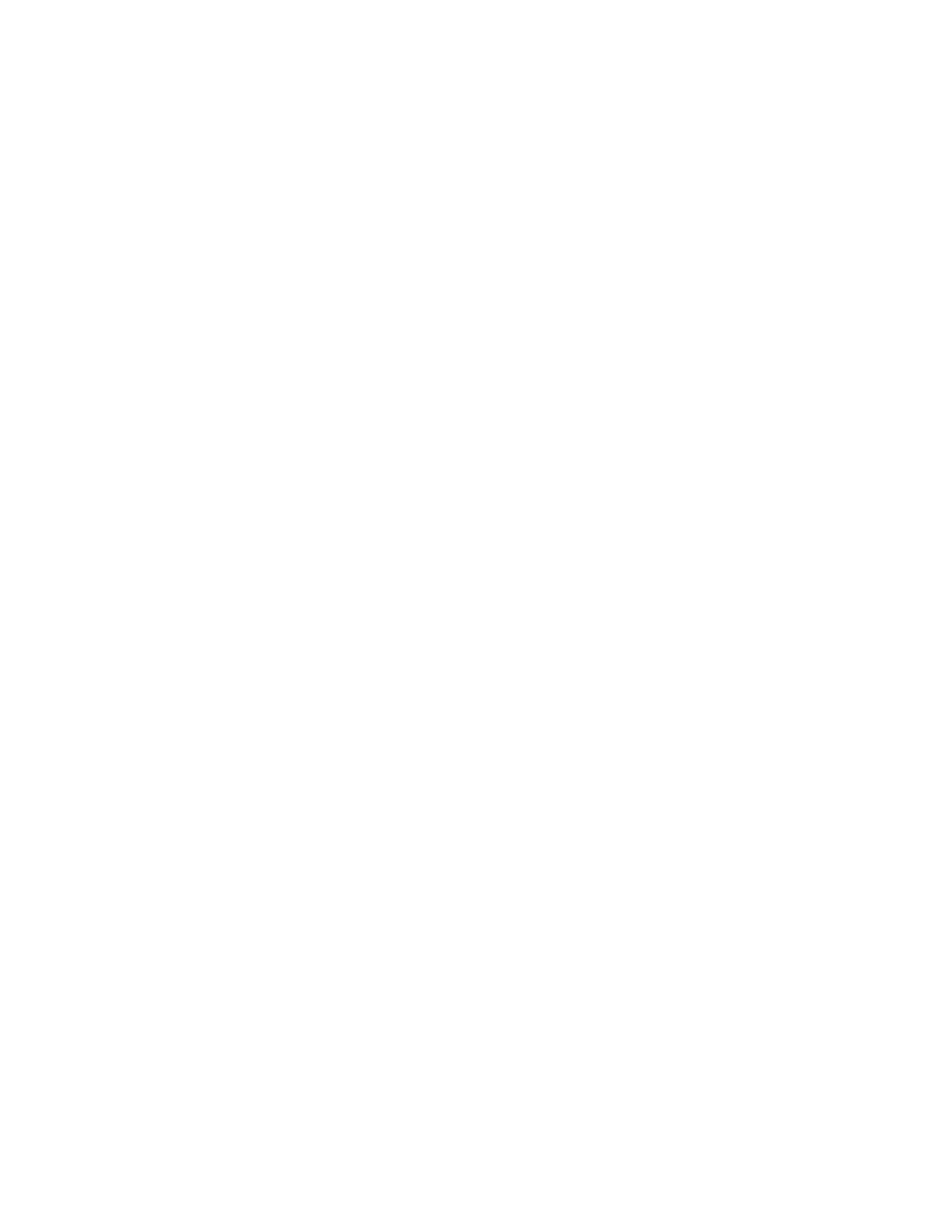
7. PAINT AND COATINGS
7.1 ANTI-CORROSION TREATMENT
WARNING: Standard shop practices, particularly eye protection, should be followed during the per-
forming the operations below to avoid personal injury.
To improv e th e c or rosi on res is tance of the body st ru ctu re, one or tw o side d gal v ani se d st eel she et i s used . In
addition, the following anti-corrosion measures are used:
• Steel sheets are treated with cathodic electroprimer which has excellent corrosion resistance.
• Rust proof wax coatings are applied to the inside of doors and side sills where moisture is likely to remain.
• Vinyl coating is applied to the underside of the body and to the inside of the wheel housing.
• Sealant is applied to door hems and panel joints to prevent water penetration and resulting rust.
When panels are replaced or there is collision damage repair, leaving the relevant area unt reated will leave
the area s usceptib le to cor rosion . There fore, it i s an es senti al func tion o f a ny repair operat ion to cor rectly re-
coat the relevant surfaces.
All metal panels are coated with metal conditioners and primer coating during vehicle production. Following
repair and/or replacement part installation, every accessible bare metal surface should be cleaned and coated
with rust proof primer. Perform this operation prior to the application of sealant and rust proof wax coating.
Sealan t is a ppl ied to t he s pec i fic joints of a v eh ic le durin g pr od uc tio n. T he se al ant is int ended to pr ev ent dus t
from ente ring the veh icle and also serves as an anti- corrosion bar rier. The seala nt is applied to the do or and
hood hem areas and between panels and must be correctly resealed if damaged. Reseal the joints of new
replacement panels and reseal the hem area of a replacement door or hood skins.
Use a quality sealant to seal flanged joints, overlapping joints and seams. The sealant must have flexible
characteristics and be able to be painted after it is applied to repaired areas.
Use caulking material to seal op en joints. Select the correct sealant for the situation and the purpose for its
use. Observe the manufacturer’s instructions when using the sealant.
In m any instances, wh ere repaired sectio ns requir e painting, fo llow the n ormal tech niques fo r finish prepara-
tion, colour painting and undercoating build-up.
Rust proof wax, a penetrative compound, is applied to metal-to-metal surfaces (inside doors and side sills)
where i t is di fficult t o use no rm al u nde rc oa tin g met hod s. S el ec t the cor r ect, pe netr at iv e rus t pr oof w ax f or this
application.
When undercoating (vinyl coating) underbody areas, care should be taken to keep engine related parts, shock
absor ber mo unts and mov ab le parts free fro m se al ant. Fo ll owin g un der -co ati ng, e ns ure tha t body dr ai n ho les
remain open.
The correct sequence for the application of anti-corrosion materials is as follows:
1. Clean and prepare the metal surface.
2. Apply primer.
3. Apply sealant (all joints original ly sealed).
4. Apply colour in areas where colour is required such as hem flanges, exposed joints and under body
components.
5. Apply anti-corrosion compound (penetrative wax).
6. Apply undercoating (rust proof material).