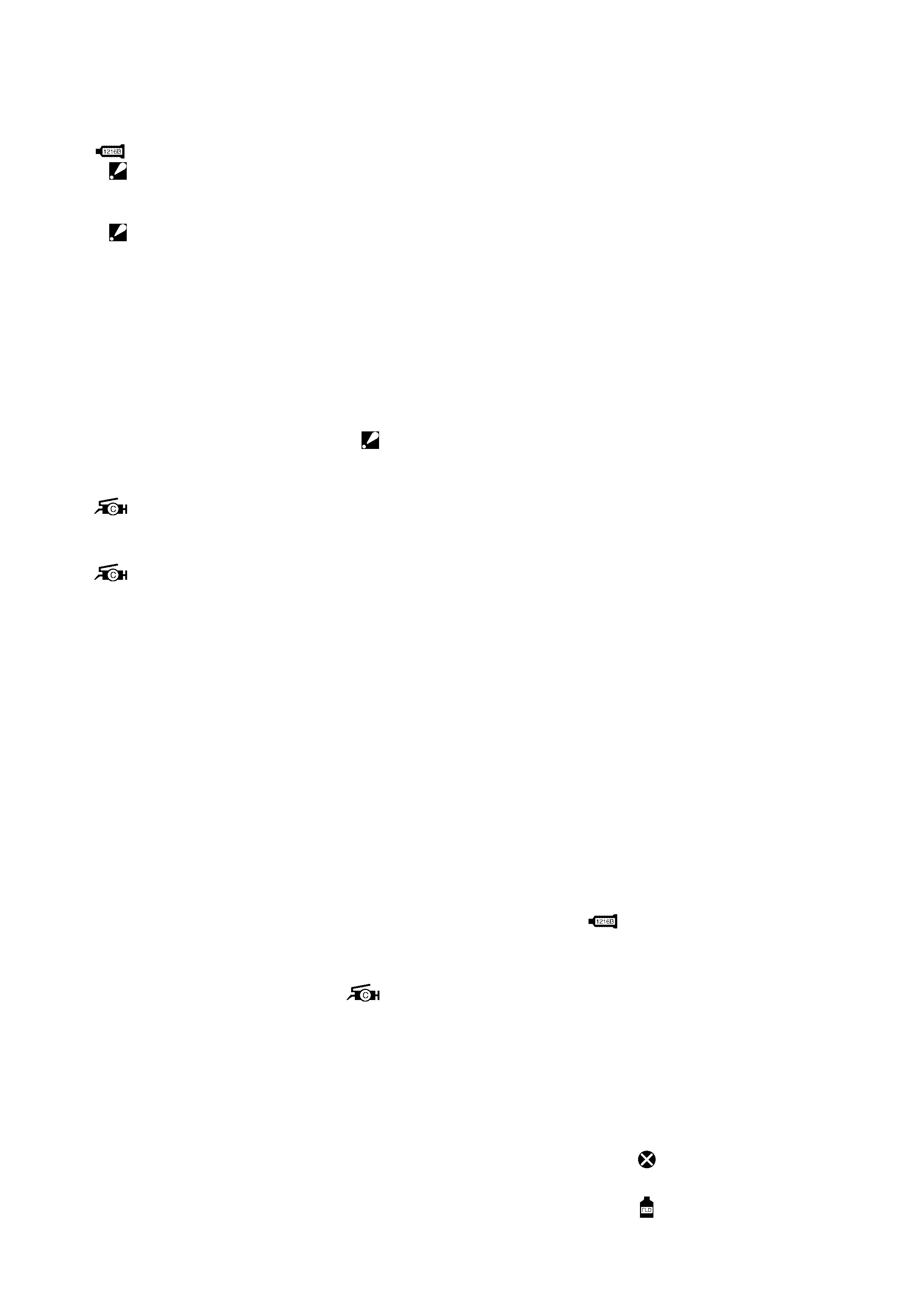
Legend
1. Torque converter 38. Cooler check valve 67. 2nd brak e separator
plate
2. Torque converte r housing
: Apply se alant Three Bond
No. 1216B to m ating
surface to transaxle case.
39. Spring
40. Transaxle case plug 68. 2nd brake return spring
subassembly
41. Fluid filler tube
42. Fluid level gauge 69. Front sun gear thrust
bearing race
3. Oil strain er assem bly
: Replace oil strainer
when overhauling.
43. Fluid cooler inlet pipe
44. Fluid cooler outlet pipe 70. Front planetary sun gear
45. 2nd brak e gas ket 71. Plan et ary gea r thrust
bearing
4. Parking lock pawl shaft 46. Brake drum gasket
5. Parking lock pawl 47. Fluid outlet union 72. One-way clutch No.1
assembly
6. Parking lock pawl return
spring 48. Reduction drive gear
nut
: After tightening nut so
as rotational torque of
reduction drive gear to
be in specified value,
caulk nut securely.
73. Rear planetary sun gear
subassembly
7. Parking lock pawl rod
8. Parking lock pawl bracket 74. Rear sun gear thrust
bearing race
9. Manual dete nt spring
10. Manual valve lever 75. Rear sun gear thrust
bearing
11. Manual valve lever pin
12. Manual shift shaft 49. Reduction drive gear 76. Forward clutch hub
13. Manual shift shaft oil seal
: Apply Lithium grease to oil
seal lip.
50. Planetary ring gear
subassembly 77. Intermediate shaft thrust
bearing race
51. Breather hose 78. Intermediate sh aft thrust
bearing
14. Differential sid e oil se al
: Apply Lithium grease to oil
seal lip.
52. Breather union
53. Input shaft speed
sensor 79. 2nd brake piston
snap ring
15. Torque converter
housing plug 54. Valve body harness 80. O/D and 2nd coast brake
retaining plate snap ring
55. 1st and reverse brake
piston
16. Lubrication LH tube 81. O/D and 2nd coast brake
reta ini ng pla te
17. Lubrica tion RH tube 56. O-ring
18. Fluid reservoir RH plate 57. 1st and reverse brake
return spring
subassembly
82. O/D and 2nd coast brake
disc
19. Input shaft front thrust
bearing 83. O/D and 2nd coast brake
separator pl ate
20. Input shaft rear thrust
bearing 58. 1st and reverse brake
disc 84. O/D and 2nd coast brake
rear plate
21. Input shaft rear thrust
bearing race 59. 1st and reverse brake
sepa rator plate 85. Rear cover seal ring
22. Direct clutch hub 60. 1st and reverse brake
retaining plate 86. Reverse clutch drum
thrust bearing
23. Lubrication tube clamp
24. Fluid reservoir LH plate 61. 1st and reve rse brake
snap ring 87. Rear cover plug
25. Governor apply
No.2 gasket 88. Transaxle rear cover
Apply sealant Th ree Bond
No. 1216B to
mating surface.
62. Planetary gear
assembly
26. Automatic transaxle case
27. Accumulator piston
O-ring 63. Planetary carrier thrust
washer
: Apply Lithium grease to
slide con tact face.
89. Harness bracket
90. Select cable clam p
28. Accumulator spring 91. Governor apply No.1
gasket
29. C2 accumulator piston
30. C1 accumulator piston 92. O utput shaft speed
sensor (VSS)
31. B1 accumulator piston 64. One-way clutch No.2
assembly
32. Oil pan gasket 93. O ne-way clutch outer
race retainer
33. Oil pan 65. 2nd brake ret a ining
plate
34. A/T fluid drain plug Do not reuse.
35. Manual select leve r
36. Lock washer 66. 2nd brake disc
plate Apply automatic
transa xle fluid.
37. Transm is si on rang e
sensor