make sure that the exhaust gas is forced
outdoors.
• Do not perf orm service w ork in area s wh e re comb ust ible mat er ials can co me in contact wi th a hot
exhaust system.
• When working with toxic or flammable materials (such as gasoline and refrigerant), make sure that
the area the work is well-ventilated.
• To avoid burns, keep away from hot metal parts such as the radiator, exhaust manifold, tail pipe,
muffler, etc.
• New and used engine oil can be hazardous. Do not swallow oil or allow continuous contact with
the skin. Continuous contact with used engine oil has been found to cause [skin] cancer in
laborato ry animals. Brief contact with used oil may irr itate skin. To minimise your exposure, wear
a long-sleeve shirt and moisture-proof gloves when changing engine oil. If engine oil contacts
your skin, wash thoroughly with soap and water. Launder any clothing or rags if wet with oil.
• Keep oil filters away from children and pets. Recycle or properly dispose of used oil and filters
• Make sure the bonnet is fully closed and latched before driving. If it is not, it can open
unexpectedly during driving, obstructing your view and resulting in a collision.