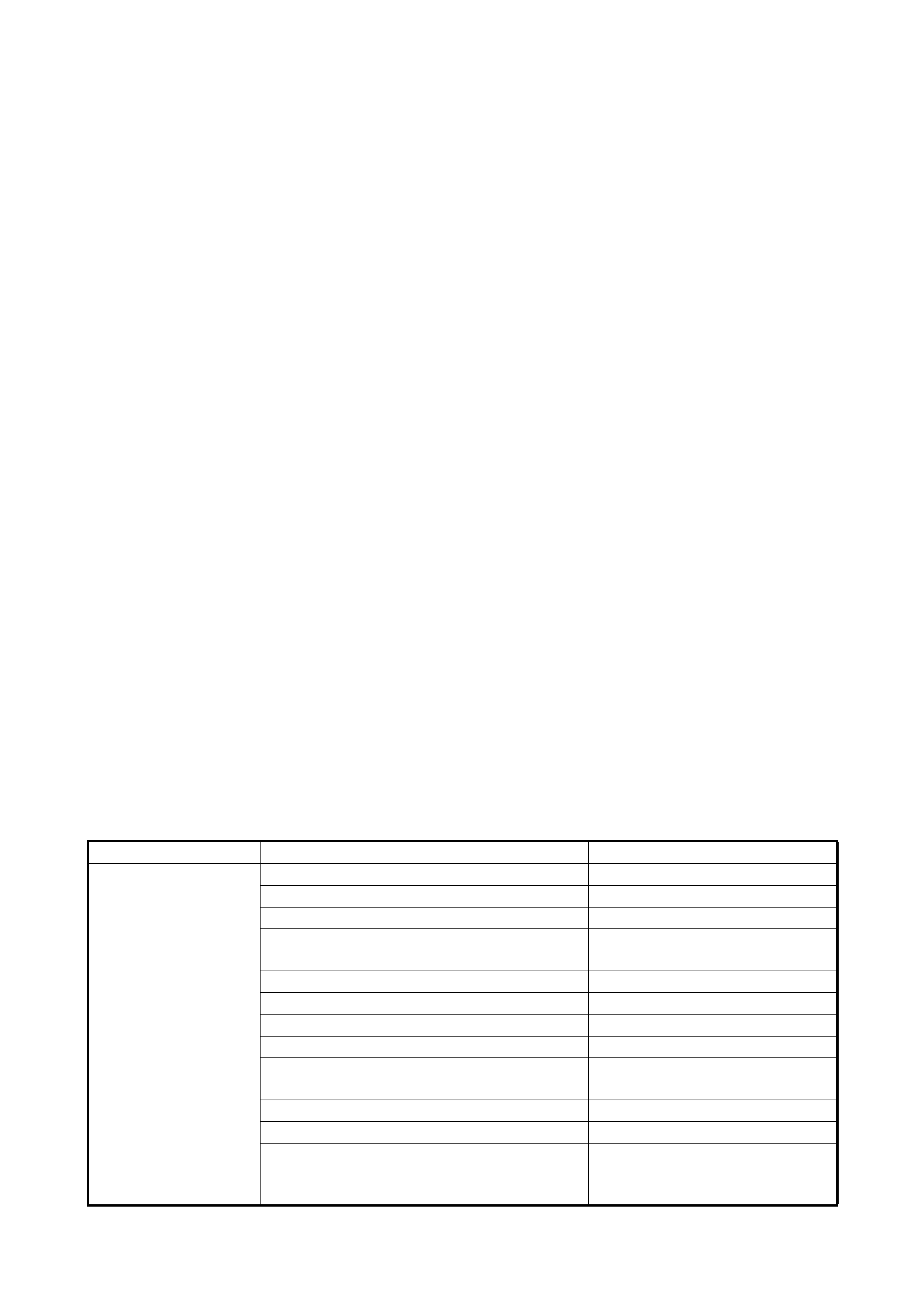
2. DIAGNOSIS
2.1 ROAD TES T ING BRAKES
The brak ing sy stem sho uld be tested on a dr y, cl ean, s mooth a nd level roadw ay which is not c rowned . Road
test brakes by making brake applications with both light and heavy pedal forces at various speeds to deter-
mine if the vehicle stops evenly and effectively. Drive the vehicle to see if it leads to one side or the other with-
out brake application. If it does, check the tyre pressure, front wheel alignment and front suspension
attachments for looseness. Refer to 2.4 DIAGNOSIS TABLE in this Section for other causes.
2.2 BRAKE FLUID LEAKS
Check the master cylinder fluid levels. A slight drop in reservoir level will result from normal lining wear, an
abnormally low level indicates a leak in the system. If a leak is indicated, check the entire brake system for
leaks. Even if there is evidence of a slight leak, the cause should be corrected and the defective parts
replaced.
2.3 SUBSTANDARD OR CONTAMINATED BRAKE FLUID
Incorrect brake fluid, mineral oil or water in the brake system fluid may cause the brake fluid to boil or the rub-
ber components in the hydraulic system to deteriorate.
Swelling of the master cylinder primary piston cups is a sign that the rubber parts have deteriorated. This
deterioration may also be evidenced by swollen wheel cylinder piston cups on the drum brake wheels.
If deterioration of rubber components is evident, disassemble all hydraulic parts and wash with alcohol. Dry
these parts with com pres sed air befo re ass embly to kee p alc ohol out of the sys tem. R eplac e all r ubber parts
in the system, including hoses. Also, when working on the brake mechanisms, check for fluid on the linings or
pads. If excessive fluid is found, replace the linings or pads.
If the master cylinder piston seals are satisfactory, check for leakage or signs that the brake system has over-
heated. If leakage is not found, drain fluid, flush with brake fluid, refill and bleed system.
The s ystem mus t b e flu sh ed i f the re is an y d oubt as to th e gr ade of flui d i n the sy stem or if the flu id has been
used which parts that may be contaminated.
2.4 DIAGNOSIS TABLE
Condition Possible Cause Correction
Not enough braking
force Brake fluid leakage from brake lines Locate leaking point and repair.
Overheated brakes Determine cause and repair.
Poor contact of shoes on brake drum Repair for proper contact.
Brake shoes linings stained with oil or wet with
water Repair leak and replace.
Badly worn brake linings Replace pads or shoes.
Defective wheel cylinders Repair or replace.
Malfunctioning caliper assembly Repair or replace.
Air in system Bleed system.
Incorrect sensor spring length of LSPV, if
equipped Check or adjust.
Broken sensor spring of LSPV, if equipped Replace.
Defective LSPV, if equipped Replace.
Malfunctioning ABS (Antilock brake system), if
equipped Check system and replace as nec-
essary, refer to Section 5E
ANTILOCK BRAKE SYSTEM.