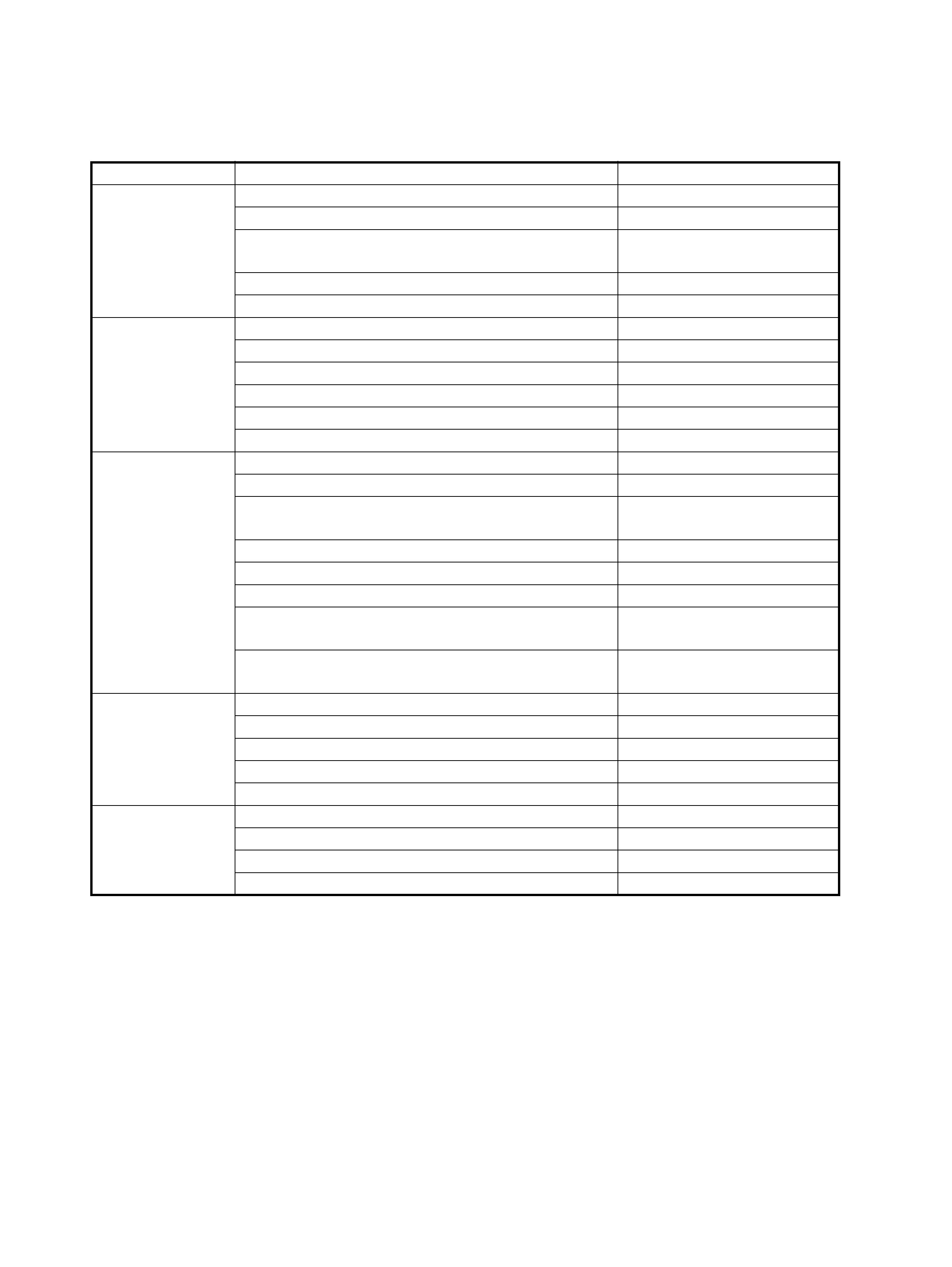
2. DIAGNOSIS
Condition Possible Cause Correction
Slipping Incorrect clutch pedal free travel Adjust free travel.
Worn or oily clutch disc facing Replace disc.
Wa rped disc, pressure plate or flywheel surface Re place disc, clutch cover o r
flywheel.
Weakened diaphragm spring Replace clutch cov er.
Rusted clutch cable Replace cable.
Dragging clutch Incorrect clutch pedal free travel Adjust free tra vel.
Weakened diaphragm spring, or worn spring tip Replace clutch cover.
Rusted input shaft splines Lubricate.
Damaged or worn splin es of tra nsaxle input shaft Re place input shaft.
Wa rped c lutch disc Replace disc .
Clutch fac ings broken or dirty with oil Re place disc.
Clutch vibration Glazed (glass-like) clutch fa cings Repair or replace disc.
Clutch fac ings dirty with oil Re place disc.
Release bearing binds on input shaft bearing
retainer Lubri ca te or replace input
shaft bearing retainer.
Wa rped c lutch disc, or poor facing contact Re place disc.
Weakened torsion springs in clutch disc Replace disc.
Clutch d isc rivets loose Replace disc.
Distor ted pres sure plate or flywheel surfac e Re place clutch cover or f ly-
wheel.
Weakened engine m ount or loose engine mou nting
bolt or nut Retighten or replace mount.
Noisy clutch Worn or broken release bearing Replace release bearing.
Input shaft front bearing worn Replace input sh aft beari ng.
Excessive rattle of clutch disc hub Replace disc .
Cracked clutch disc Replace disc.
Pressure plate and diaphragm sprin g rattling Replace c lutch cover.
Grabbing clutch Clutch disc facings soaked with oil Replace disc.
Clutch disc f a cings excessively worn Replace disc.
Riv et heads standing out from f acing Replace disc.
Weakened torsion springs Replace disc .