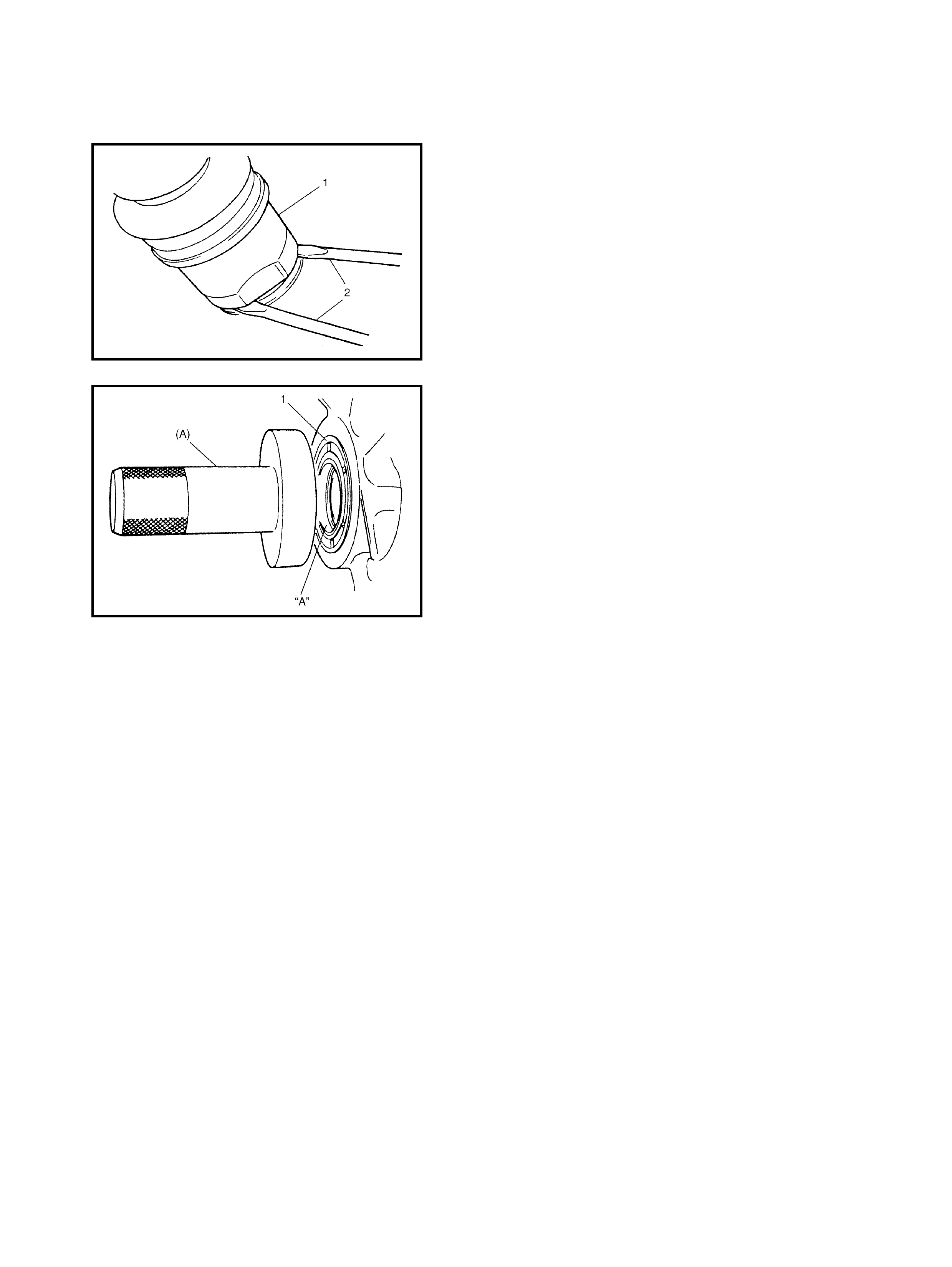
5. Remove the ball joint bolt and then separate the sus-
pension arm from the knuckle.
6. Separate the transfer from the transaxle assembly,
refer to Section 7D, 4.1 TRANSFER UNIT.
7. Remove the drive shaft joint (1) using two large size
screwdrivers (2), to release the snap ring fitting of the
joint spline at the differential side. Pushing the knuckle
portion outward, detach the drive shaft at the differen-
tial side.
8. Remove the oil seal (1).
9. Using special tool 09913-75510 (A) for left or right
hand and a hammer, install a new oil seal until it
becomes flush with the case surface.
NOTE: When installing the oil seal, face the spring side
inward.
10. Apply grease “A” to the oil seal lip. Check the drive
shaft for smoothness where the oil seal contacts.
“A”: Lithium grease
11. Insert the transfer into the transaxle, refer to
Section 7D, 4.6 TRANSFER UNIT.
12. Insert the drive shaft joint into the differential gear.
CAUTION:
• Be careful not to scratch the oil seal lip while inserting
the drive shaft joint.
• Make sure to seat the snap ring when inserting the
drive shaft joint fully.
• Only use your hands when inserting the joint boot as a
hammer will cause damage.
13. Connect the ball joint with the knuckle and fasten with a
bolt, to specification, refer to Section 3D, 3.3 WHEEL
HUB AND STEERING KNUCKLE.
14. Connect the tie-rod end with the knuckle and fasten
with a new nut, to the specified torque, refer to Section
3D, 3.3 WHEEL HUB AND STEERING KNUCKLE.
15. Install the stab iliser mounti ng brackets, an d fasten the
bolts to the specified torque, refer to Section 3D,
3.2 STABILISER BAR AND/OR BUSHINGS.
16. Replenish the transaxle oil and transfer oil as specified,
refer to 3.1 OIL CHANGE in this Section, then check
the oil seal for leakage.