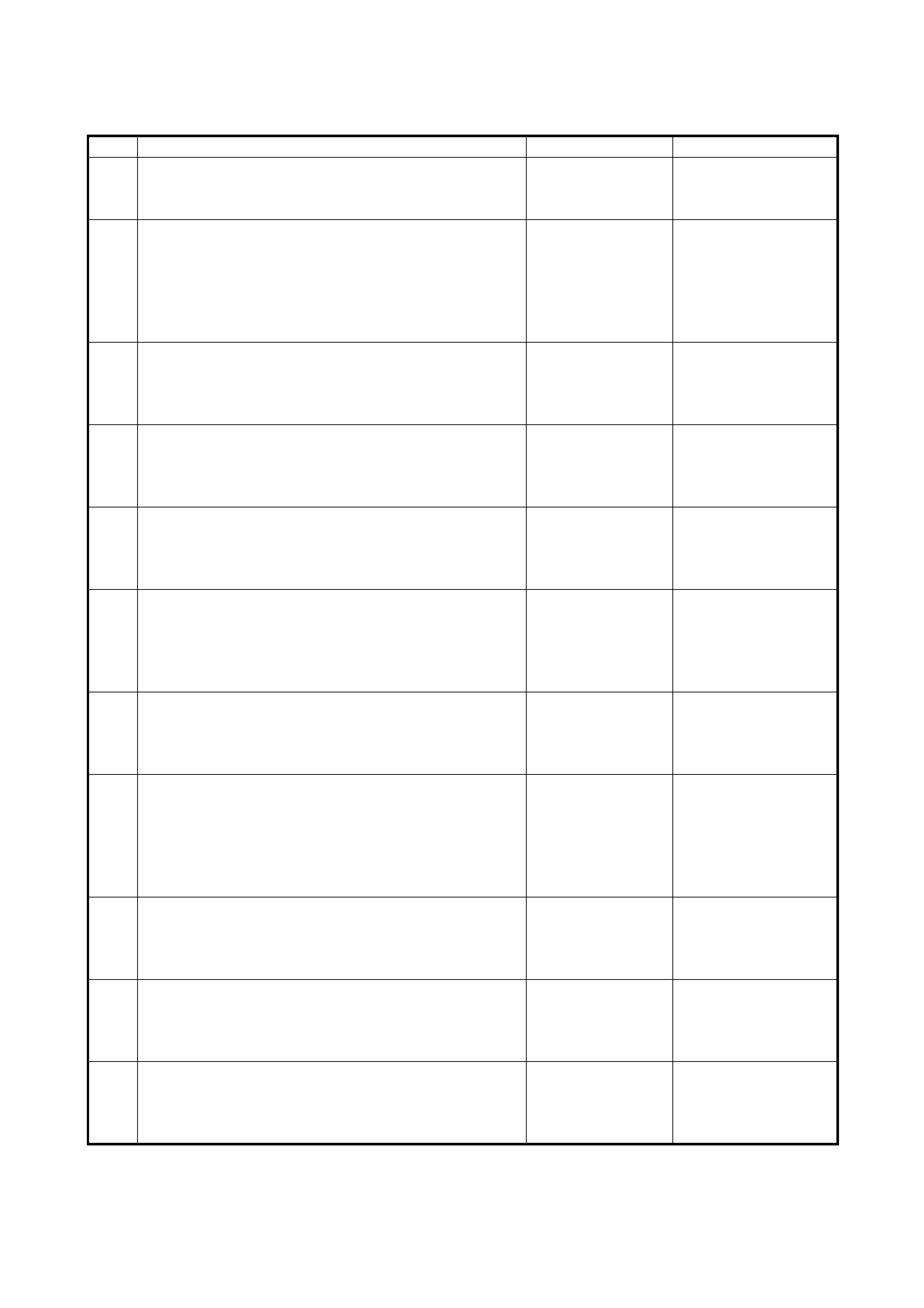
2.2 IGNITION SYSTEM DIAGN OSTIC FLOW TABLE
Step Action Yes No
1 Were the steps in Section 6 2.4 ENGINE DIAGNOSTIC
FLOW TABLE performed? Go to Step 2. Go to Section 6, 2.4
ENGINE DIAGNOS-
TIC FLOW TABLE.
2 Ignition Spark Test
Check all spark plugs for condition and type, refer to 3.3
SPARK PLUGS in this Section.
If OK, perform ignition spark test, refer to 3.1 IGNITION
SPARK TEST in this Section.
Is spark emitted from all spark plugs?
Go to Step 11. Go to Step 3.
3 Diagnostic Trouble Code (DTC) Check Is DTC stored in
ECM? Go to the applica-
ble DTC DIAGNOS-
TIC FLOW TABLE
in Section 6.
Go to Step 4.
4 Electrical Connection Check
Check ignition coil assemblies and high-tension leads
for electrical connection.
Are they connected securely?
Go to Step 5. Connect securely.
5 High-ten sion Lea ds Check
Check high-tension leads for resistance refer to 3.2
High-Tension Leads in this Section.
Is check result satisfactory?
Go to Step 6. Replace high-tension
lead(s).
6 Ignition Coil Assembly Power Supply and Ground Cir-
cuit Check
Check ignition coil assembly power supply and ground
circuits for open and short.
Are circuits in good condition?
Go to Step 7. Repair or replace.
7 Ignition Coil Assembly Check
Check ignition coil for resistance refer, to 3.4 IGNITION
COIL ASSE MB LY in th is Sec tion.
Is check result satisfactory?
Go to Step 8. Replace ignition coil
assembly.
8 Crankshaft Position (CKP) Sensor Check
Check crankshaft position sensor, refer to Step 3 and 4,
Section 6, 2.20 DTC P0335 (No.23) CRANKSHAFT
POSITION SENSOR (CKP) CIRCUIT MALFUNCTION,
flow table.
Is check result satisfactory?
Go to Step 9. Tighten CKP sensor
bolt, replace CKP sen-
sor or CKP sensor
plate.
9 Ignition Trigger Signal Circuit Chec k
Check ignition trigger signal wire for open, short and
poor connection.
Is circuit in good conditi on?
Go to Step 10. Repair or replace.
10 A Known-good Ignition Coil Assembly Substitution
Substitute a known-good ignition coil assembly and
then repeat Step 2.
Is check result of Step 2 satisfactory?
Go to Step 11. Substitute a known-
good ECM and then
repeat Step 2.
11 Ignition Timing Check
Check initial ignition timing and ignition timing advance,
refer to 3.7 IGNITION TIMING in this Section.
Is check result satisfactory?
System is in good
condition. Check CKP sensor,
CKP sensor plate and
input signals related to
this system.