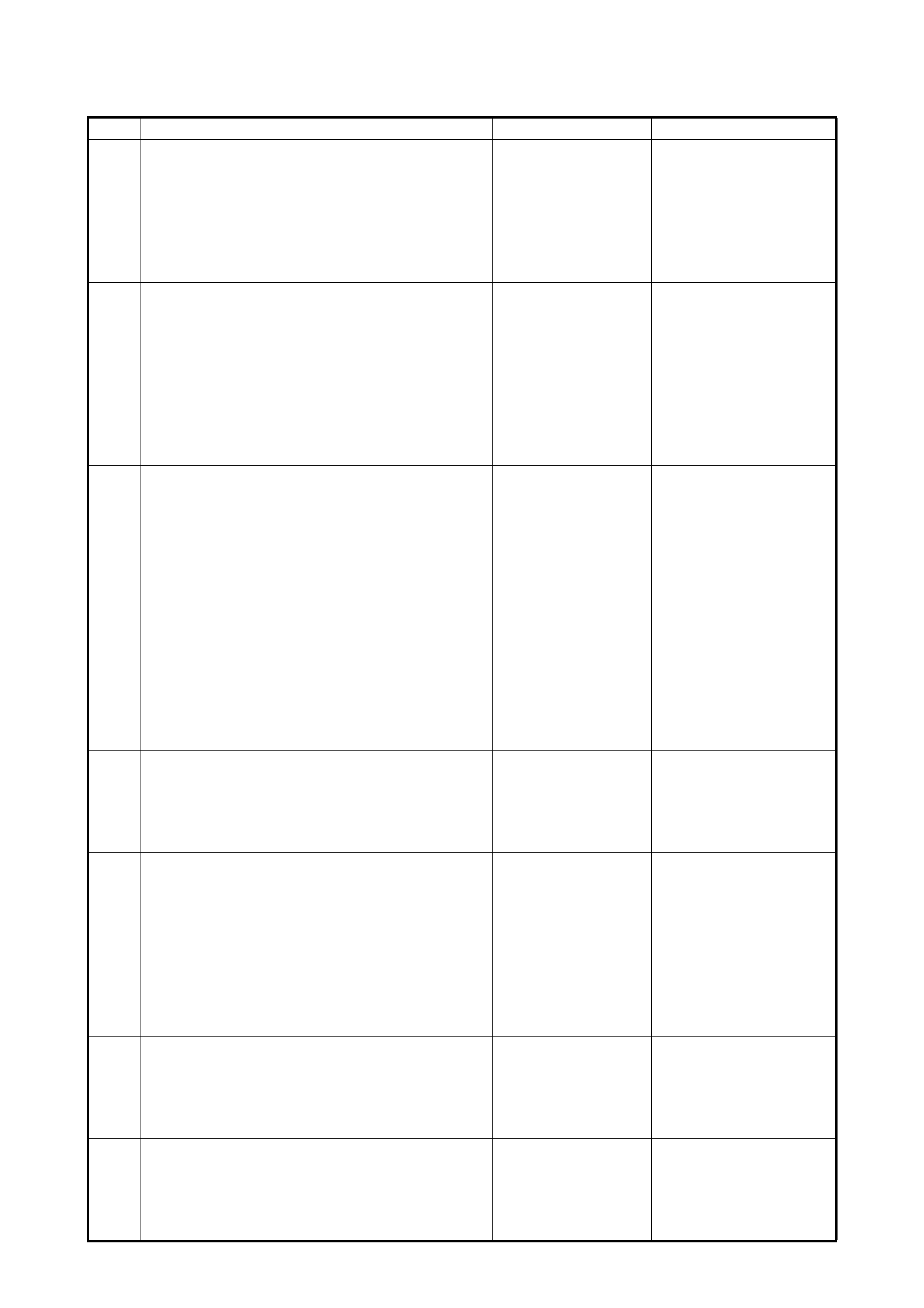
INSPECTION
Step Action Yes No
1 1. Disconnect applicable ABS wheel speed
sensor connector with ignition switch OFF.
2. Measure resistance between terminals of
ABS wheel speed sensor. Refer to FRONT
WHEEL SPEED SENSOR and/or REAR
WHEEL SPEED SENSOR in this Section.
Is measured resistance value as specified?
Go to Step 2. Replace ABS wheel
speed sensor assembly.
2 1. Turn ignition swi tc h OFF.
2. Disconnect ABS hydraulic unit/control
modu le con nector.
3. Check for proper connection to ABS control
module at each sensor terminal.
4. If OK, then turn ignition switch ON and
measure voltage between sensor terminal of
module connector and body ground.
Is it 0V?
Go to Step 3. ABS wheel speed sen-
sor circuit shorted to
power.
3 1. Turn ignition swi tc h OFF.
2. Connect ABS wheel speed sensor
connector.
3. Measure resistance between the following
points.
4. Both ABS hydraulic unit/control module
connector terminals of the corresponding
sensor.
This check result should be the same as
above Step 1.
5. Either terminal of wheel speed sensor
connector and body ground.
This check result should be no continuity.
Are both check results OK?
Go to Step 4. Circuit open or shorted to
ground.
4 1. Remove applicable ABS wheel speed
sensor.
2. Check sensor for damage or foreign material
attached.
Is it in good condition?
Go to Step 5. Clean, repair or replace.
5 1. Check front and/or rear sensor ring for the
following (remove rear axle shaft as
necessary):
2. Ring serration (teeth) neither missing nor
damaged.
3. No foreign material being attached.
4. Ring not eccen tric .
5. Wheel bearing free from excessive play.
Are they in good condition?
Go to Step 6. Clean, repair or replace.
6 1. Install ABS wheel speed sensor to knuckle.
2. Tighten sensor bolt to specified torque and
check that there is no clearance between
sensor and knuckle.
Is it OK?
Go to Step 7. Replace ABS wheel
speed sensor.
7 Referring to Reference of FRONT WHEEL
SPEED SENSOR and/or Reference of REAR
WHEEL SPEED SENSOR in this Section, check
output voltage or waveform.
Is specified voltage and/or waveform obtained?
Substitute a known
good ABS hydraulic
unit/control module
assembly and
recheck.
Replace se ns or and
recheck.