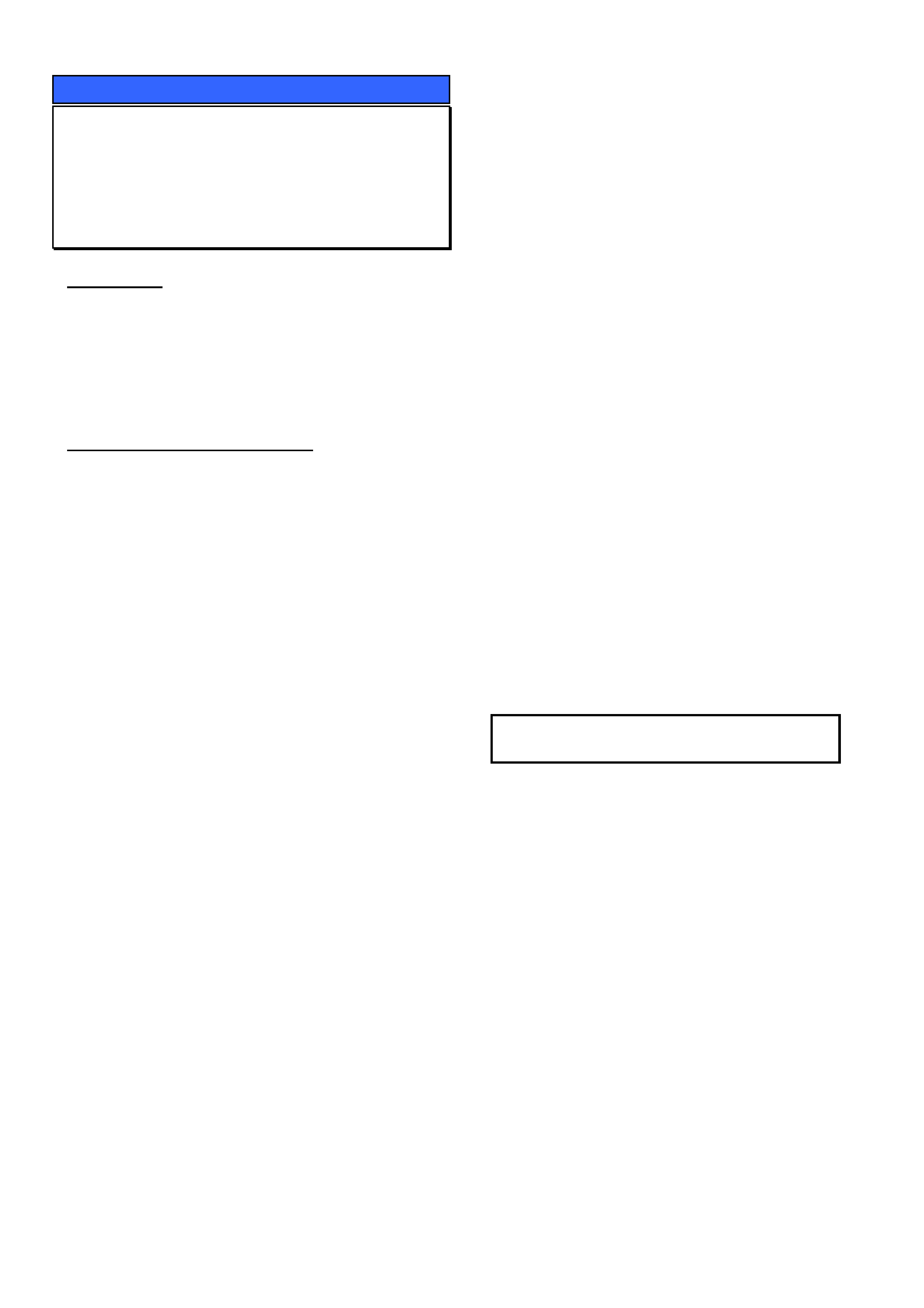
HOLDEN SERVICE TECHLINE _________________________________________________________________AUGUST, 2004
10
SERVICE PROCEDURE
A/T Cooler Flush & Flow Rate Check
Requirement
V & W – with A/T
(Group 7B) TL0748-0407
CONDITION
Returned parts analysis shows that there is often
debris from failed transmissions causing cooler
blockages.
Failure to reverse flush, and carry out a transmission
cooler flow rate check may result in a repeat
transmission failure, if a cooler blockage exists.
SERVICE RECOMMENDATION
It is recommended that Service Managers, Workshop
Controllers or Service Advisors advise technicians to
perform a cooler flush and flow rate check by adding
the wording “Cooler Flush & Flow Rate Check
Required” to Repair Orders whenever:
• a changeover or replacement transmission is
installed.
• fluid contamination is suspected.
• whenever the oil pump and/or torque converter is
replaced.
All Service personnel should take note of the following
statement which is repeated from the All Dealer Letter
on SRTA Auto/Trans. replacement (DL 40/00). Pay
particular attention to the charge-back expense that
may result from NOT flushing and flow rate checking
a transmission.
“Dealerships are required to flush and flow rate check
the vehicles’ auto. trans. cooling circuit when
changing a transmission. Lack of cooler flush and flow
rate checking has resulted in repeat transmission
replacements. In addition, cooler flow restrictions
result in specific heat damage to components and
gear failure due to restricted lubrication, which is
obvious during transmission teardown at the SRTA
remanufacturing facility. Any transmissions returned
to SRTA which exhibit extreme damage such as this,
may be subject of cost recovery from SRTA, of the
remanufacture cost and the replacement of
transmission components – current cost is $2800.00+
per transmission.
----------------------------------------------------------------------
Following is a copy of reverse flush and flow rate
checking procedure from Passenger Vehicle SIP.
2.1 TRANSMISSION COOLER REVERSE
FLUSH AND FLOW RATE CHECK – ALL
LT Section No. – 04-200
IMPORTANT: It is essential that a reverse flush and oil
cooler flow rate check is performed, after ANY of the
following situations:
• Transmission is replaced.
• Fluid contamination is suspected.
• Whenever the oil pump and/or torque converter is
replaced.
NOTE: The reverse flush must be completed prior to
conducting a flow rate check.
Reverse Flush
The recommended procedure for reverse flushing the
transmission cooler and lines, particularly after an
overhauled or replaced transmission has been installed
into the vehicle, is as follows:
1. Disconnect both cooler lines at the transmission and
at the radiator cooler end. Refer to 3.15 TRANSMISSION
COOLER PIPES/HOSES, in this Section. Do not lose the
pipe to fitting sealing washer, when the pipe is removed.
2. Carefully check the cooler inlet fitting (lower) to see
whether any material is evident at this point. If so, dislodge
and remove with a suitable tool and/or compressed air
blown in the reverse direction through the cooler.
3. Using a commercially available pressure spray gun
and clean solvent, such as white spirit:
a. Back flush through both cooler lines.
b. Back flush through the cooler, including an external
cooler (if fitted).
c. Blow compressed air through return and inlet pipes
to remove solvent.
d. Flush pipes with transmission fluid.
4. Check the cooler pipe to cooler fitting, sealing
washers for damage, replacing as required.
5. Reconnect cooler lines to the transmission and
cooler but leave the cooler return line to transmission
connection open.
6. Conduct a flow rate test as described below, to
ensure that any restriction has been cleared.
7. If flow rate is satisfactory, reconnect the return line to
the transmission quick connect fitting.
8. Tighten the cooler pipe flange buts at the cooler end
(V6 engines only) to the specified torque. Refer to 3.15
TRANSMISSION COOLER PIPES/HOSES, Reinstall for
the correct procedure.
OIL COOLER PIPE TO RADIATOR FITTING TORQUE
SPECIFICATION V6 Engines
25 Nm
9. Lower vehicle and check fluid level as detailed in 2.1
FLUID LEVEL CHECK, in this Section.
FLOW RATE CHECK
IMPORTANT: Do not run engine any longer than absolutely
necessary, as too low a fluid level can cause aeration and
foaming.
1. When installing the transmission assembly, leave the
cooler return line disconnected from the transmission
(upper fitting).
2. Ensure that the fluid level is to the ecommended
level, as detailed in 2.1 FLUID LEVEL CHECK, in this
Section.
3. Place a container underneath the disconnected
cooler line.
4. With the selector lever in the Neutral position, start
the engine and observe the fluid flow into the container,
after all air bubbles have ceased and a steady flow is
evident. Measure the flow rate.
Result: The fluid flow rate should be approximately 0.7 litre
in a 20 second period, with cold automatic transmission
fluid (ATF). With ATF at normal operating temperature (86
– 93° C), the flow rate will increase and should be
approximately 1.2 litres in a 20 second period.
If the flow rate is less than this specification, the source of
the restriction must be located and rectified. Possibilities
are either radiator tank cooler, faulty flexible hoses and/or
external cooler (if fitted).
5. Reinstall the cooler return line to the transmission
quick connect. Refer to 3.15 TRANSMISSION COOLER
PIPES/HOSES, Reinstall for the correct procedure.