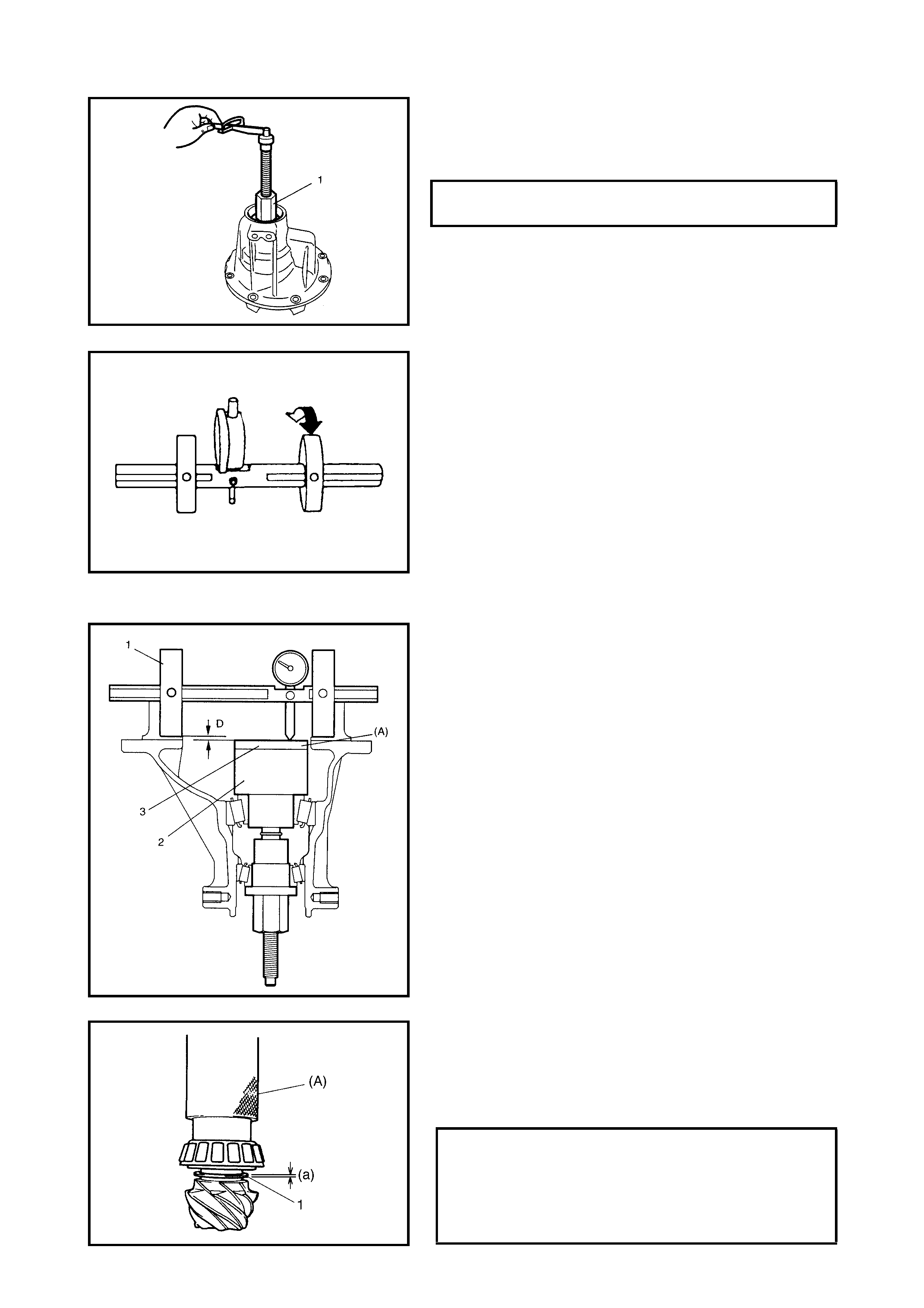
NOTE:
Before taking measurement, check rotation by
hand for more than 15 revolutions.
6. Tighten the bevel pinion nut using special tool (1) so
that the specified bearing preload is obtained.
NOTE:
• When setting the dial gauge to the bearing form
dummy with dummy sh aft, tighten the screw l ightly. Be
careful not to overtighten it, which will cause damage
to the dial gauge.
• With the dial gauge set, turn the dummy back and forth
by hand several times and attain accurate 0 (zero)
adjustment.
• It is desira ble that th e short pointe r indicates bey ond 2
mm when long one is at 0 (zero).
7. Set the dial gauge to the bearing form dummy with
dummy shaft and make 0 (zero) adjustment on the
surface plate.
8. Put the block dummy (3) on the pinion form dummy (2),
special tool
09922-76510 (A)
.
NOTE:
• Repeat turning dummy back and forth and measure
the distance of the top surface of the block dummy
accurately.
• When the dial gauge measuring tip extends from 0
(zero) position, pointer turns counter-clockwise.
• The measured value may exceed 1 mm. Therefore, it
is also necessary to know the reading of the short
pointer.
9. Place the zero-adjusted bearing form dummy with
dummy shaft (1) and dial gauge set on the block
dummy (3) and take a measurement between zero
position and extended dial gauge measuring tip.
10. Obtain adjusting shim thickness by using the measured
value of the dial gauge in the following equation.
Required Shim Thickness = Dial Gauge Measured Value D
11. Select adjusting shim(s) (1) closest to the calculated
value from among the following available sizes.
12. Fit the shim(s) and then press-fit the rear bearing with
special tool
09940-51710 (A)
.
DRIVE BEVEL PINION BEARING
PRELOAD @ 50 rpm 0.5 - 1.3 Nm
AVAILABLE SHIM THICKNESS (a)
0.30, 1.00,
1.03, 1.06,
1.09, 1.12,
1.15, 1.18,
1.21, 1.24,
1.27, 1.30 mm