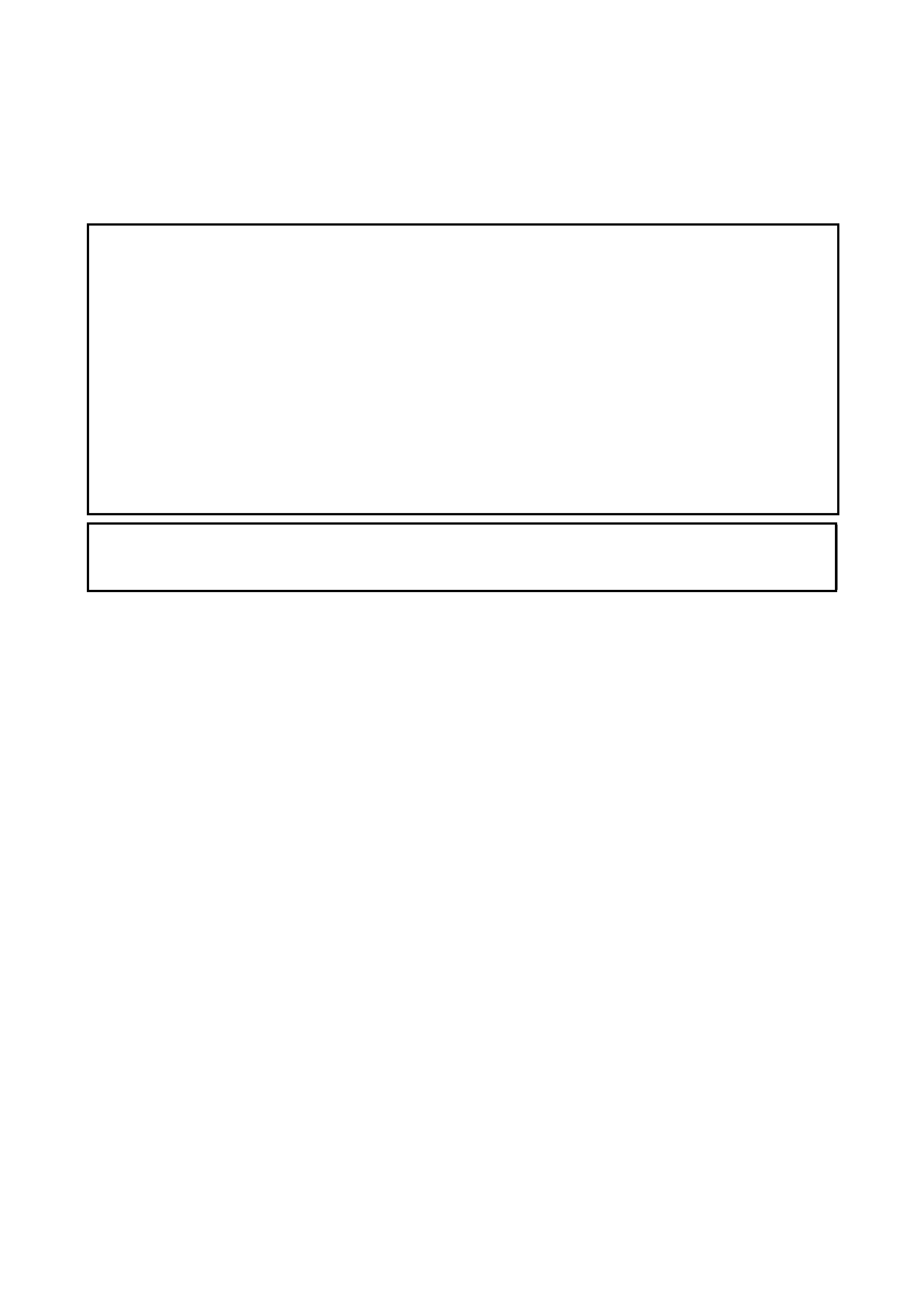
SECTION 3B1 - ELECTRICAL POWER
STEERING (P/S) SYSTEM
1. GENERAL DESCRIPTION
1.1 SYSTEM COMPONENTS
2. WIRING DIAGRAM
3. DIAGNOSIS
3.1 ON-BOARD DIAGNOSTIC SYSTEM
3.2 PRECAUTIONS IN DIAGNOSING
TROUBLES
3.3 SYSTEM CHECK FLOW TABLE
Customer Questionnaire Example
3.4 EPS WARNING LAMP CHECK
3.5 DTC CHECK
Using Tech 2
Not Using Tech 2
3.6 DTC CLEARANCE
Using Tech 2
Not Using Tech 2
3.7 SERIAL DATA LINK CIRCUIT CHECK
Diagnostic Flow Table
3.8 DTC TABLE
3.9 TABLE A - EPS WARNING LAMP DOES
NOT ILLUMINATE WITH IGNITION
SWITCH ON AND WITH ENGINE NOT
RUNNING
Circuit
Inspection
3.10 TABLE B - EPS WARNING LAMP
FLASHES WITH IGNITION SWITCH ON
Circuit
3.11 TABLE C - EPS WARNING LAMP DOES
NOT FLASH, REMAINS ON OR OFF,
EVEN WITH DIAGNOSIS SWITCH
TERMINAL GROUNDED
Circuit
3.12 DTC C1111 (DTC No.11) TORQUE
SENSOR MAIN CIRCUIT FAILURE
3.13 DTC C1113 (DTC No.13) TORQUE
SENSOR MAIN AND SUB CIRCUIT
FAILURE
3.14 DTC C1115 (DTC No.15) TORQUE
SENSOR SUB CIRCUIT FAILURE
3.15 DTC C1114 (DTC No.14) TORQUE
SENSOR 5V POWER SUPPLY CIRCUIT
FAILURE
3.16 DTC C1116 (DTC No.16) TORQUE
SENSOR 8V POWER SUPPLY CIRCUIT
FAILURE
3.17 DTC C1121/C1123/C1124
(DTC No.21/23/24) VSS CIRCUIT
FAILURE
3.18 DTC C1122 (DTC No.22) ENGINE SPEED
SIGNAL CIRCUIT FAILURE
3.19 DTC C1141/C1142/C1143/C1144/C1145
(DTC No.41/42/43/44/45) MOTOR
CIRCUIT FAILURE
3.20 DTC C1151 (DTC No.51) CLUTCH
CIRCUIT FAILURE
3.21 DTC C1153(DTC No.53) P/S CONTROL
MODULE POWER SUPPLY CIRCUIT
FAILURE
WARNING:
For vehicles equipped with Supplemental Restraint (Airbag) System:
• Service on and around the airbag system components or wiring must be performed only by an
authorised HOLDEN retailer. Refer to AIRBAG SYSTEM COMPONENTS AND WIRING LOCATION
VIEW under GENERAL DESCRIPTION in Section 10B AIRBAG SYSTEM in order to confirm
whether you are performing service on or near the airbag system components or wiring. Please
observe all WARNINGS and SERVICE PRECAUTIONS under ON-VEHICLE SERVICE in Section
10B AIRBAG SYSTEM before performing service on or around the airbag system components or
wiring. Failure to follow WARNINGS could result in unintentional activation of th e system or could
render the system inoperative. Either of these two conditions may result in severe injury.
• Technical service work must be started at least 90 seconds after the ignition switch is turned to
the “LOCK” position and the negative cable is disconnected from the battery. Otherwise, the sys-
tem may be activated by reserve energy in the Sensing and Diagnostic Module (SDM).
IMPORTANT:
Prior to connecting Tech 2 to the vehicle, ref e r to Section 0C TECH 2.