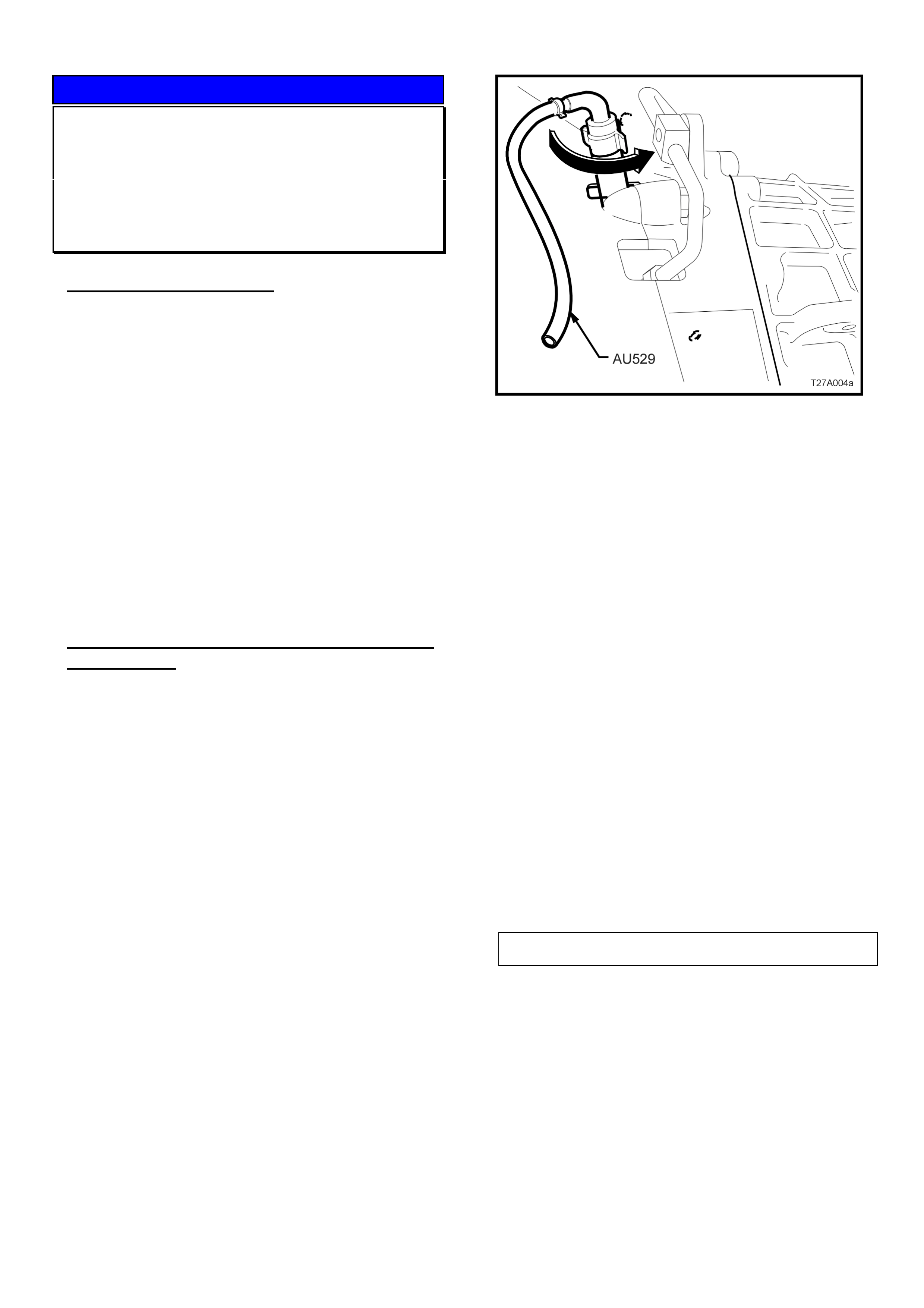
HOLDEN SERVICE TECHLINE__________________________________________________________________MARCH, 2003
14
SERVICE PROCEDURE
Clutch Pedal “Low” – Correct Bleeding
Procedure
V car with Gen III V8 & M/T
(GROUP 7A) TL456-0303
PROBLEM DESCRIPTION
Some retailers have reported difficulty in bleeding
Gen III V8 clutch hydraulic systems, and repeat
customer complaints of “low clutch pedal”, or “hard to
engage gears”.
The cause of these complaints is under investigation.
A number of vehicles have not displayed this
complaint condition until the hydraulic system has
been disturbed during clutch or transmission removal.
During investigation of returned components, it
appears that various methods of bleeding are being
used - with some methods being unsuccessful or
creating aeration of clutch hydraulic fluid.
Because of this, the following SIP procedure has
been repeated in this Techline and is recommended
for use whenever a Gen III V8 clutch hydraulic
system requires bleeding.
CLUTCH HYDRAULIC SYSTEM BLEEDING
PROCEDURE
The clutch hydraulic system must be bled whenever
the hydraulic line has been disconnected, or when a
leak has allowed air to enter the system. Air trapped
in the system can prevent full disengagement of the
clutch.
During bleeding operations, the master cylinder
reservoir must be kept at least half full with hydraulic
brake fluid.
1. Carefully clean any dirt from around the fluid
reservoir cap.
2. Remove the filler cap and top up reservoir as
required, with heavy duty hydraulic brake fluid,
such as Super DOT 4 Plus.
3. Using an 11 mm, 3/8 drive socket, short
extension and socket bar, loosen the slave
cylinder bleeder, located in the upper aperture of
the transmission adaptor plate/clutch housing, on
the left hand side.
4. Then, using just the socket and extension,
tighten the bleeder, using light finger force only.
5. Insert the end of the rubber tube of Tool AU529
over the end of the bleeder, positioned at the 9
o’clock position.
6. With the other end of the bleeder tool inserted
into a clean glass container such as a jar, that
has been partially filled with new brake fluid, open
the bleeder 1/4 turn, using the rubber on the
bleeder tool to provide the required grip. Ensure
that the end of the hose always remains
submerged in the brake fluid during bleeding
operations.
7. Using an assistant, slowly depress the clutch
pedal by hand, one single time and, while holding
the pedal depressed, close the bleeder using
Tool AU529. Once the bleeder is closed, the
clutch pedal can be allowed to slowly release.
(ENSURE PEDAL FULLY RETURNS TO THE
“UP” POSITION – lift by hand if required). Repeat
this process until all bubbles cease to appear at
the end of the bleeder hose.
NOTE: Do not pump the clutch pedal
repeatedly during bleeding operations, as
entrapped air will cause the fluid to foam,
making air removal extremely difficult. Also, as
the hydraulic steel piping is routed over the top
of the transmission housing, air can be trapped
in that section.
8. When all air has been removed, close off the
bleeder and remove Tool AU529. With the clutch
pedal still depressed, tighten the bleeder screw to
the correct torque specification.
CLUTCH SLAVE CYLINDER BLEEDER SCREW
TORQUE SPECIFICATION 18 Nm
9. Once all bleeding operations have been
completed, ensure that the reservoir fluid level is
correct.
NOTE 1: “Alternative methods” of bleeding as
mentioned in SIP should not be used on any vehicle
where repeated air entry type symptoms have been
identified. This is to ensure air entry does not occur
during the use of these methods. Only use these
methods as a ‘last resort’.
NOTE 2: Discolouration of fluid is no reason for
replacement of fluid – Refer Service Techline in Issue
3, March 2003.