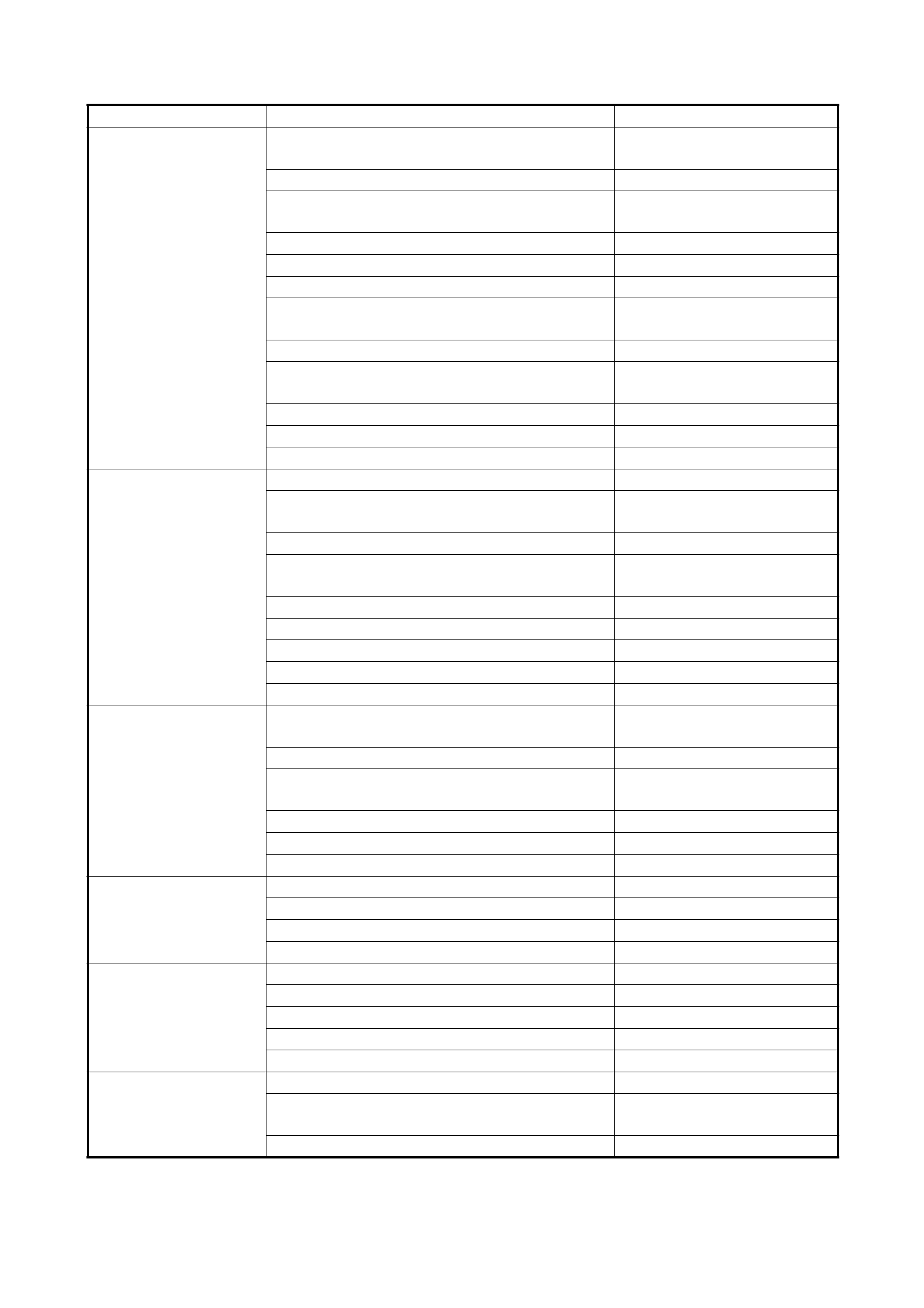
Con diti on Po ssi ble Cause Corre ct ion
Motor no t ru nning
(N o operating so und
from m agnetic sw itch)
Shift lev er switch is not in P or N, or not adjusted
(A/T) Shift in P or N, or adjust switch.
Batter y run down Recharge battery.
Batter y voltage too low due t o batter y
deterioration Replace battery.
Poo r contact in batter y terminal connect ion Retighten or replace.
Loose grounding cable connection Retighten.
Fuse loose or blown Tighten or replace.
Poor contacting action of ignition s witch and
magnetic switch Replace.
Lead wire connector loose Retighten.
Open-circuit between ignition swi tch and mag-
netic switch Repair.
Open-circuit in pull-in coil Replace magnetic switch.
Brushes are seating poorly or worn down Repair or replace.
Poo r sliding of plunger and/or pinion Repair.
Motor no t ru nning
(Op erating so und f rom
ma gnetic switch
heard)
Batter y run down Recharge battery.
Batter y voltage too low due t o batter y deter iora-
tion Replac e battery.
Loose batter y c able connections Retighten.
Burn t main contact point, or p oor contact ing
action of magnetic switc h Replace magnetic switch.
Brushes are seating poorly or worn down Repair or replace.
Weakened brush spring Replace.
Burn t commutator Replace arm at ure.
Layer short-circuit of arm atu re Replace.
Crankshaft rotation obstructed Repair.
Starting motor running
but too slow ( sm al l
torque) (If battery and
wir ing are satisfac-
tory, inspect starting
motor)
Insufficient contact of magnetic sw itch main con-
tacts Replace magnetic switch.
Layer short-circuit of arm atu re Replace.
Disconnected, burn t or worn commutator Repair commutator or replace
armature.
Worn brushes Replace brush.
Weakened brush springs Replace spring.
Burn t or abnor m ally worn end bush Repla ce bu sh .
Starting motor run-
ning, but no t cra nki ng
engine
Worn pinion tip Replace over-running clutch.
Poo r sliding of over-r unning clutch Repair.
Over-running clutch slipping Replace over-running clutch.
Worn teeth of ring gear Replace flywheel .
Noise Abnormally worn bush Replace bush.
Worn pinion or worn teeth of ring gear Replace pinion or flywheel.
Poo r sliding of pinion (failure in return movement) Repair or replace.
Worn internal or planetary gear teeth Replace.
Lack of oil in each par t Lubr icate.
Starting motor does
not s top runn in g Fused contact points of magnet ic switch Replace magnetic switch.
Shor t -circu it between turns of magnet ic switch
coil (layer s hort-circuit) Replace magnetic switch.
Failure of returning action in ignition switch Replace.