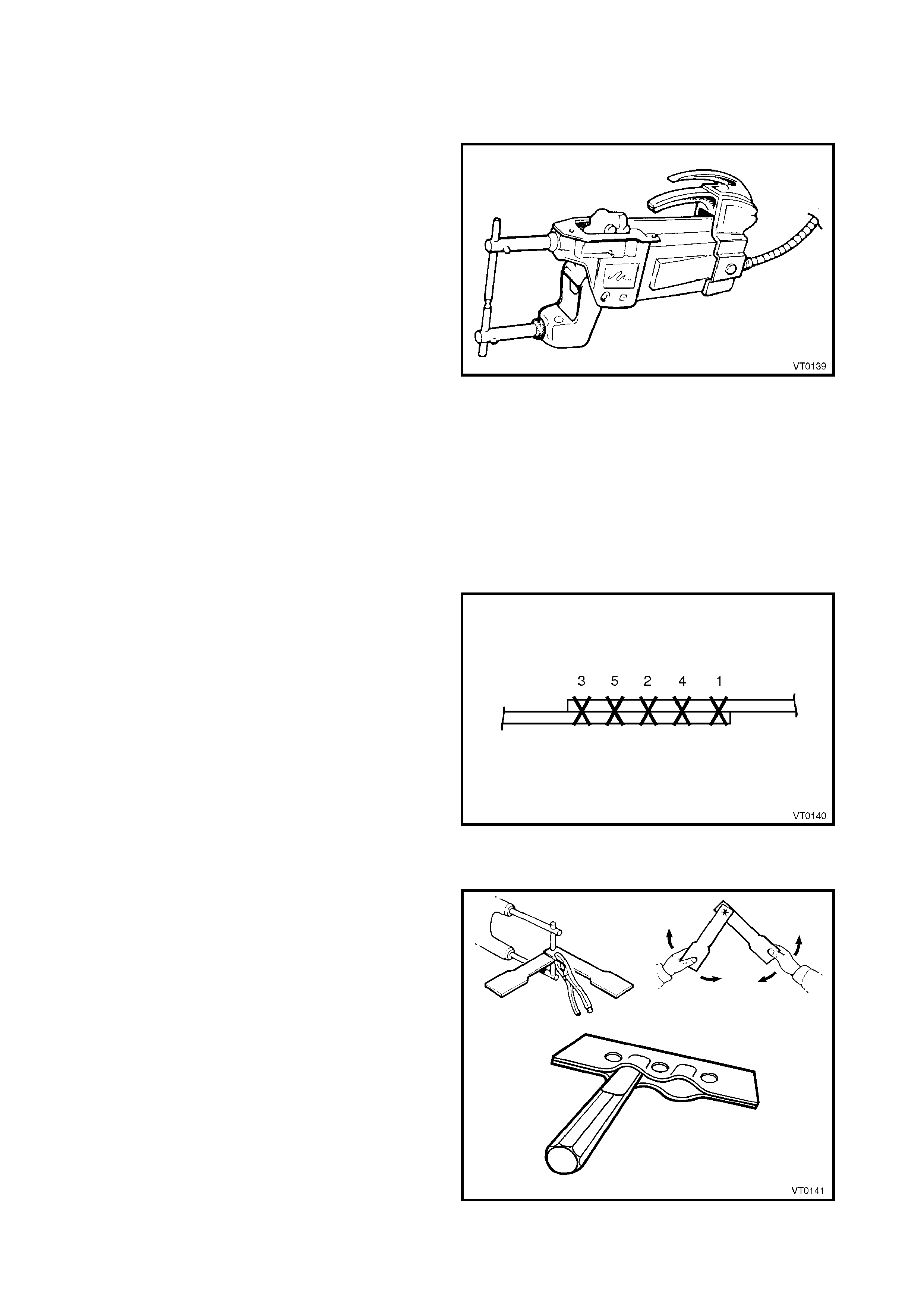
The efficiency of the spot welding operations during the repair will control the strength and durability of the
finished vehic le. It is recom m ended that the following points be adhered to in or der that a high quality of welding
is achieved.
SPOT WELDER
1. The spot welding machine should be adjusted for
the minimum length of arm appropriate to the
particular weld, so that maximum clamping
pressure is available.
2. The electrode tips should be aligned to be parallel
and on the same axis to maintain maximum
pressure and weld alignment.
3. The correct welding tips should be employed as
per Table 1 on the previous page.
Figure 1-27
PANEL CONDITION
1. The panel surface must be free of paint film, rust, dirt and other contaminates so that current flow will be
sufficient for proper fusion.
2. The m ating surfac es should be prepared suc h that there are no gaps between the surfaces . Current flow is
reduced considerably by poor contact.
3. All mating surfaces must be treated with a weld through primer to prevent corrosion in this inaccessible area.
The correct primer has high conductivity to facilitate the weld. Refer to 5 BODY SEALING, ADHESIVES &
DEADENERS in the following Sections, 3A – Sedan, 3B – Wagon, 3C – Utility or 3D – Coupe.
NUMBER OF WELDS
1. The same number and similar position of spot
welds should be used when replacing the panel, as
was used during manufacture. It is important to
maintain the original structural strength of
the vehicle, par ticular ly because of the implications
in deployment of the SRS system. Refer to
Section 2, PRECAUTIONS in this Supplement for
further information on the SRS.
2. The required spot weld diameter is specified in
Table 1, earlier in this Section.
3. Spot welding too closely spaced weakens the
welds due to the shunt effect of the current. Apply
a non-sequential welding procedure.
Figure 1-28
WELD TESTING
1. Prior to welding, two (or more) pieces of same
thickness panel should be test welded, using the
intended weld settings. The weld should then be
destroyed by twisting the pieces. If the settings are
correct, there should be a weld button (nugget)
pulled out of one test piece with the dimensions
recommended. If not, the weld settings must be
adjusted, and the test repeated.
2. Completed weld sections may be tested using a
hammer and chisel (or flat bladed screwdriver).
The testing should cease once the size of the
nuggets can be determined, and the welds should
still be intact.
NOTE: The test section must be returned to the
correct shape after testing.
Figure 1-29