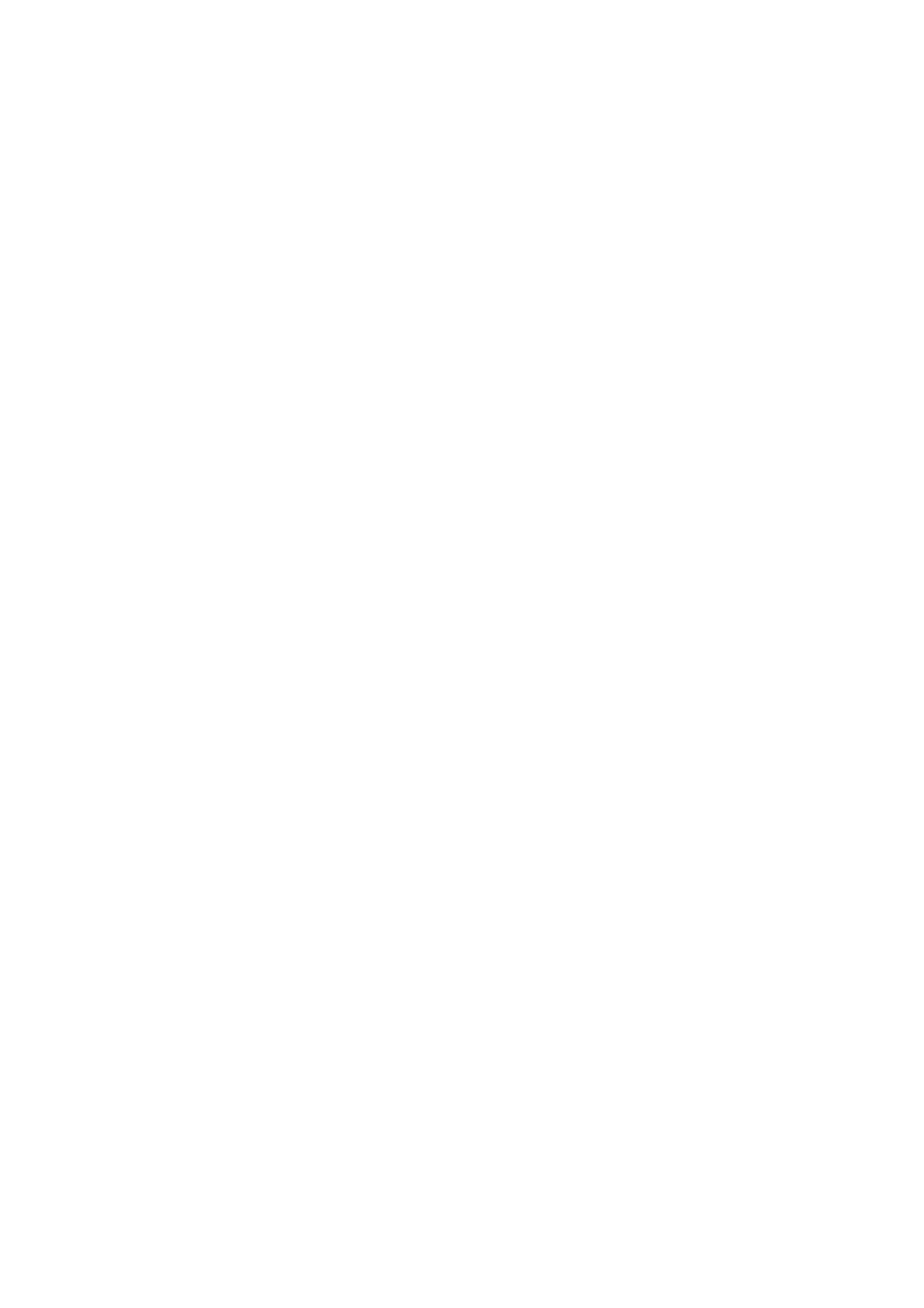
1. Customer Complaint Analysis
Recor d details of the problem (failure, compl aint) and how it oc curred as desc ribed by the custo mer. For this
purpose, use of an inspection form such as follows, will facilitate collecting information to the point required for
proper analysis and diagnosis.
2. DTC Check, Record and Clearance
First, check DTC, refer to DTC Che ck in 2.4 ENGINE DIAG NOSTIC FLOW TA BLE. If DTC is indicated, print
or write it down and then clear them by referring to DTC clearance section. DTC indicates malfunction that
occurred in the system but does not indicat e whether it exists now or it occurred in the past and the normal
condi tion has been resto red now. To ch eck which case appl ies, check the sy mptom in question according to
Step 4 and recheck DTC according to Step 5.
Attempt to diagnose a trouble based on DTC in this step only or failure to clear the DTC in this step will lead to
incorrect diagnosis, trouble diagnosis of a normal circuit or difficulty in troubleshooting.
3. and 4. Visual Inspection
As a preli minary step, per form a visua l check of the ite ms that suppor t proper function of the engine, re fer to
Visual Inspection in 2.4 ENGINE DIAGNOSTIC FLOW TABLE.
5. Trouble Symptom Confirmation
Based on information obtained in Step 1 Customer Complaint Analysis and Step 2 DTC Check, confirm
trouble symptoms. Also, reconfirm DTC according to DTC Confirmation Procedure described in each DTC
Diagnosis Section.
6. and 7. Rechecking and Record of DTC
Refer to DTC Check in 2.4 ENGINE DIAGNOSTIC FLOW TABLE for checking procedure.
8. Engine Basic Inspection and Engine Diagnosis Table
Perform basic engine check according to the Engine Basic Inspection Flow Table in
2.4 ENGINE DIAGNOSTIC FLOW TABLE first. When th e end of the flow table has been rea ched, ch eck the
parts of the system suspected as a possible cause, refer to Engine Diagnosis Table in
2.4 ENGINE DIAGNOSTIC FLOW TABLE and based on symptoms appearing on the vehicle (symptoms
obtained through steps of customer complaint analysis, trouble symptom confirmation and/or basic engine
check) and repair or replace faulty parts, if any.
9. Troubleshooting for DTC (See each DTC Diag. Table)
Based on the DTC indicate d in Step 5 and refe rring to the applica ble DTC Diag . Table in th is Section , locate
the cause of the trouble, namely in a sensor, switch, wire harness, connector, actuator, ECM or other part and
repair or replace faulty parts.
10. Check for Intermitt e nt Problem
Check parts where an intermittent trouble is easy to occur (e.g., wire harness, connector , etc.), refer to
1.7 ELECTRICAL CIRCUIT INSPECTION PROCEDURE - INTERMITTENT AND POOR CONNECTION in
Section 0A and related circuit of DTC recorded in Step 2.
11. Final Confirmati on Test
Confirm that the problem symptom has gone and the engine is free from any abnormal conditions. If what has
been repaired is related to the DTC, clear the DTC once, perform DTC confirmation procedure and confirm
that no DTC is indicated.