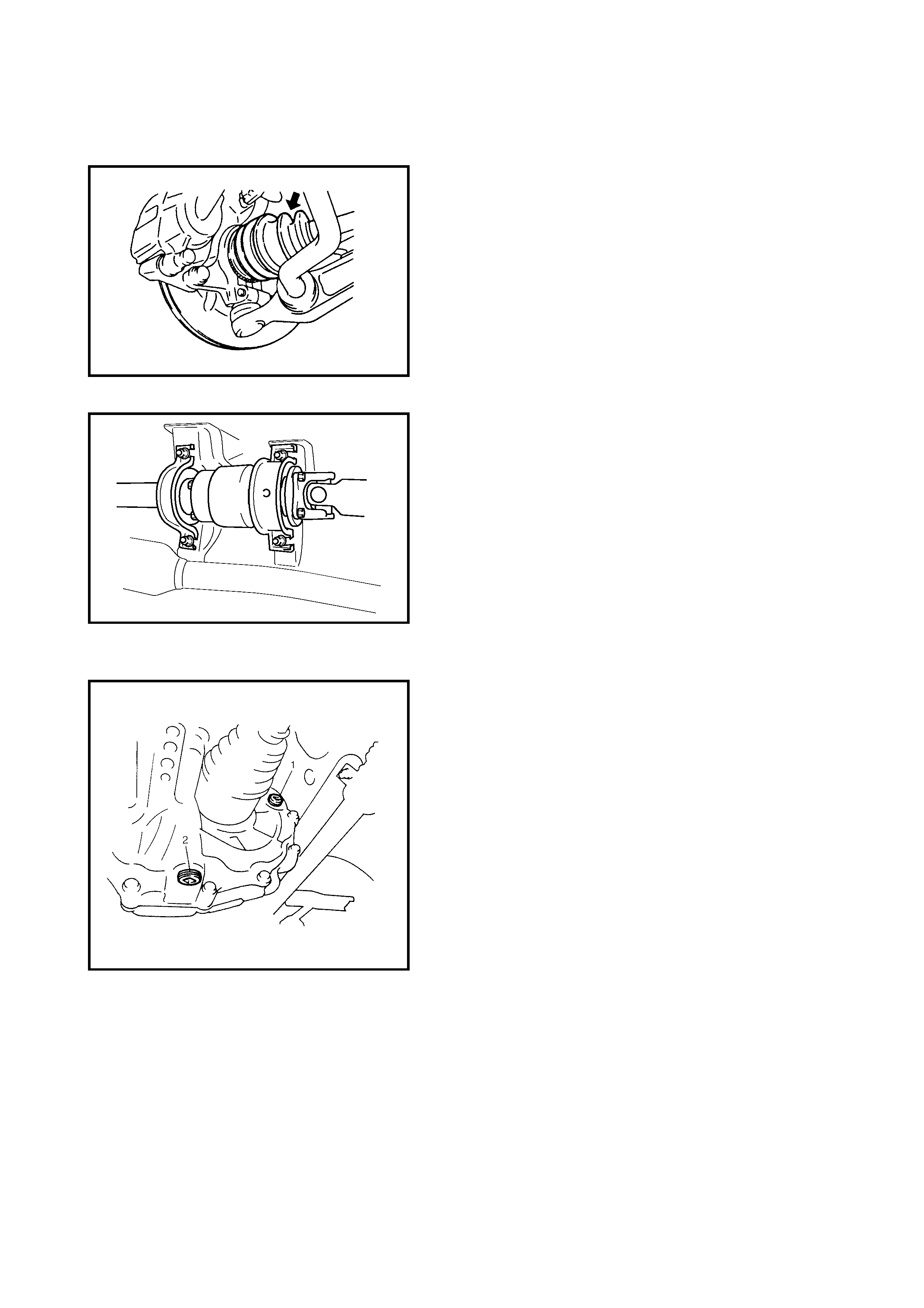
DRIVE SHAFT (AXLE) BOOTS / PROPELLER
SHAFTS
Drive Shaft (Axle) Boots Inspection
Check the drive shaft boots (wheel side and differential
side) for leaks, detachment, tear or other damage.
Replace boot as necessary.
Propeller Shaft Inspection
1. Check the propeller shaft connecting bolts for loose-
ness. If required, tighten to specified torque, refer to
Section 4B, PROPELLER SHAFTS.
2. Check the propeller shaft joints for wear, play and
damage.
If any defect is found, replace.
3. Check the propeller shaft centre support for intrusion of
foreign matter, cracks, abnormal noise and damage. If
any defect is found, replace.
MANUAL TRANSMISSION OIL
Inspection
1. Inspect the transmission case for evidence of oil
leakage. Repair any leaks as required.
2. Make sure that the vehicle is level.
3. Remove the transmission oil filler / level plug (1).
4. Check the oil level.
If oil flows out of the level plug hole or if it is level with
the hole, the oil level is correct.
If the oil level is insufficient, fill with specified oil up to
the level hole.
For the oil specifications, refer to Section 7A,
3.1 OIL CHANGE.
5. Apply sealant to filler/level plug and tighten it to
specified torque.
Replacement
1. Place the vehicle level and drain the oil by removing
the drain plug (2).
2. Apply se alant to drain pl ug after clean ing it a nd tighte n
drain plug to specified torque.
3. Pour specified oil up to level hole.
4. Tighten filler plug to specified torque.
For recommended oil, its amount and tightening torque
data, refer to Section 7A, 3.1 OIL CHANGE.