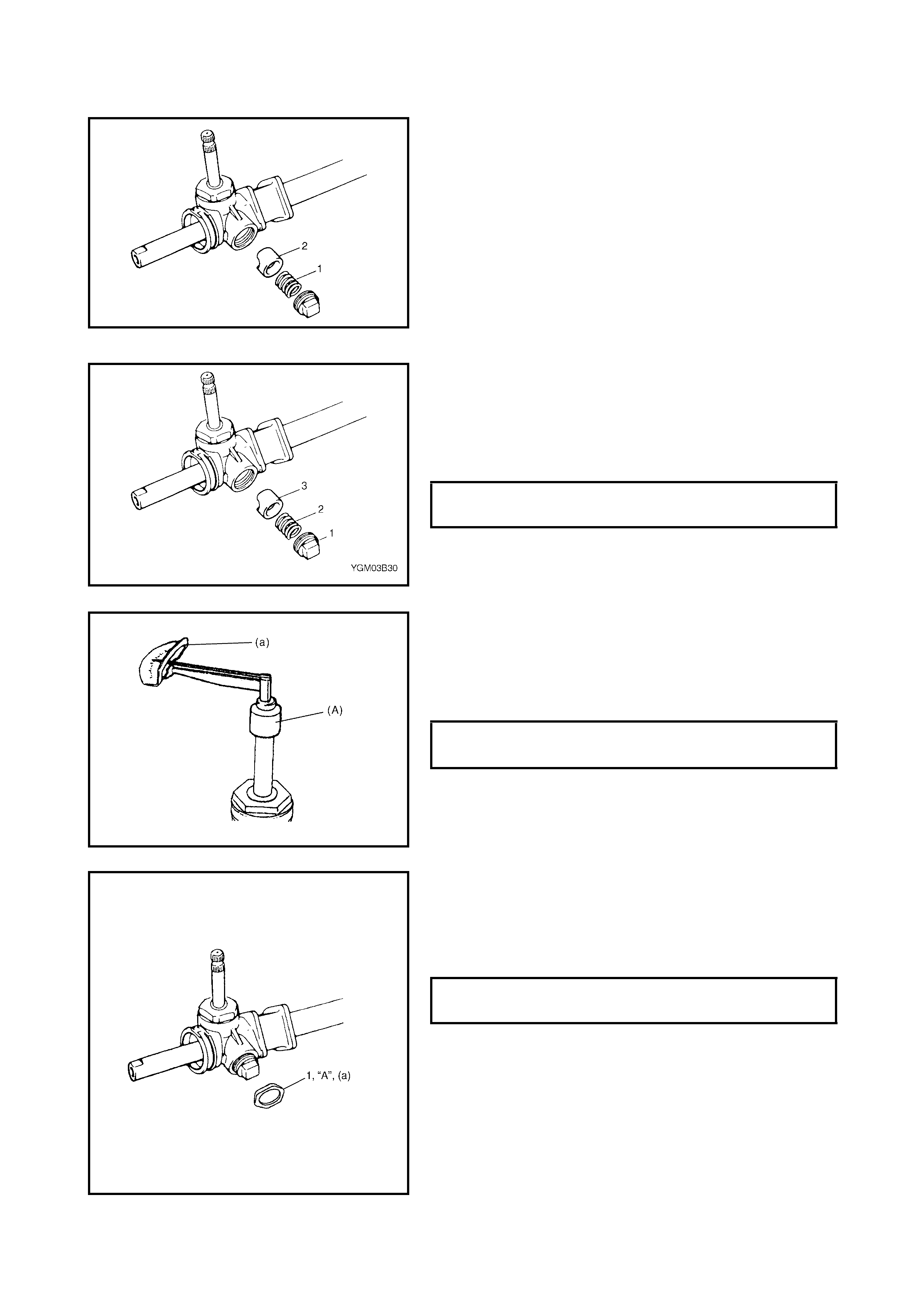
INSPECTION
• Inspect rack plunger (2) for wear or damage.
• Inspect rack plunger spring (1) for deterioration.
In either case, if found defective, replace.
INSTALLATION
1. Apply lithium grease lightly to sliding part of plunger
against rack.
2. Install rack plunger (3), rack plunger spring (2), rack
damper screw (1) to steering case in direction shown.
Tighten rack damper screw to specified torque.
3. After tightening rack damper screw to specified torque,
special tool 09944-18211, turn it back by 30° ~ 50° and
check for rotation torque of pinion. If it is not as
specified below, adjust so that it will be within specified
torque range.
Also, check if rack as a whole moves smoothly.
4. Apply watertight sealant “A” to thread part of rack
damper screw lock nut (1) and tighten it to specified
torque (a) by not turning damper screw position
adjusted in step 3.
“A”: Watertight sealant - Three Bond No.1207C
5. After adjustment, put rack damper screw cap as deeply
as possible.
6. Install rack boots and tie rods refer to 3.4 RACK BOOT/
TIE ROD INSTALLATION in this Section.
7. Install steering gear case, refer to 3.3 MANUAL RACK
AND PINION ASSEMBLY INSTALLATION in this
Section.
RACK DAMPER SCREW
TORQUE SPECIFICATION 12 Nm
ROTATION TORQUER OF PINION (a)
TO RQUE SPECIFICATION 0.4 - 1.1 Nm
RACK DAMPER SCREW LOCK NUT (a)
TORQUE SPECIFICATION 40 Nm