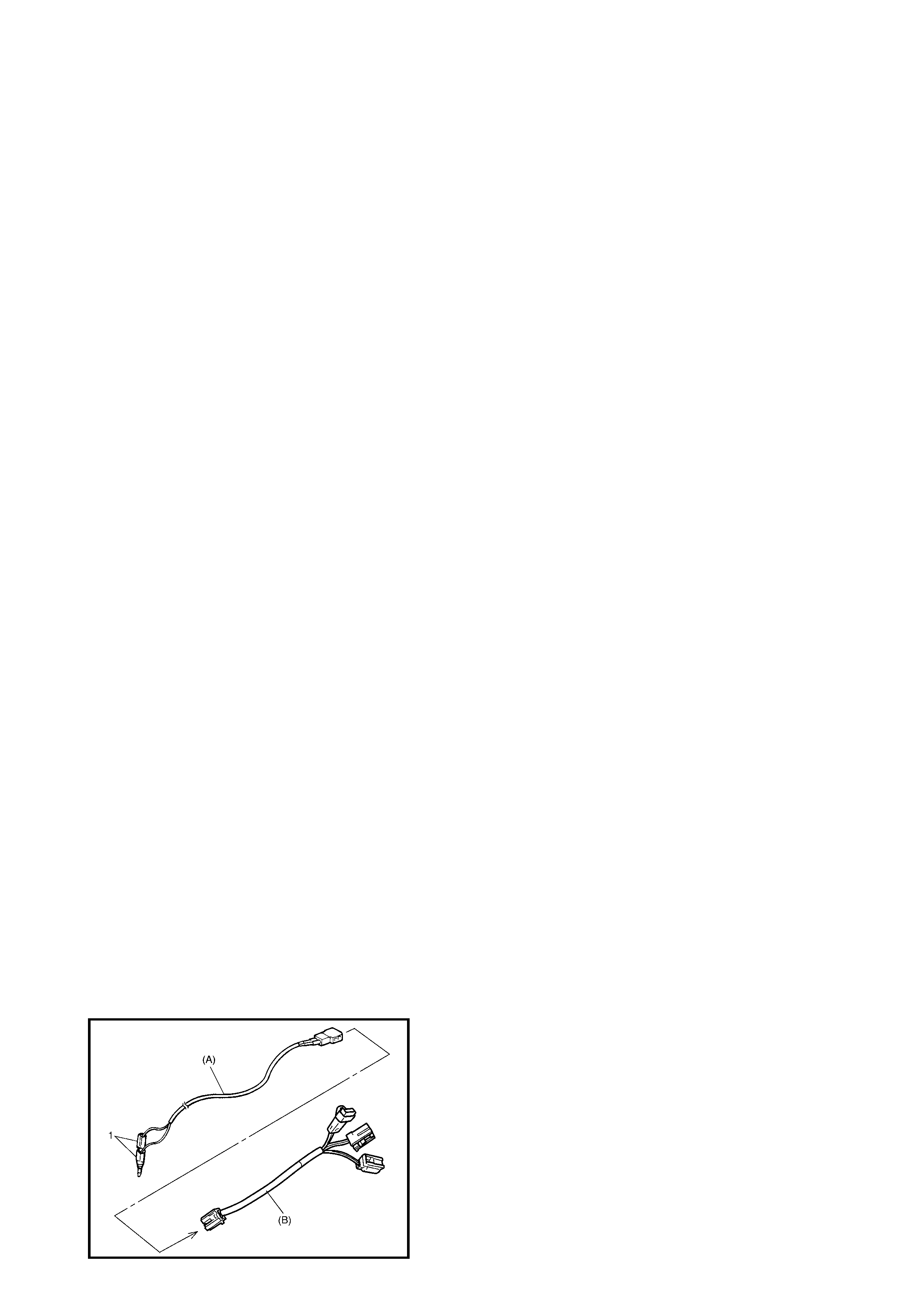
4. AIRBAG (INFLATOR) MODULE AND
SEAT BELT PRETENSIONER DISPOSAL
WARNING: Failure to follow proper airbag (inflator) module and seat belt pretensioner disposal proce-
dures can result in airbag deployment and pretensioner activation, which may cause personal injury.
Do not dispose of a live (undeployed) airbag (inflator) module and seat belt pretensione r.
An undeployed airbag (inflator) module / inactivated seat belt pretensioner must not be disposed of
through normal refuse channels. The undeployed airbag (inflator) module and inactivated seat belt
pretensioner contain substances that can cause severe illness or personal injury if the sealed con-
tainer is damaged during disposal.
An airbag (inflator) module or seat belt pretensioner can be deployed / activated inside or outside the vehicle.
The deployment / activation method used depends upon the final disposition of the vehicle. Review the follow-
ing instructions to determine which is best in a given situation.
Deployment / Activation Outside Vehicle:
When i t is intend ed to ret urn th e veh icle to serv ice, de ploy the ai rbag (i nflator) modu le(s) or acti vate the se at
belt pretensioner(s) outside the vehicle.
Deployment / Activation Inside Vehicle:
When the vehicle is to be destroyed, salvaged for component parts, deploy the airbag modules and/or acti-
vate the seat belt pretensioners installed in the vehicle.
WARNING: The follo wi ng pr ecaut ion s must be o bse rve d fo r th is wor k. F a ilure t o o bser ve a n y of th em
may result in personal injury.
• The procedure should be followed strictly as described here.
•Read 3.1 SERVICE PRECAUTIONS beforehand.
• To avoid accidental deployment, this work should be performed by no more than one person.
• Since smoke is produced when an airbag (inflator) module is deployed or a pretensioner is
activated, select a well-ventilated area.
• An airbag (inflator) module and seat belt pretensioner will immediately deploy / activate when a
12 volt power supply is connected to it. Wear safety glasses throughout this entire deployment /
activation and disposal procedure.
• Wear suitable ear protection when deploying an airbag or activating a pretensioner. Also, advise
those who are in the area close by to also wear suitable ear protection.
• Do not deploy or activate two or more airbag (inflator) modules or seat belt pretensioners at the
same time.
• Never connect a deployment harness to any 12 volt power source before connecting the deploy-
ment harness to the airbag (inflator) module and seat belt pretensioner. The deployment harness
shall remain shorted and not be connected to the 12 volt power source until the airbag or the pre-
tensioner is ready to be deployed or activated.
4.1 DEPLOYMENT / ACTIVATION OUTSIDE VEHICLE
When it is intended to return the vehicle to service,
deploy the airbag (inflator) module(s) or activate the
seat belt pretensioners(s) outside of t he vehicle.
1. Turn ignition switch to LOCK and remove the key.
2. Wear safety glasses during this deployment / activation
procedure.
3. Check that there is no open, short or damage in special
tools (A) 09932-75030 deployment harness and (B)
09932-78331 adaptor cable. If any fault is found, do
not use it.
NOTE: If a faulty seat belt pretensioner connector of the
adapter cable is found, replace it with a spare connector.
4. Short (1) the two deployment harness leads together
by fully seating one banana plug into the other.