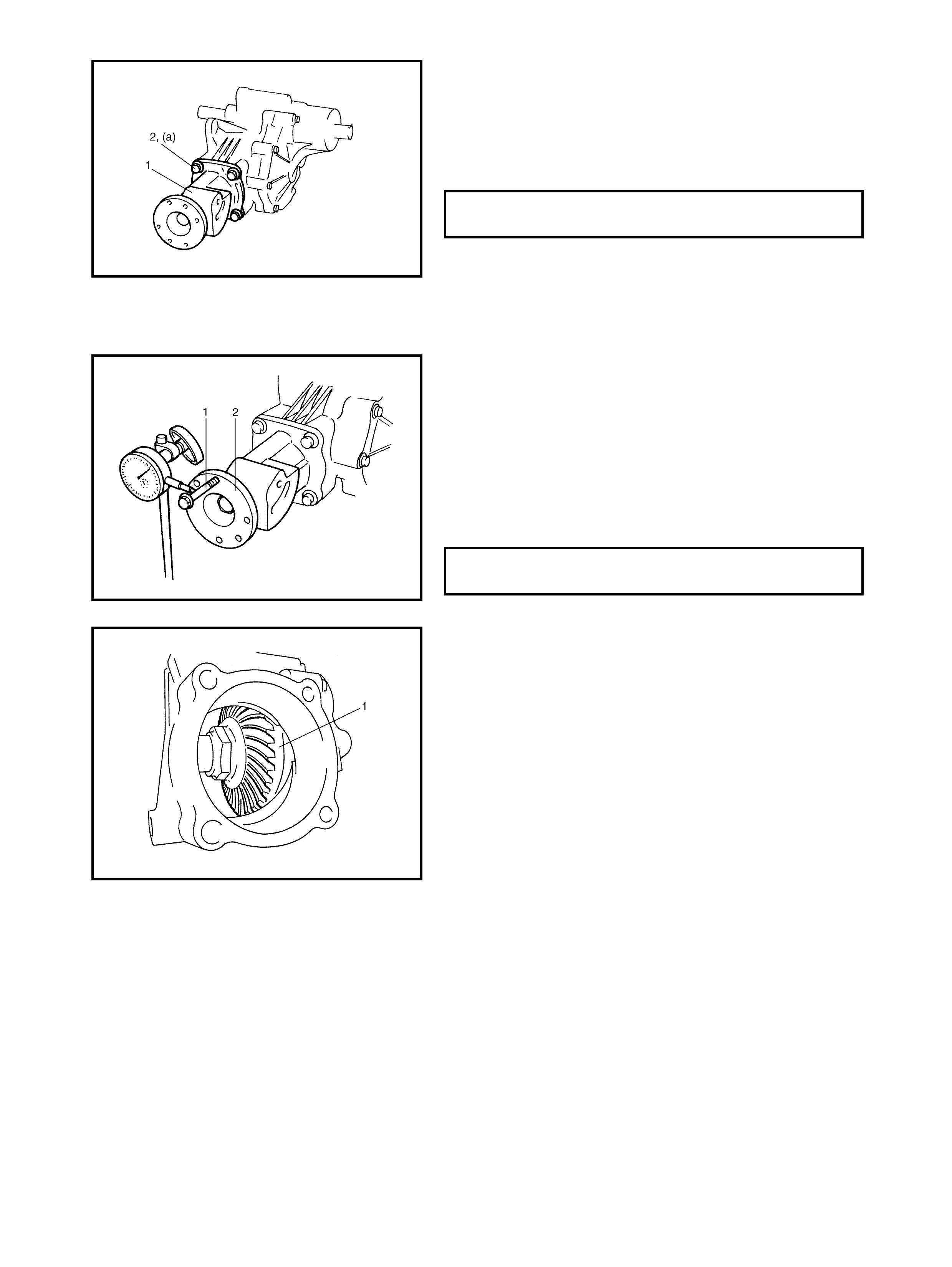
3. Install the bevel pinion shim(s) refer to 4.4 UNIT
ASSEMBLY, TRANSFER OUTPUT RETAINER
ASSEMBLY AND ADJUSTMENT in this Section. Install
the transfer output retainer assem bly (1) to the transfer
case and tighten the retainer bolts (2) to specified
torque.
4.5 BEVEL GEAR BACK LASH
MEASUREMENT
1. Install a bolt to the bolt hole of flange (2), set a dial
gauge measuring tip at right angles to the bolt (1) as
shown in the figure.
Note the measurement of the backlash of the pinion
and bevel gear.
NOTE: If the backlash exceeds specification given below,
replace the bevel pinion shim (between the transfer case
and the transfer output retainer) and measure backlash
again.
2. Finally, check gear to oth contact as follows.
NOTE: When applying red paste to teeth, be sure to paint
tooth surfaces evenly. The pas te must n ot be to o dry or too
liquid.
a. After cleaning tooth surface of bevel gear (1), paint
them with gear marking compound evenly using a
brush or sponge etc.
NOTE: Be careful not to tur n bevel gear mo re than one full
tur n, or it will hinder the accuracy of the test.
b. Turn the bevel gear until the painted section
meshes with the bevel pinion gear. Tur n it back and
forth by hand to repeat the contac t.
c. Rotate the gear until the painted section is visible
and ch eck the contact pat ter n, refer to the following
chart.
If the contact pattern is not normal, readjust or
replace as necessary
NOTE: If the bevel gear back lash and the bevel pinion
shims are adjusted properly, the correct tooth contact pat-
ter n will be evident.
If the correct tooth contact is still not evident, despite cor-
rect adjustment, there may be abnormal tooth wear or
transfer case or retainer damage. Check each component
and replace as necessary.
TRANSFER OUTPUT RETAINER
BOLTS (a) 50 Nm
TRANSFER PINION AND BEVEL GEAR
BA CKLASH 0.1 - 0.2 mm